Powder coating has become a widely used surface treatment technology in modern industry due to its environmental protection and high efficiency. However, precision control in the coating process is still a challenge, and any slight error may affect the quality and appearance of the coating. The emergence of automatic powder coating line provides a new solution to this problem. With its intelligent control system, the automatic powder coating production line can accurately adjust the spraying parameters to ensure the consistency and quality of each layer of coating. By reducing the errors caused by manual operation, it not only improves production efficiency, but also ensures the high precision and stability of the powder coating process.
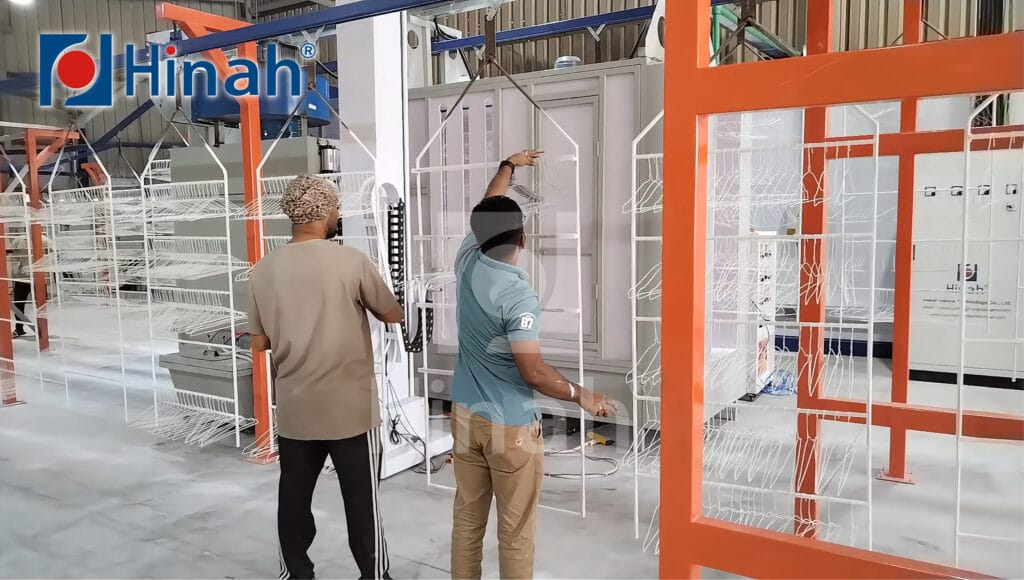
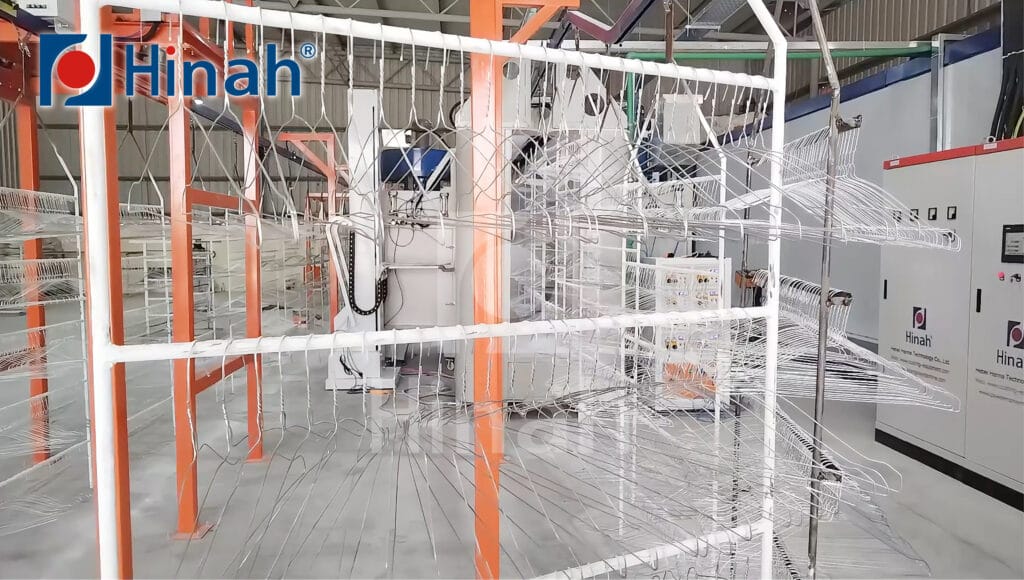
I. Core technology of automatic powder coating line
The automatic powder coating line realizes precise control of the coating process through highly automated and intelligent technology. Its core technologies mainly include the following aspects:
1. Spraying technology and charge control
- Charge spraying: The automatic powder coating line uses the principle of electrostatics to make the powder coating carry a negative charge, while the coated object carries a positive charge. In this way, the powder coating is adsorbed to the surface of the workpiece during the spraying process to achieve uniform coating coverage.
