The automated powder coating line uses automated equipment to complete the powder coating process, widely applied in surface treatment of metals, plastics, and other materials. Compared to traditional manual spraying, the automated production line increases production efficiency, ensures consistent coating quality, and reduces human error. Understanding the automated powder coating line price is crucial for buyers. The price is influenced by factors such as scale, automation level, and technological configuration. Proper budgeting and choosing the right equipment can ensure the best return on investment. Therefore, understanding the price is key to making an informed purchasing decision.
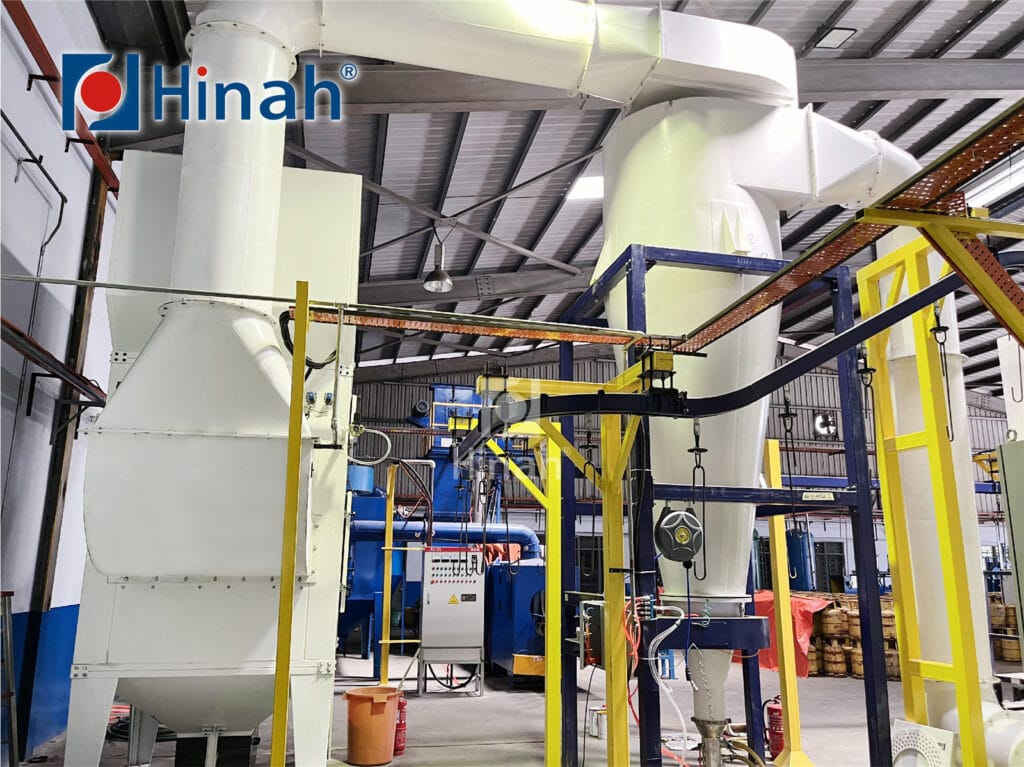
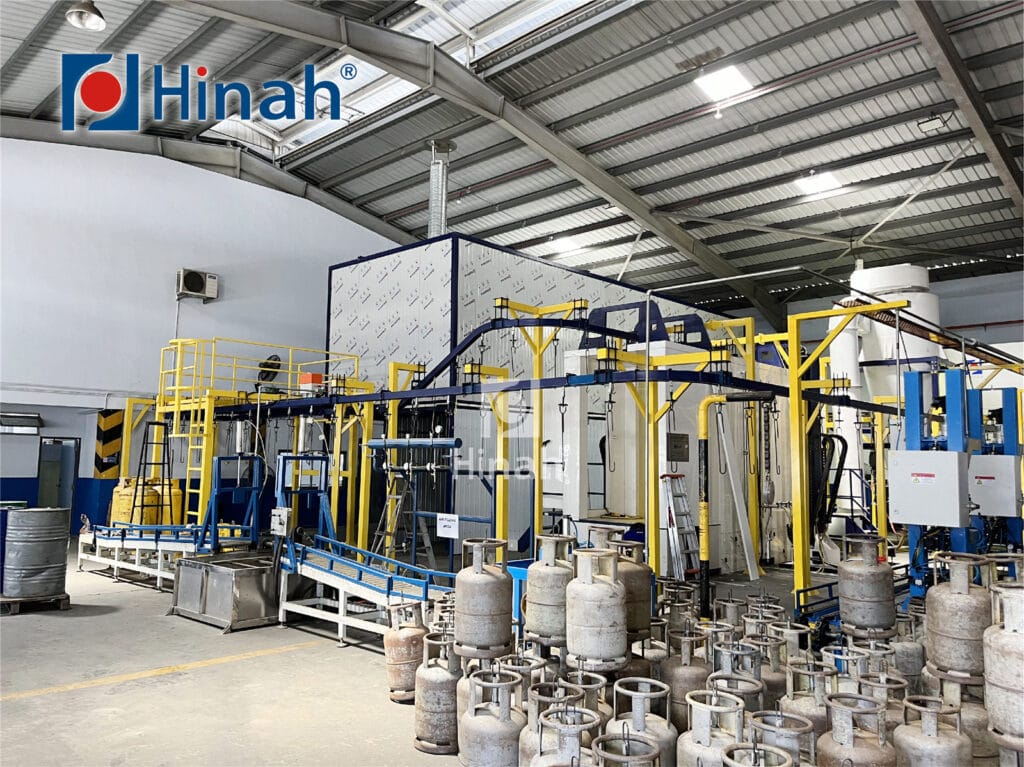
I. What are the key parts of the automated powder coating line?
The automated powder coating line usually consists of the following key parts:
1. Powder Coating Robot
The powder coating robot sprays the powder coating evenly onto the surface of the workpiece to ensure uniformity and accuracy of the coating. It automatically performs the spraying process through a precise control system and a robot arm, improving production efficiency and reducing material waste.
2. Powder Coating Conveyor System
The conveyor system moves the workpiece to be coated from one work area to another to ensure the continuity and efficiency of the production process. Common transmission methods include chain, roller, and hanging transmission.
3. Powder Coating Curing Oven
The curing oven is used to heat the sprayed powder coating so that it cures at high temperatures and forms a solid coating. The curing oven usually uses electric heating or gas heating, and the temperature control system ensures that the temperature and time of coating curing are accurate.
4. Powder Recovery System
In order to reduce material waste, the automated powder coating line is usually equipped with a powder recovery system. This system can collect and recycle the unused powder during the spraying process, thereby improving the efficiency of coating use.
5. Electrical Control System
The automated powder coating line is equipped with an advanced control system, usually controlled by a PLC (programmable logic controller) or computer, which can monitor and adjust various parameters in the production process in real-time, such as spray thickness, paint flow, curing temperature, etc.
6. Powder Coating Pretreatment System
Before coating, the surface of the workpiece needs to be cleaned and treated to improve the adhesion of the coating. The pretreatment system usually includes processes such as sandblasting, pickling, and phosphating.
7. Exhaust and Ventilation System
The dust and gas generated during the spraying process need to be effectively discharged through the exhaust system to ensure the safety and air quality of the production environment.
These components work together to enable the automated powder coating line to efficiently and stably complete the production tasks of powder coating.
