The automated powder coating line is gaining increasing attention in the aluminum profile. Compared with traditional manual spraying, it can provide a more uniform and durable coating, improving production efficiency and reducing resource waste. Aluminum is widely used in industries such as construction and automobiles due to its excellent performance, and automated powder coating lines have become an ideal choice to meet high-quality requirements.
This article will explore the advantages of automated powder coating lines in aluminum profiles, analyze its application in improving coating quality and production efficiency, and discuss how to choose the right automated powder coating line manufacturers.
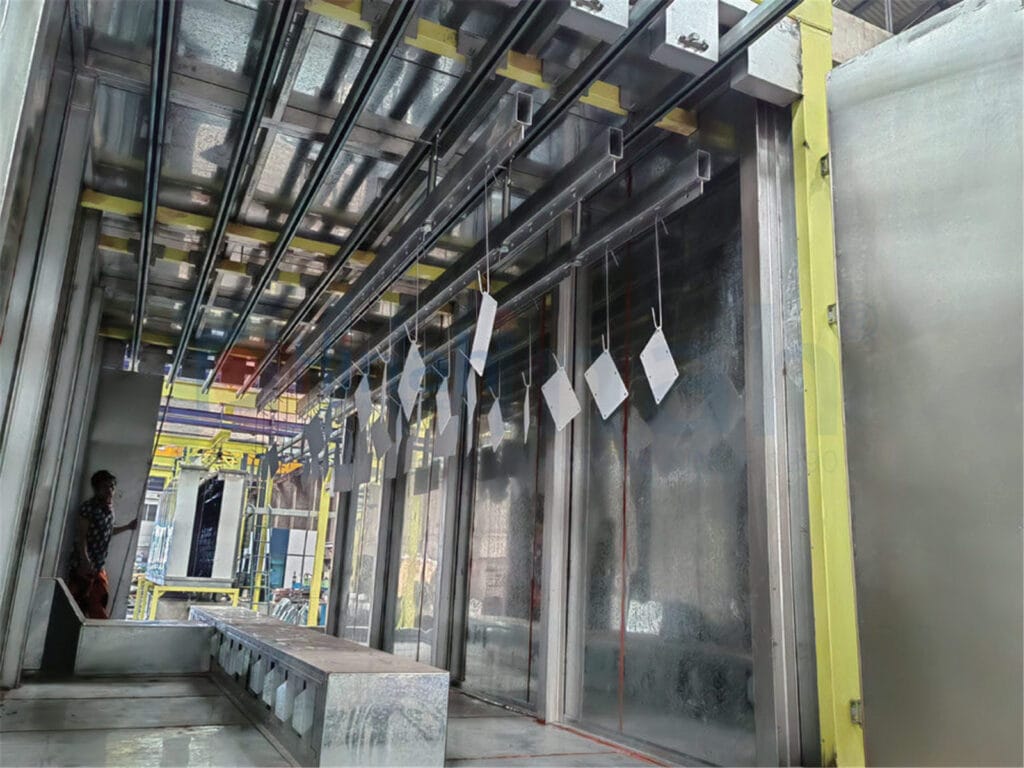
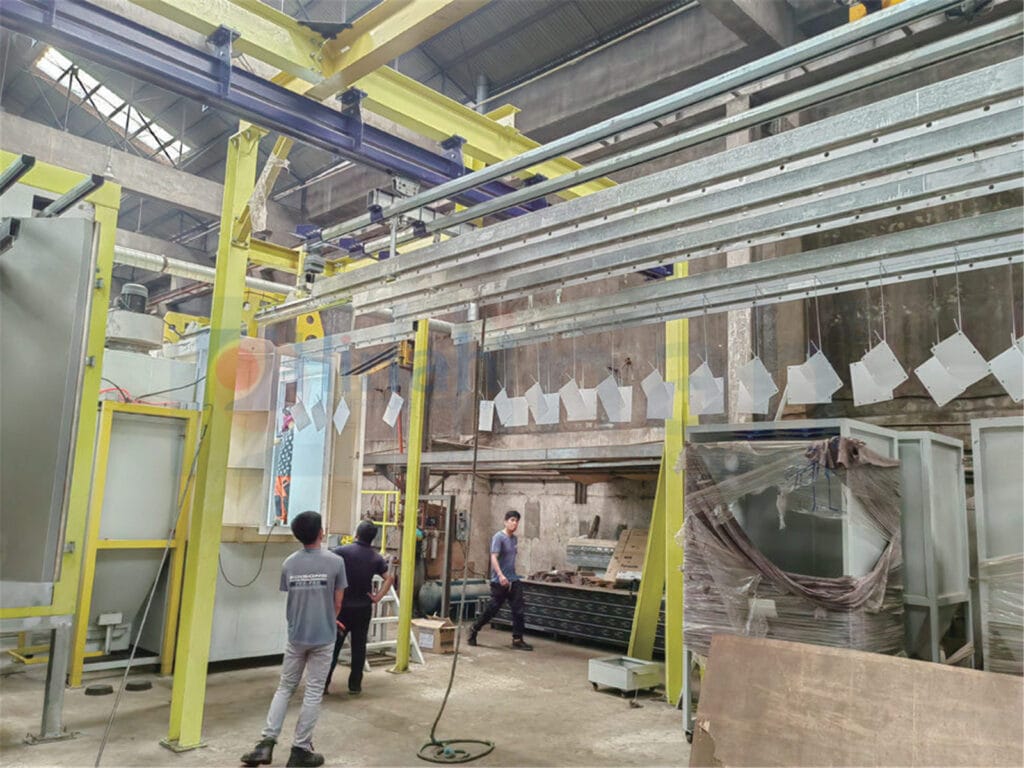
I. Basic principles of automated powder coating line
Automated powder coating line is an efficient coating technology that evenly sprays powder coating on the surface of aluminum through electrostatic spraying and other methods, and forms a hard and uniform coating through the curing process. This process usually includes three stages: pretreatment, spraying, and curing. In the pretreatment stage, the surface of the aluminum is cleaned to ensure the adhesion of the coating; in the spraying stage, equipment such as spray guns or robotic arms are used to evenly cover the coating; in the curing stage, the powder coating is melted and cured into a film by heating. The automation of the entire coating process can greatly improve production efficiency and reduce manual intervention.
The automated powder coating line has many technical features. First, precise spraying control can ensure the consistency and uniformity of the coating and avoid human errors. Secondly, the use of electrostatic spraying technology and recycling systems can effectively reduce paint waste, save energy, and meet environmental protection requirements. At the same time, the efficient powder recovery and exhaust gas treatment system not only reduces resource consumption but also reduces harmful gas emissions, making the production process more green and environmentally friendly.