- Spraying distance and angle control: The spray gun can accurately control the spraying distance and angle to ensure that the powder coating is evenly covered in every corner of the product to avoid uneven coating thickness.
2. Airflow and coating uniformity
- Airflow control system: Accurately adjust the airflow of the spray gun to ensure uniform distribution of the coating during spraying. The optimized airflow system can reduce powder waste and improve the uniformity of the coating.
- Coating uniformity detection: Through advanced detection technology, the thickness and uniformity of the coating are monitored in real time to ensure that every product produced meets quality standards.
3. Intelligent control system
- Automatic adjustment function: The automatic powder coating line is equipped with a highly intelligent control system, which can automatically adjust the spraying parameters, such as powder spraying amount, spraying time, temperature, etc. according to different production needs to optimize the coating effect.
- Real-time data feedback and adjustment: The control system can monitor the production status in real time, feedback data to the operator or automatically adjust it to ensure that each batch of production is carried out in the best condition.
4. Powder recovery and reuse
The large cyclone recovery system used in the automatic powder coating line can efficiently separate powder and air, recover the paint and ensure that the powder is not contaminated. Through the high-speed rotating wind flow, the unadsorbed powder will be separated and transported to the recovery box through the pipeline to minimize waste.
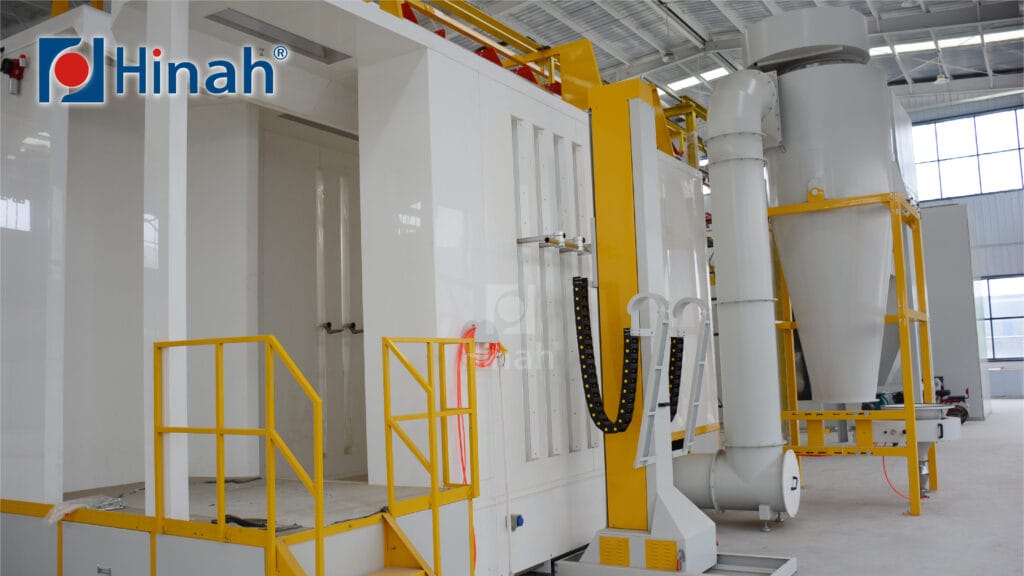
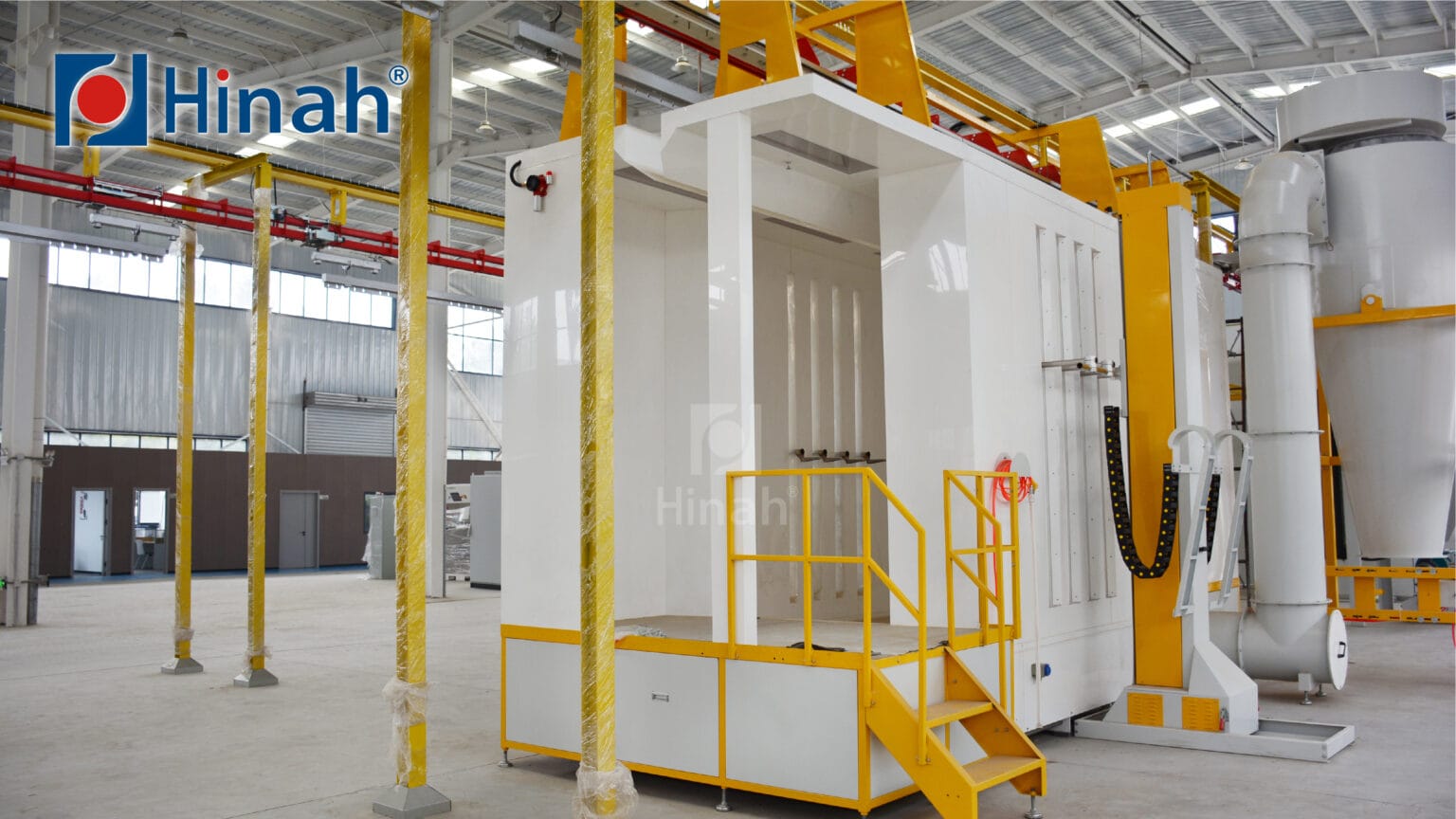
II. Advantages of automatic powder coating line
1. Intelligent and precise coating control
Through the integration of high-precision sensors and intelligent algorithms in the automation system, the spraying pressure, powder flow rate and atomization effect can be monitored in real time to achieve ±5μm film thickness error control. Electrostatic adsorption technology combined with a closed-loop feedback mechanism ensures that the coating evenly covers complex curved surfaces, eliminates common sagging, orange peel or spray leakage in manual operation, and significantly improves the consistency of product appearance and anti-corrosion performance.
