Want to Discuss Your Upcoming Product Line?
Hinah coating will help you get things done.
Email us
Tel (Whatsapp/Wechat)
+86-186 3213 8668
Powder Coating Curing Oven
Advanced technology, energy saving, high efficiency.
Curing oven system. Divided into bridge type, tunnel type, and box type curing oven, batch curing oven.
The curing oven is one of the most important equipment in the production line of powder coating equipment, and its temperature uniformity is an important index to ensure the quality of the coating.
The heating way of the oven is radiation, hot air circulation and electricity, coal, bio-particles, diesel, natural gas, etc. According to the production plan can be divided into single and through type. The equipment form has straight through and bridge type. Hot air circulation oven has good heat preservation, uniform temperature in the furnace, and less heat loss. After testing, the temperature difference in the furnace is ± 3℃, reaching the performance index of the similar products of the advanced countries.
The oven inside and outside is made of galvanized plates 0.6mm, the middle is 150mm rock wool board.

Type1: Tunnel Curing Oven
Advanced technology, energy saving, high efficiency.
• Tunnel furnace is suitable for slender products such as pipes, aluminum profiles, support columns, etc.
• Heating source: natural gas/liquefied petroleum gas/diesel/electricity, etc.
• Wind curtains are installed at both ends of the tunnel furnace to prevent heat loss and save fuel. This is a patent of Hinah Technology.
• Heat distribution in the furnace is uniform, and the temperature difference is controlled within ±3°
• Fast heating speed and high efficiency
• International brand, high safety
Features
Tunnel Curing Oven
● Tunnel-type curing ovens are designed with a conveyor belt system that moves workpieces through a tunnel-shaped chamber.
● The oven is typically long and narrow, with the conveyor belt running through the center of the chamber.
● Heating elements are positioned along the walls or ceiling of the tunnel to provide consistent heat distribution. And wind curtain at both ends to efficiently prevent heat loss in the oven.
● Tunnel-type ovens are well-suited for continuous production lines with high throughput requirements.
A reasonable heat ventilation system design makes air circulation perfectly balanced and keeps the furnace temperature stable. Gas burner type, 100% of heat flows into the furnace, high efficiency, and no waste.
Tunnel ovens can be built directly on the ground, which is relatively cheaper than bridge curing ovens, but their thermal insulation is relatively weak due to heat conversion. This design is more suitable for long workpieces rather than wide workpieces. If the tunnel door is too wide, the air curtain will not be strong enough for heat conversion, which will cause heat loss, slowing down the oven heating speed and increasing electricity bills.
If you choose the power and free conveyor system, the tunnel oven will be suitable for it.

Type2: Bridge Curing Ovens
Advanced technology, energy saving, high efficiency.
- Same Heat Distribution: The temperature is kept consistent and the temperature difference is controlled within ±3°. This uniformity is the key to stable quality;
- Adjustable: It can be designed to suit different sizes, and shapes of products, meeting various requirements.
- Save Energy: Hot air flowing around the top area will not convert with the cold air outside, thereby reducing energy consumption.
- Save Labor Cost: Workers can go directly through under the oven, reducing the walking path.
- Save Space: The burner chamber will be installed under the oven, occupying a smaller space than tunnel-type oven.
Features
Bridge Curing Ovens

Type3: Box Curing Ovens
Advanced technology, energy saving, high efficiency.
- Economical, stable and durable;
- Occupy a small space;
- Easy to operate and maintain;
- Suitable for small-scale and small workpieces.
Features
Box Type Curing Ovens (altname batch curing oven)

