As the manufacturing industry continues to increase its requirements for efficiency and quality, automated powder coating system has become a core technology for improving productivity. It not only reduces manual errors and improves coating consistency, but also reduces costs and energy consumption. With automated systems, companies can cope with increasingly stringent environmental regulations and market demands and ensure the sustainable development of production lines. This article will introduce you to the five key steps to implement automated powder coating to help factories meet future challenges.
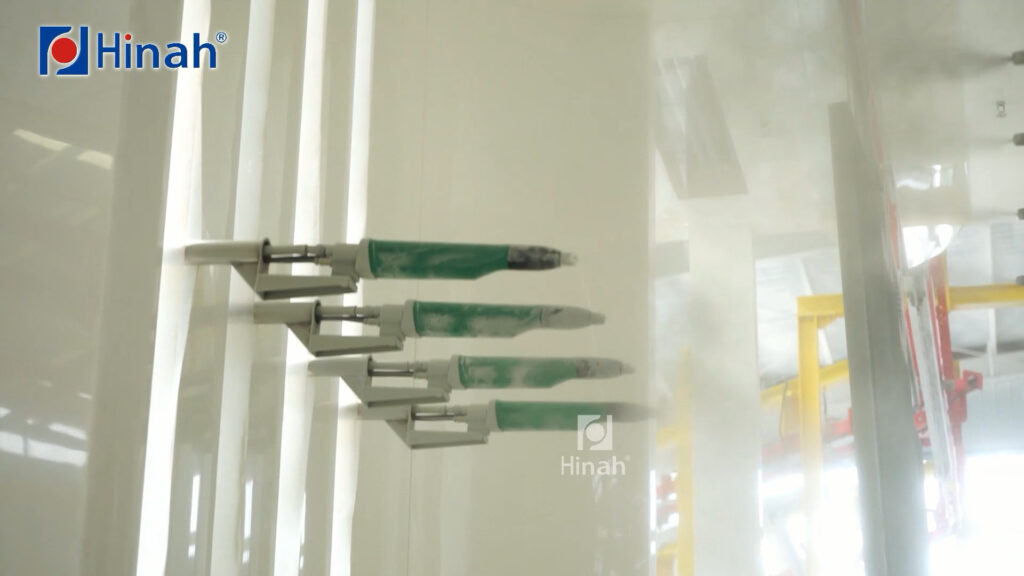
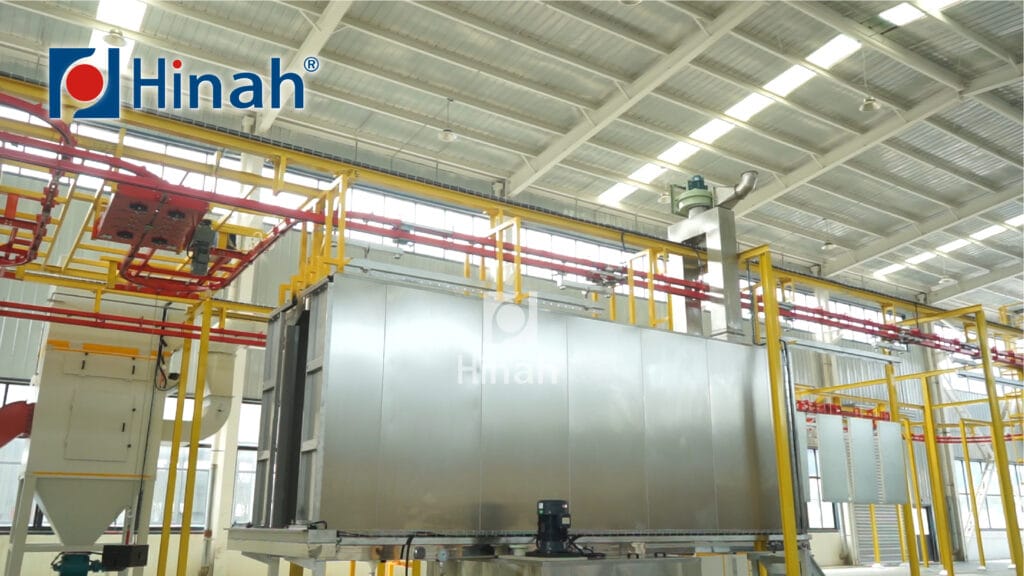
Step 1: Evaluate the factory’s powder coating needs and goals
Before implementing an automated powder coating system, you first need to conduct a comprehensive assessment of the factory’s production needs and goals. The core of this step is to understand the challenges your factory faces in the production process and the problems you hope to solve through automation technology.