2. Full-process efficient production system
The six-axis robotic arm linkage reciprocating machine system is used, and the intelligent conveyor chain is used to achieve 24-hour continuous operation, and the single-line production capacity is increased by 200%-300%. Human intervention is reduced to only one person monitoring the central control system, effectively avoiding quality fluctuations caused by human fatigue. The modular design supports fast color change (color switching within 15 minutes), and the powder recovery system makes the material utilization rate reach more than 98%, and the comprehensive operating cost is reduced by 40%.
3. Flexible production solution
Equipped with a three-dimensional scanning automatic recognition system, it is compatible with workpieces of different sizes from 5mm to 5m, and supports multi-angle synchronous spraying of special-shaped parts. The database stores more than 200 process parameter combinations, and different spray modes (such as gradient coatings on car wheels or three-dimensional textures on home appliance panels) can be called up with one click through the HMI interface. The expansion interface reserves the industrial Internet of Things protocol, which can be easily connected to the MES system to realize intelligent production scheduling and meet the needs of multi-variety and small-batch customization.
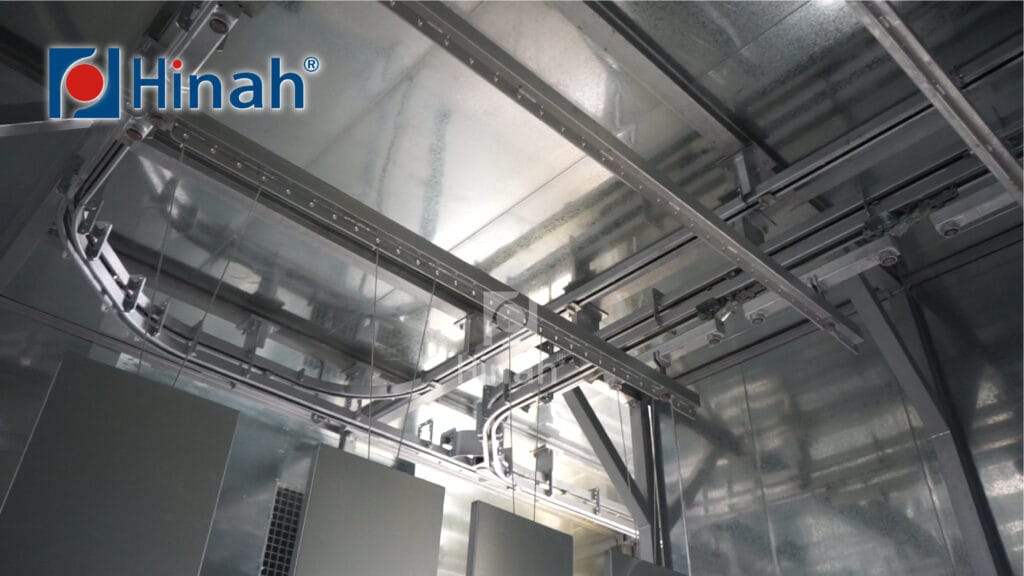
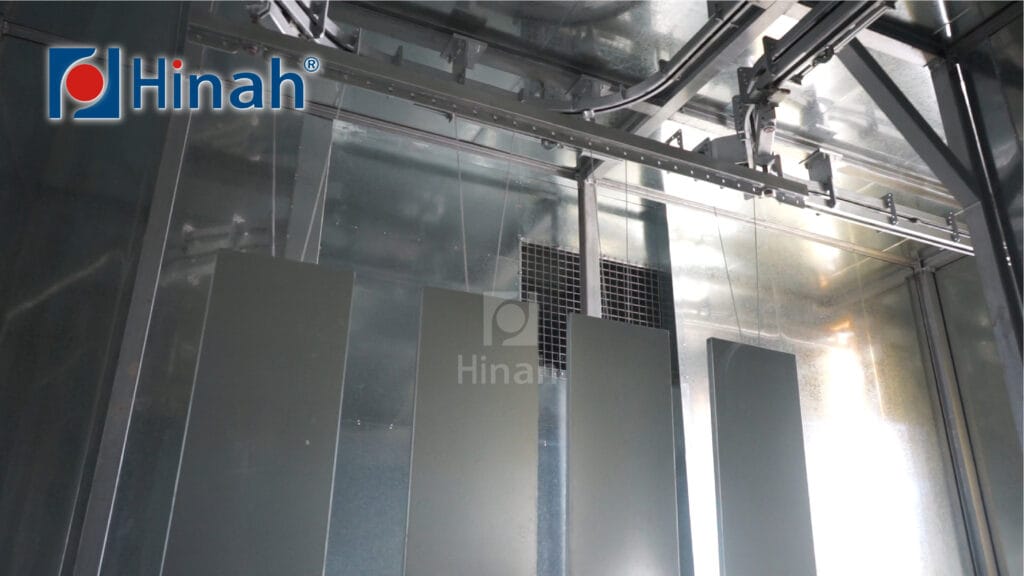
III. Key factors behind precise coating
1. Powder spraying quality and particle size control