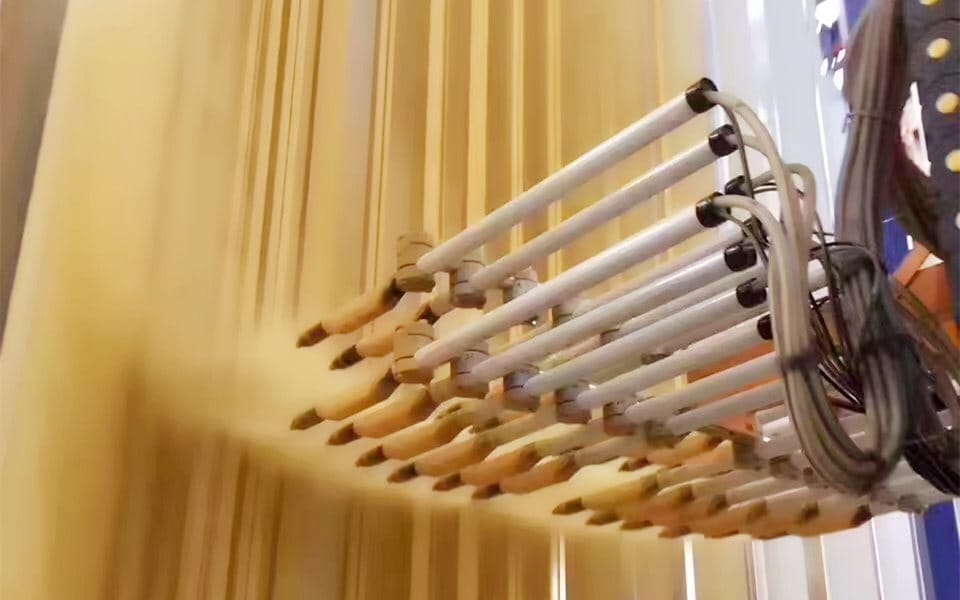
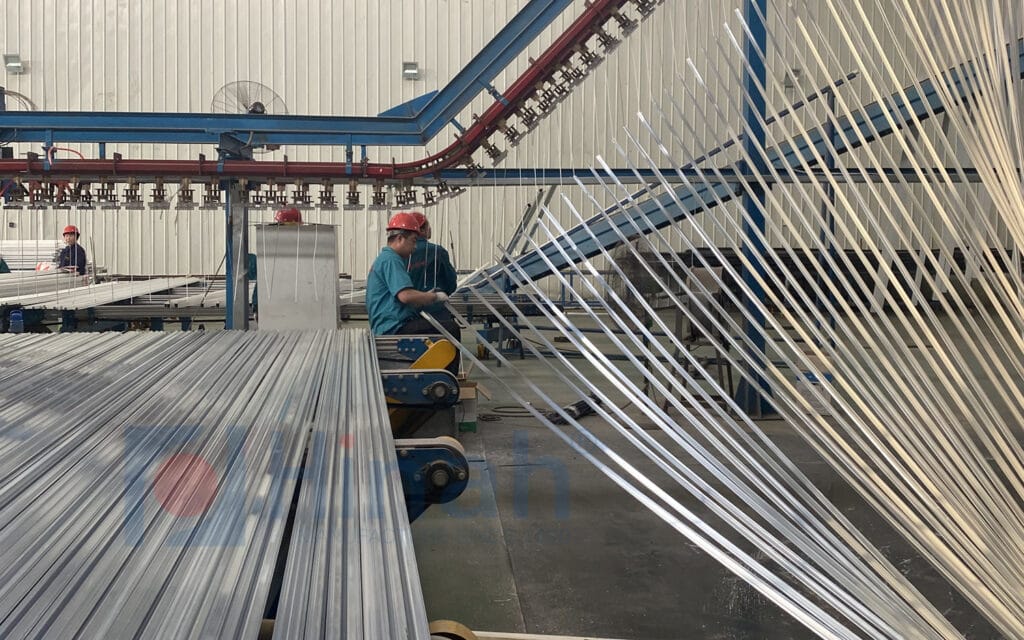
II. Advantages of automated powder coating lines for aluminum profile
2.1 Improve coating quality and consistency
First, automated powder coating lines can significantly improve the quality and consistency of coatings. Through precise spray control, the thickness and uniformity of the coating can be strictly guaranteed, avoiding errors that may occur in manual painting. The automated system ensures that the coating adhesion and corrosion resistance of each piece of aluminum surface reaches the best standards, and the surface effect is more beautiful.
2.2 Improve production efficiency and reduce waste
Secondly, the automated powder coating line greatly improves production efficiency and reduces resource waste. Compared with traditional manual spraying, automated equipment can perform efficient operations quickly and continuously, significantly increasing production speed. At the same time, the precise spraying of paint and efficient recycling system reduce the waste of powder paint, further reduce production costs and improve resource utilization.