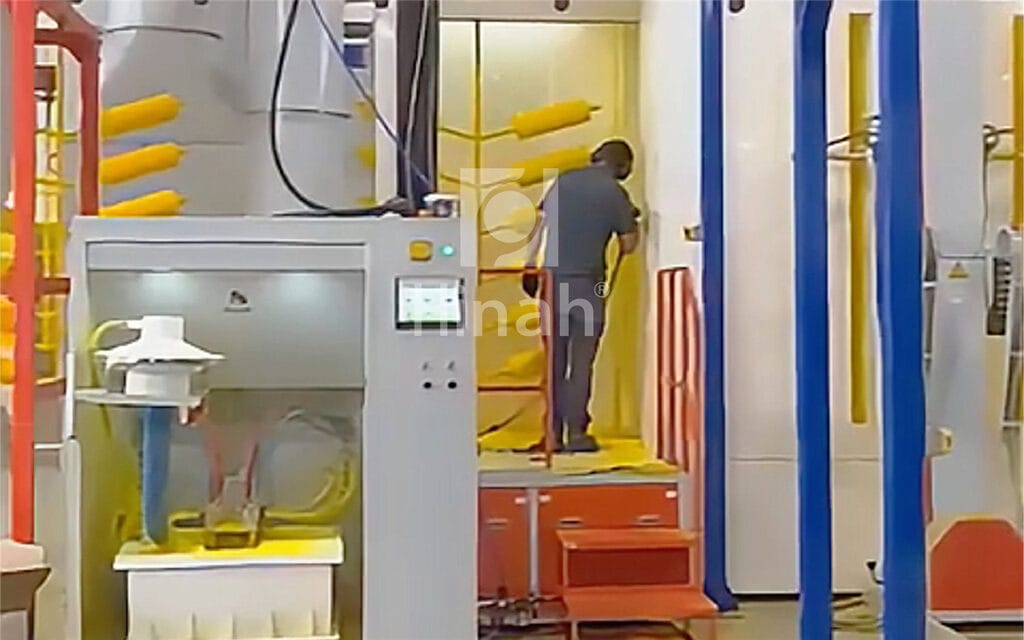
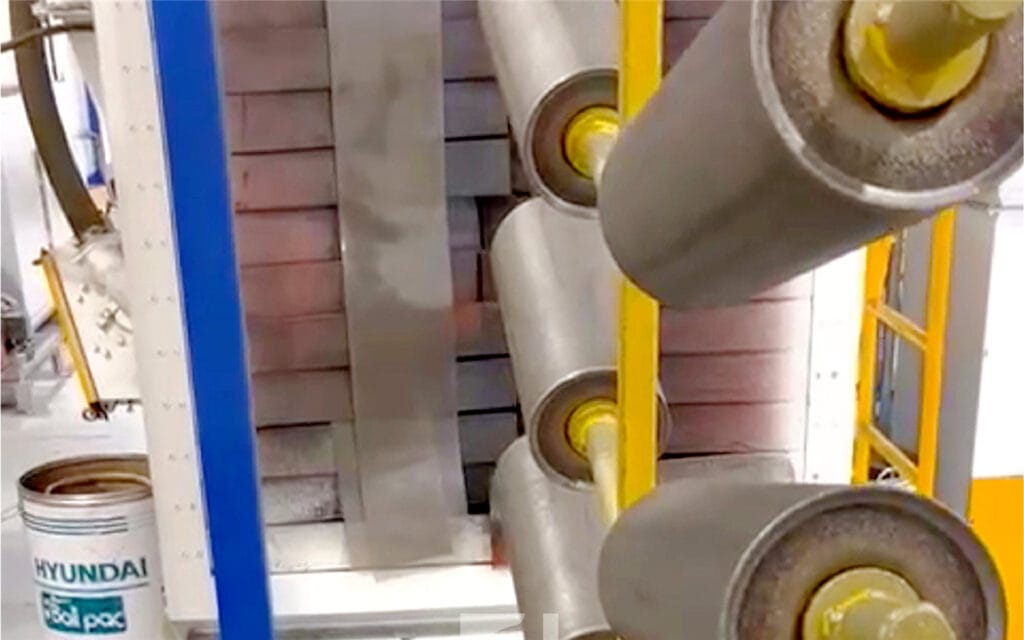
II. What factors affect the automated powder coating line price?
Here are three key factors that influence the automated powder coating line price:
1. Production line scale and output
The size of the production line and the required output directly determine the price. Large-scale production lines typically require more equipment and higher system capacity to handle more workpieces. High-capacity production lines generally cost more because they involve more machinery, space, and energy consumption. In addition, large-scale production lines require stronger automation and higher production speeds to meet higher demand.