The quality of powder spraying has a direct impact on the coating effect. The particle size, shape and distribution of the powder determine the uniformity and adhesion of the coating. Too large or too small a particle size may lead to uneven coating thickness and affect the coating effect. The automatic powder coating line ensures that each layer of coating achieves the best coverage effect by precisely controlling the powder particle size and particle size distribution. Through the powder spraying quality monitoring system, the amount of powder used can be adjusted in real time to ensure high-quality coating.
2. Automatic spray gun adjustment and directional spraying technology
Automatic spray guns are the key to ensuring uniform distribution of coatings. Modern spray guns use intelligent adjustment systems that can automatically adjust spraying parameters such as spraying angle, pressure and spray volume according to product shape, size and surface characteristics. This directional spraying technology can reduce overspray and leak spraying, and achieve precise coating of complex-shaped workpieces. At the same time, the automatic spray gun can also adjust the spraying intensity based on real-time feedback to ensure that each workpiece surface is evenly covered.
3. Accurate temperature control and baking process
Temperature is an important factor affecting the adhesion, leveling and hardness of powder coating. The automatic powder coating line monitors and adjusts the baking temperature after spraying in real time through an integrated intelligent temperature control system to ensure that the powder is fully cured at the appropriate temperature. The precise baking process can avoid overheating or underheating of the coating and ensure the firmness and durability of the coating. In addition, the intelligent temperature control system can automatically adjust the temperature and baking time according to the characteristics of different powders, thereby maximizing the quality and stability of the coating.