2.3 Reduce labor costs and improve safety
Finally, automated powder coating lines also play an important role in reducing labor costs and improving safety. The introduction of automated equipment significantly reduces the need for manual operations, thereby reducing labor costs. In addition, automated systems reduce operator exposure risks and improve overall production process safety.
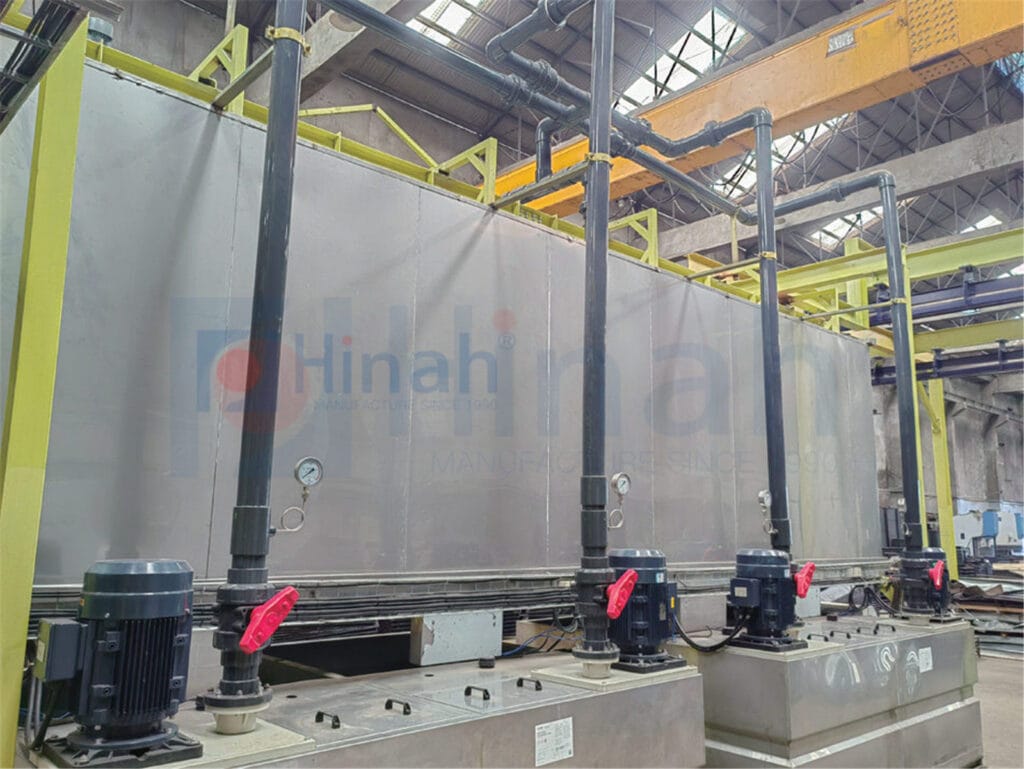
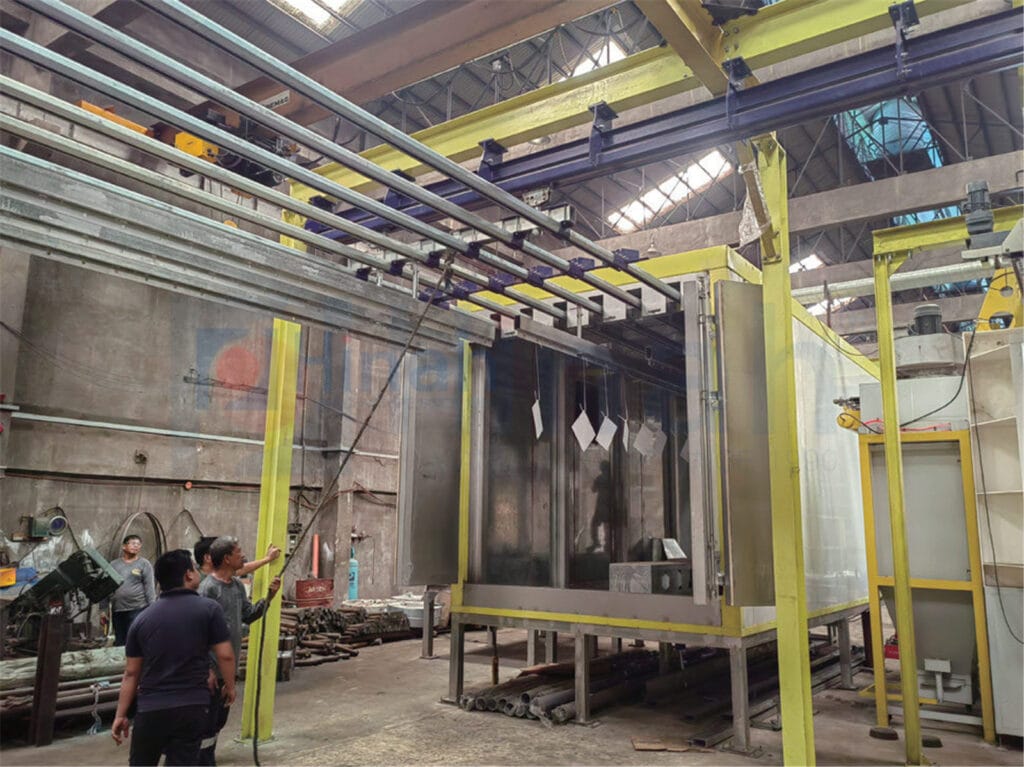
III. Application of automated powder coating lines in aluminum profiles
3.1 Construction industry
In the construction industry, the coating requirements for aluminum alloy window frames, doors and windows, curtain walls, and other products are very strict, requiring the coating to have good weather resistance, corrosion resistance, and decorative effects. Automated powder coating lines can provide uniform and durable coatings, improve the service life and appearance quality of aluminum materials, and ensure the durability and aesthetics of buildings.
3.2 Automotive industry
In the automotive industry, the coating of aluminum bodies and aluminum alloy parts requires higher adhesion and corrosion resistance of the coating. Automated powder coating lines can efficiently complete the coating of a large number of body parts and provide a highly consistent coating effect, helping to improve the quality and market competitiveness of automotive products.