The Heating system of the oven
Advanced technology, energy saving, high efficiency.
- The heating system mainly consists of a chamber, burner(heating exchanger), hot air circulating fan, air ducts, etc;
- Heating Sources: Gas /LPG/ Diesel / Electricity and so on, optional;
- Our burner is fast heating, has high efficiency, and is equipped with proportional adjustment, and frequency conversion. International brand: Riello;
- The heating chamber is installed on the oven’s left and right side(according to the plant layout), with the oven body as a connected structure;
- The heating chamber has a maintenance door, easy to maintain, and can be used as the new air inlet for quickly reducing the oven temperature.
Features
The Heating system of the oven
Temperature Control System
(1) It is made up of a temperature measurement system, temperature control system, and over-temperature alarm system.
It’s through the sensor, digital temperature controller, and AC contactor control device that automatically complete the whole process of temperature measurement and control.
(2) The oven tunnel control system is measured by the temperature sensor signal by the digital temperature controller with the set temperature value (Analog) comparison of the output command signal to control the working state of the heater, so as to achieve the temperature control/display.
Hot Air Circulation Fan
(1) The circulating hot air is fed into the air supply pipeline of the drying channel through a circulating fan, and then the air outlet pipe is evenly distributed in the passage through the air outlet, there is a damper adjusting device to ensure the uniformity of the air supply.
(2) All hot air circulation air ducts are arranged in the passage, and the air supply duct and the air outlet are all made of 1.0mm galvanized sheets
(3) Hot air circulation mode: using bottom air supply, upper air return.
Proven
30 years of experience providing proven equipment
Lifetime Service
Maintenance is more important than repair
Maximum Efficiency
Production line capacity fully matches demand without wasting any resources
Contact Us -- Free Design & Order Equipment Calculation
Order Equipment Calculation
In Order To Provide You With The Best Solution, Please Tell Us The Following Information
● Factory Dimensions (length, width, height)
● Work Piece Output (1 day = 8 hours, 1 month = 30 days)
● Material of the workpieces
● Dimensions of work piece
● Weight of the workpieces
● Color Change Demand (Frequency)
We closely communicate with clients to understand their needs and provide tailored solutions. Once the solution fits their requirements, we customize the production of the powder coating line to help them adapt to their specific production environment and coating needs.
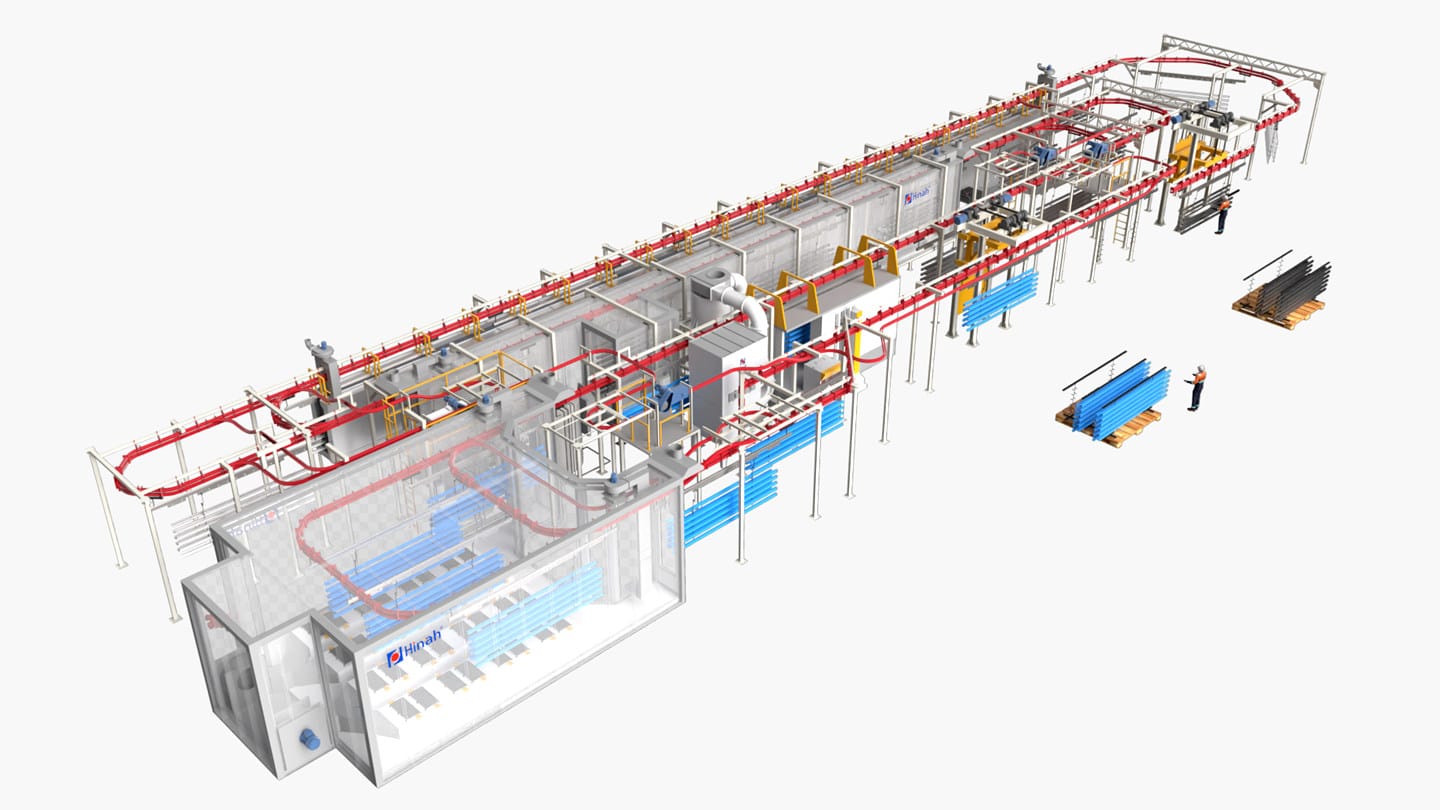
/CONTACT US
Want to Discuss Your Upcoming Product Line?
Hinah coating will help you get things done.
Email us
Tel (Whatsapp/Wechat)
+86-186 3213 8668
Learn How We Helped 1000+ Customers Gain Success.