2. Degree of automation
The degree of automation is another important factor that affects price. Fully automated powder coating lines are generally more expensive than semi-automated or manually operated lines. Fully automated systems include robotic arms, automatic spraying, coating thickness control, intelligent monitoring, and other technologies. These technologies can significantly improve production efficiency and consistency of coating quality, but also significantly increase the cost of equipment. Although production lines with a lower degree of automation have lower initial investments, they may require more manual intervention and management and have lower production efficiency.
3. Customized needs
According to the production needs of different companies, the customized design of the automated powder coating line will affect its price. For example, customers’ special requirements for workpiece size, coating thickness, spraying technology, etc. may require customized special equipment and functions. These customized features not only increase design and manufacturing complexity but may also require additional equipment and technical support, thereby increasing the price of the production line.
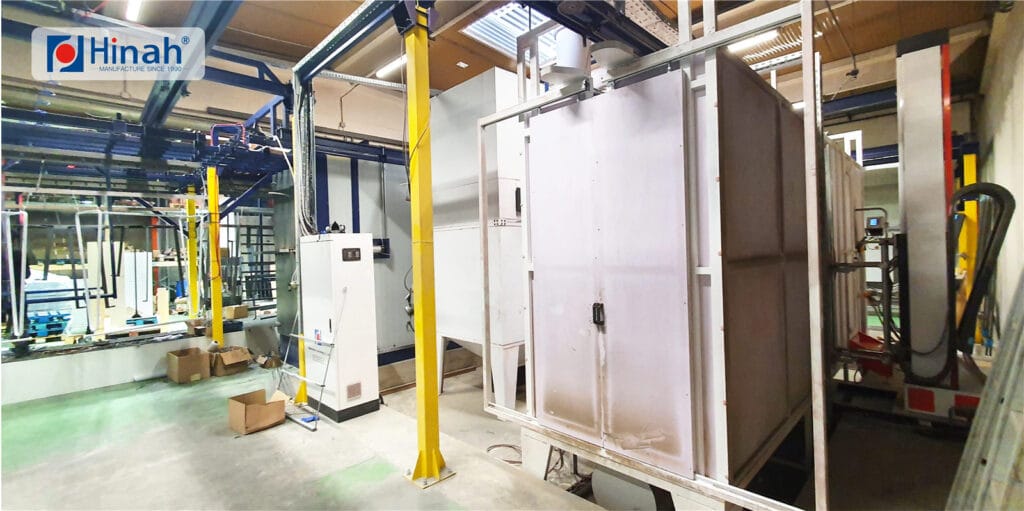
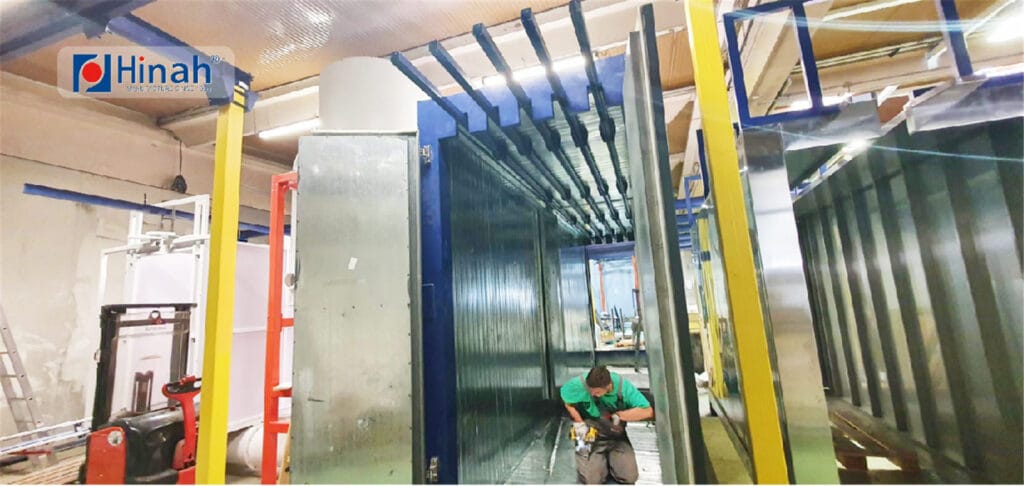
III. How to plan the budget?
1. What are the main costs included in the initial investment?