3.3 Appliance industry
In the home appliance industry, the coating of aluminum shells, frames, and other parts also requires high-quality surface treatment, especially since the appearance requirements are very high. Automated powder coating lines can ensure the uniformity and aesthetics of the coating through precise control while improving production efficiency and reducing labor costs.
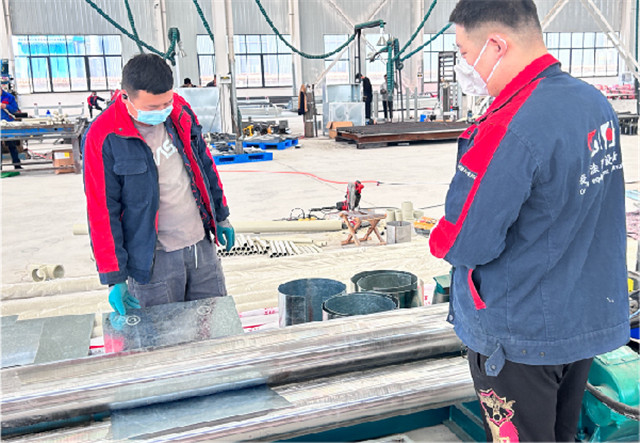
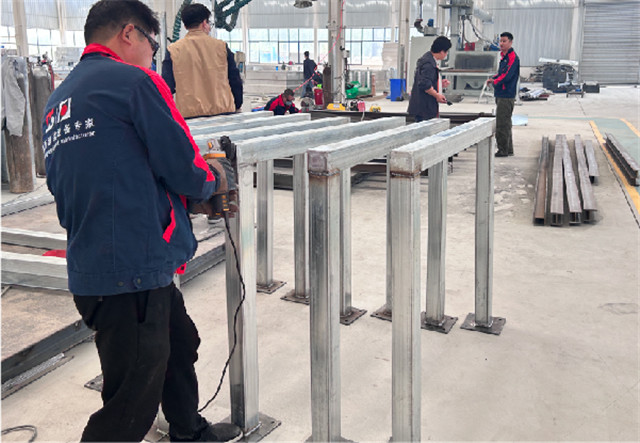
IV. Choosing the right automated powder coating line for sale
4.1 Key factors
When choosing an automated powder coating line for sale, the specifications of the equipment need to be determined based on the size, shape, and surface treatment requirements of the aluminum. At the same time, it is also very important to consider the production scale and capacity requirements. Small production lines are suitable for small batches, while large-scale production requires more efficient equipment. In addition, the budget energy efficiency and maintenance costs of the equipment should also be taken into consideration to ensure the economy of long-term operation.