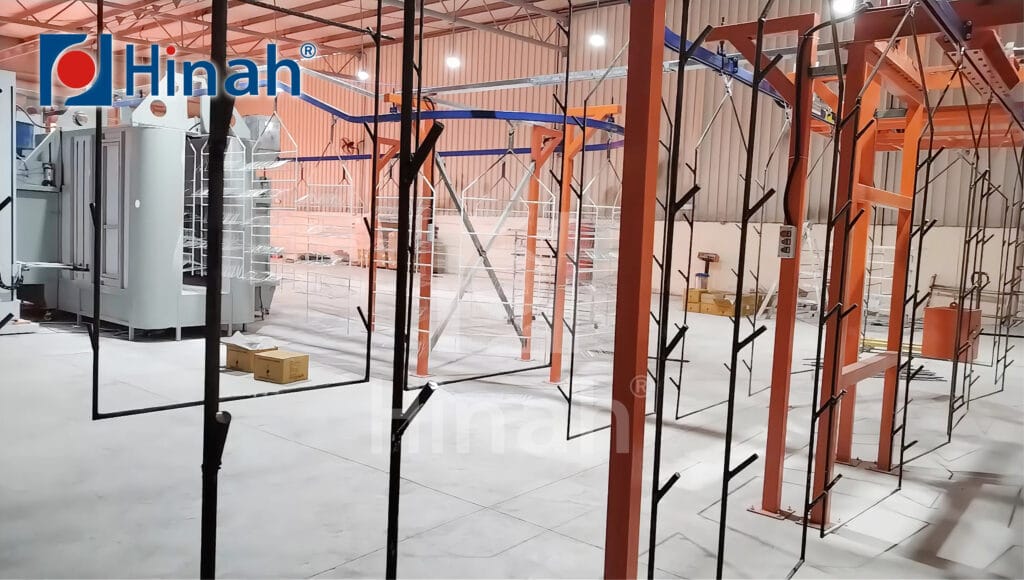
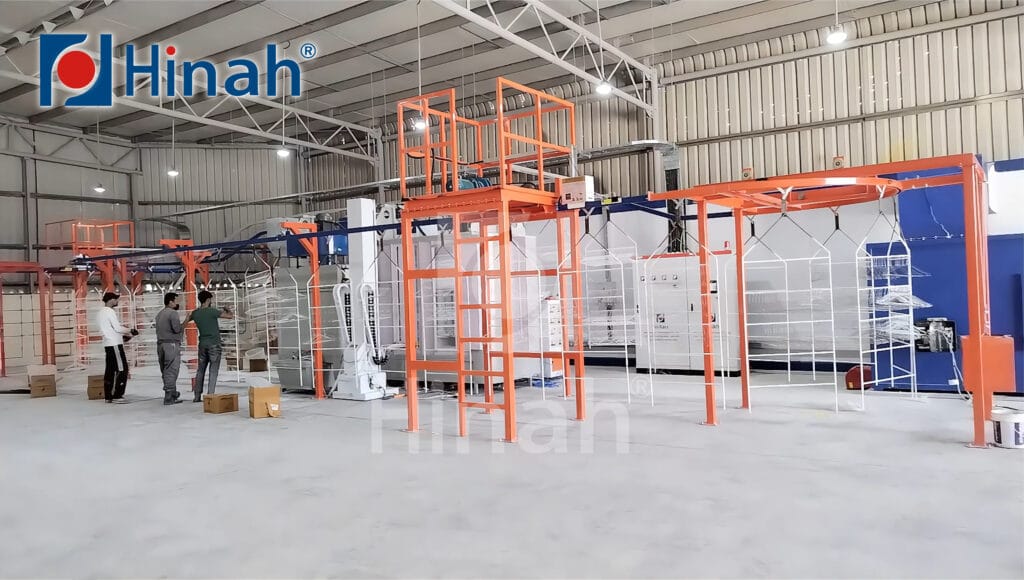
IV.Conclusion
With the advancement of technology, the automatic powder coating line not only improves the accuracy of coating, but also helps enterprises improve production efficiency and product quality. Through intelligent control and precise paint spraying, enterprises can reduce waste, reduce manual errors, and adapt to more diverse product needs. These advantages not only make the production process more efficient, but also allow each product to meet higher standards.
The automatic powder coating line is not only changing the coating process, but also injecting new vitality into the entire industry. In the future, precision and efficiency will become synonymous with every coating production line, and this transformation is also the new revolution we are welcoming together.