- Equipment procurement costs: including the purchase of equipment such as powder spraying system, transmission system, curing oven, etc. The price varies greatly depending on the degree of automation and configuration.
- Installation and commissioning costs: including equipment transportation, installation, commissioning and operation training.
- Infrastructure construction costs: installation of necessary infrastructure such as power supply and gas pipelines.
- Paint and material procurement: paint and consumable materials used in the initial stage.
- Software and control system costs: system costs for production line monitoring and control.
2. How to choose the appropriate production line configuration?
- Clear production needs: determine product type, workpiece size, and output requirements, and choose the appropriate production line scale and configuration.
- Evaluate the budget: balance the budget and automation level, and consider phased investment.
- Select the degree of automation: select the appropriate level of automation based on the budget and production needs.
- Consider energy efficiency and long-term costs: select energy-saving and efficient equipment to reduce long-term operating costs.
- Select reliable suppliers: select reputable suppliers to ensure the stability of equipment and after-sales service.
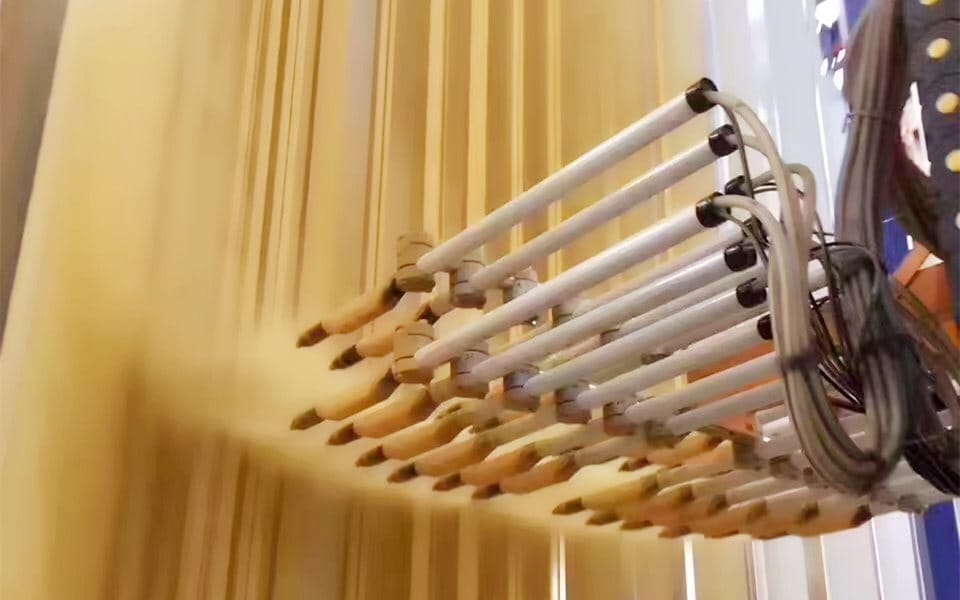