4.2 Ensure the efficiency and long-term stable operation of the equipment
In order to ensure the efficient operation of the equipment, companies should choose advanced technology and high-quality equipment that can provide higher production efficiency and coating quality. In addition, perfect after-sales service and technical support are essential. Choosing a supplier who can provide timely maintenance and technical support can effectively reduce the impact of equipment failure on production and ensure the stable operation of the production line.
V. How to choose a reliable automated powder coating line manufacturer?
It is very important to choose a powder coating line manufacturer with a good reputation and rich experience. Well-known manufacturers are usually able to provide high-quality equipment and stable technical support. Their products are market-proven, can meet industry standards, and perform well in actual use. Choosing a manufacturer that has been verified by customers and has successful cases can ensure the stability and efficiency of the equipment in long-term operation.
Technical support is one of the key factors when choosing a powder coating line manufacturer. A trustworthy manufacturer should provide a full range of after-sales services, including equipment installation and commissioning, operation training, regular maintenance, troubleshooting, etc. At the same time, the manufacturer’s response speed and maintenance capabilities are also very important to ensure that the equipment can quickly resume production when problems occur and avoid long-term downtime losses.
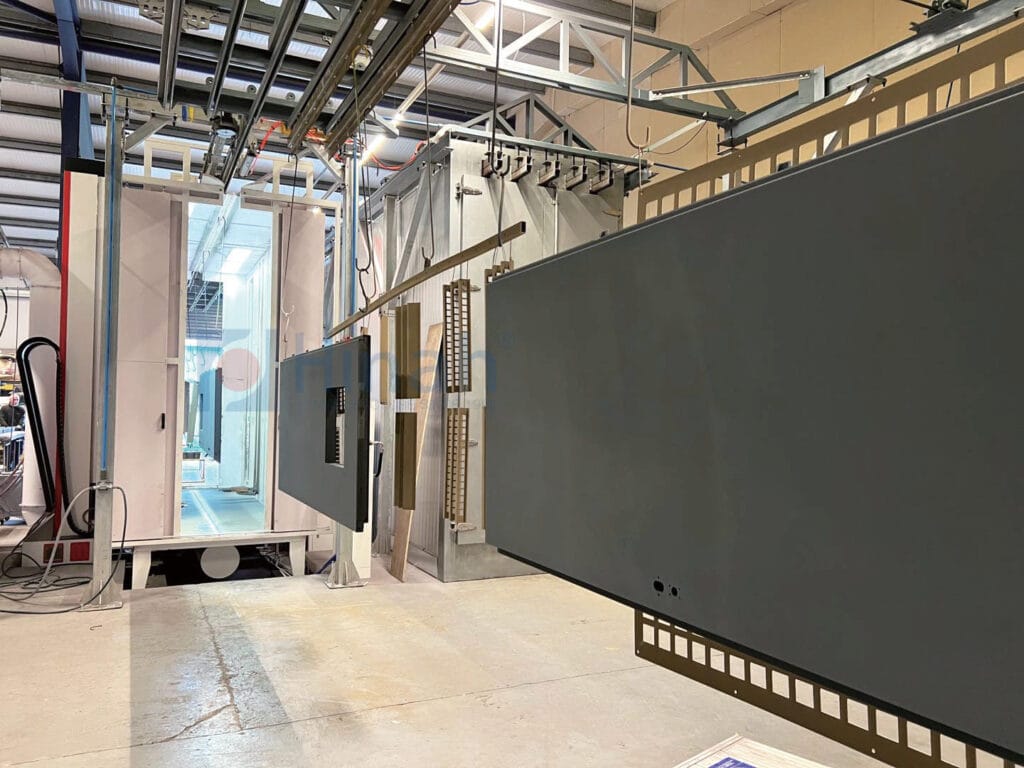
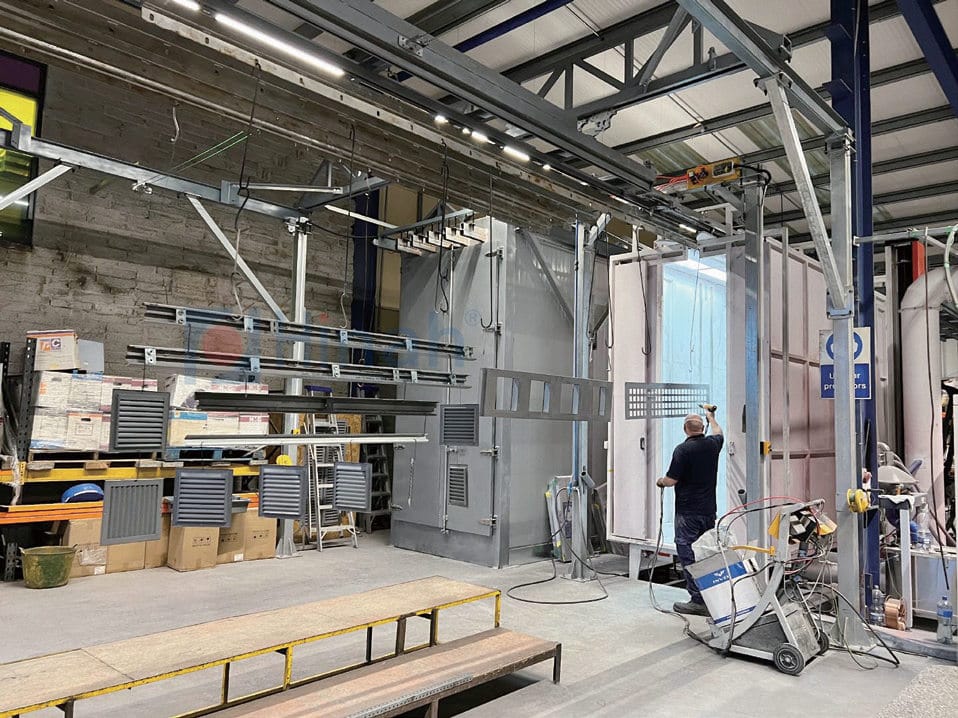
VI. Conclusion
The application of automated powder coating lines in aluminum profile is increasingly becoming the first choice in many industries due to its high efficiency and accuracy. By adopting automated equipment, companies can not only improve coating quality and consistency but also significantly improve production efficiency and reduce paint waste and energy consumption. In addition, the automated powder coating line can also reduce labor costs and improve operational safety, especially in the coating of special materials such as aluminum, which shows unparalleled advantages.
When choosing a suitable automated powder coating line, companies need to comprehensively consider the characteristics of the aluminum material, production needs, budget, and subsequent maintenance of the equipment. Working with a reliable manufacturer ensures efficient operation and long-term stability of your equipment. Therefore, when companies purchase automated powder coating lines, they should pay attention to the technical performance, quality assurance, and after-sales service of the equipment to ensure that they choose high-quality equipment that suits their production needs, thereby achieving more efficient and economical production.