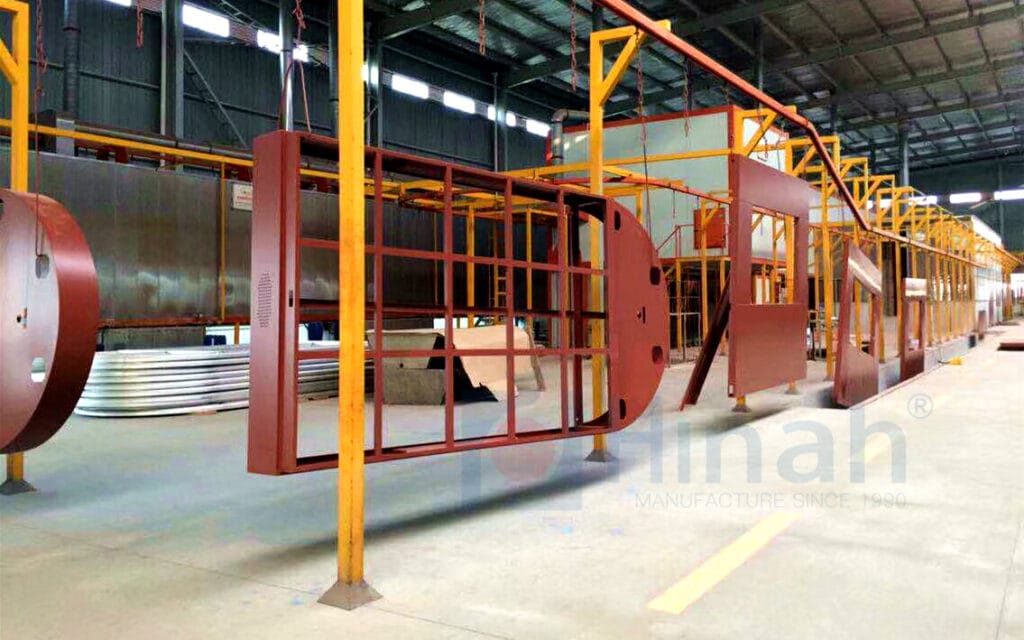
IV. How to maintain and manage the automated powder coating line?
- Regularly check and clean the powder spraying system, nozzles, and conveyor belts to ensure that the equipment is free of powder blockage and jamming.
- Regularly check mechanical parts and powder spraying systems, and replace aging or damaged parts in time.
- Check the control system, regularly update the production line control software, and optimize production efficiency.
- Check power consumption, optimize system settings, and regularly clean air filters.
- Regularly train operators to ensure correct operation of the equipment and timely detection of problems.
V. What is the range of the automated powder coating line price?
The price range is affected by multiple factors, such as the scale of the production line, the degree of automation, and the equipment configuration. Generally, the price range is as follows:
1. Entry-level production line: about $30,000 to $80,000
Suitable for small-scale production, low degree of automation, simple equipment configuration, suitable for start-ups or low-volume needs.
2. Medium-scale production line: about $80,000 to $200,000
Suitable for medium-scale production, with a high degree of automation, capable of handling a wider variety of workpieces, common in medium-sized enterprises.
3. High-end customized production line: about $200,000 to $500,000+
Highly automated and high-precision production lines are suitable for large-scale production and high-demand customers. The equipment configuration is complex and may include customized functions, intelligent control systems, etc.
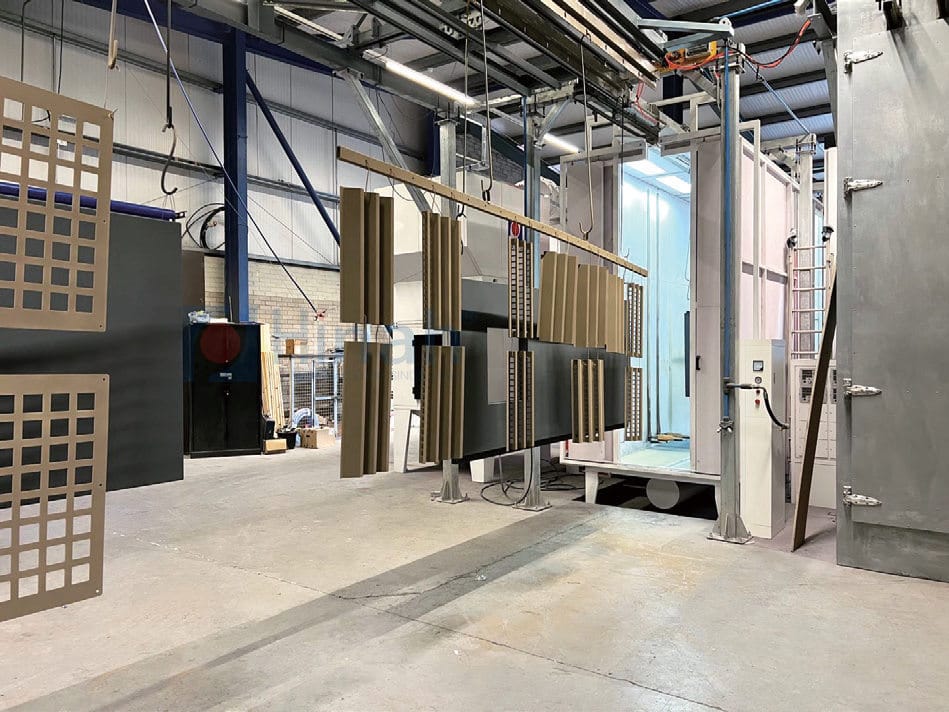
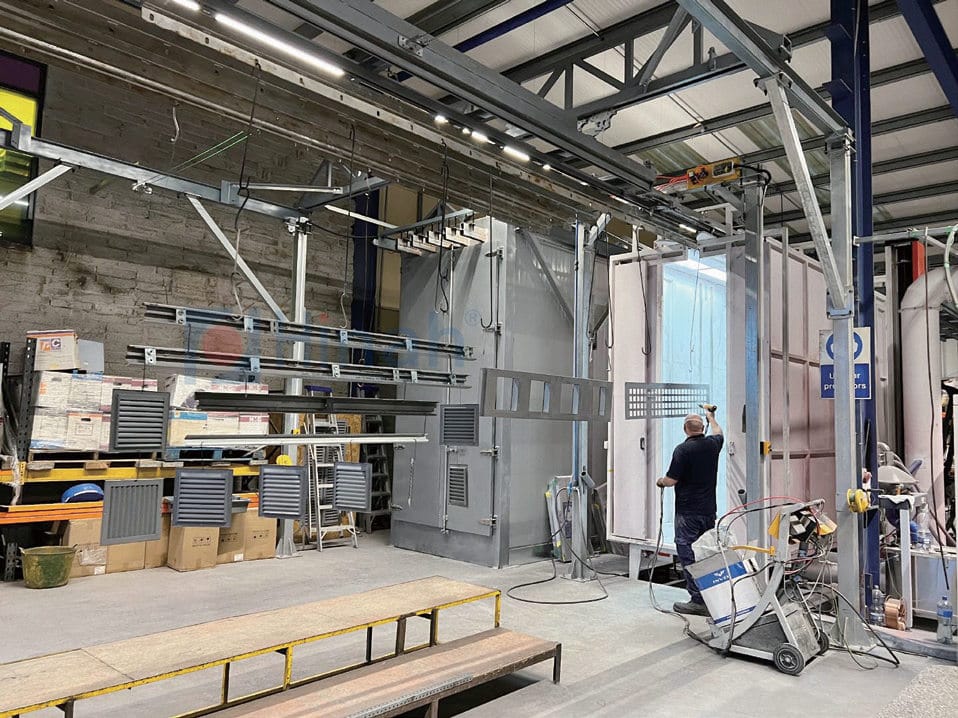
VI. Conclusion
Choosing the most suitable automated powder coating line requires a comprehensive consideration of price and function to ensure that production needs are met and the return on investment is optimized. First, it is key to clarify the company’s production goals and budget. Determine the required degree of automation and equipment configuration based on production volume, product type, and coating quality requirements. For small companies with limited budgets, entry-level low-automation production lines can be selected, while for medium or large companies, appropriately increasing the level of automation can improve production efficiency and coating quality.
Second, carefully evaluate the functional requirements of the production line. Although high-end production lines are more expensive, they can provide higher precision, intelligent control, and lower long-term operating costs. If the company’s production needs are complex and it has high requirements for quality and efficiency, choosing mid- to high-end equipment will bring a better return on investment.