1. Analyze the existing production process
By evaluating the current production line, identify bottlenecks and inefficient areas. For example, are there problems such as unstable coating quality, cumbersome manual operations, or low coating recovery efficiency?
2. Determine automation goals
Set clear automation goals based on production needs. Possible goals include:
- Improve production efficiency
- Reduce labor costs
- Improve product consistency and quality
- Reduce energy consumption and waste
Through this step, you will be able to clearly understand what specific improvements the automated powder coating system can bring to your factory, and lay the foundation for selecting the right equipment and design solutions in the next step.
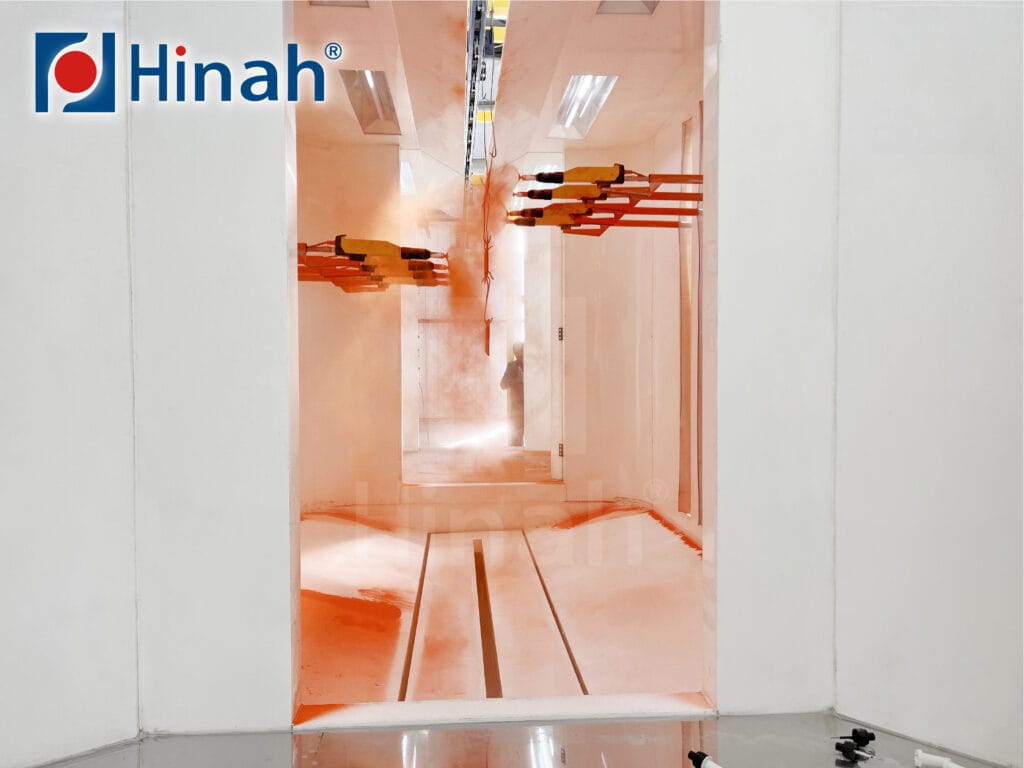
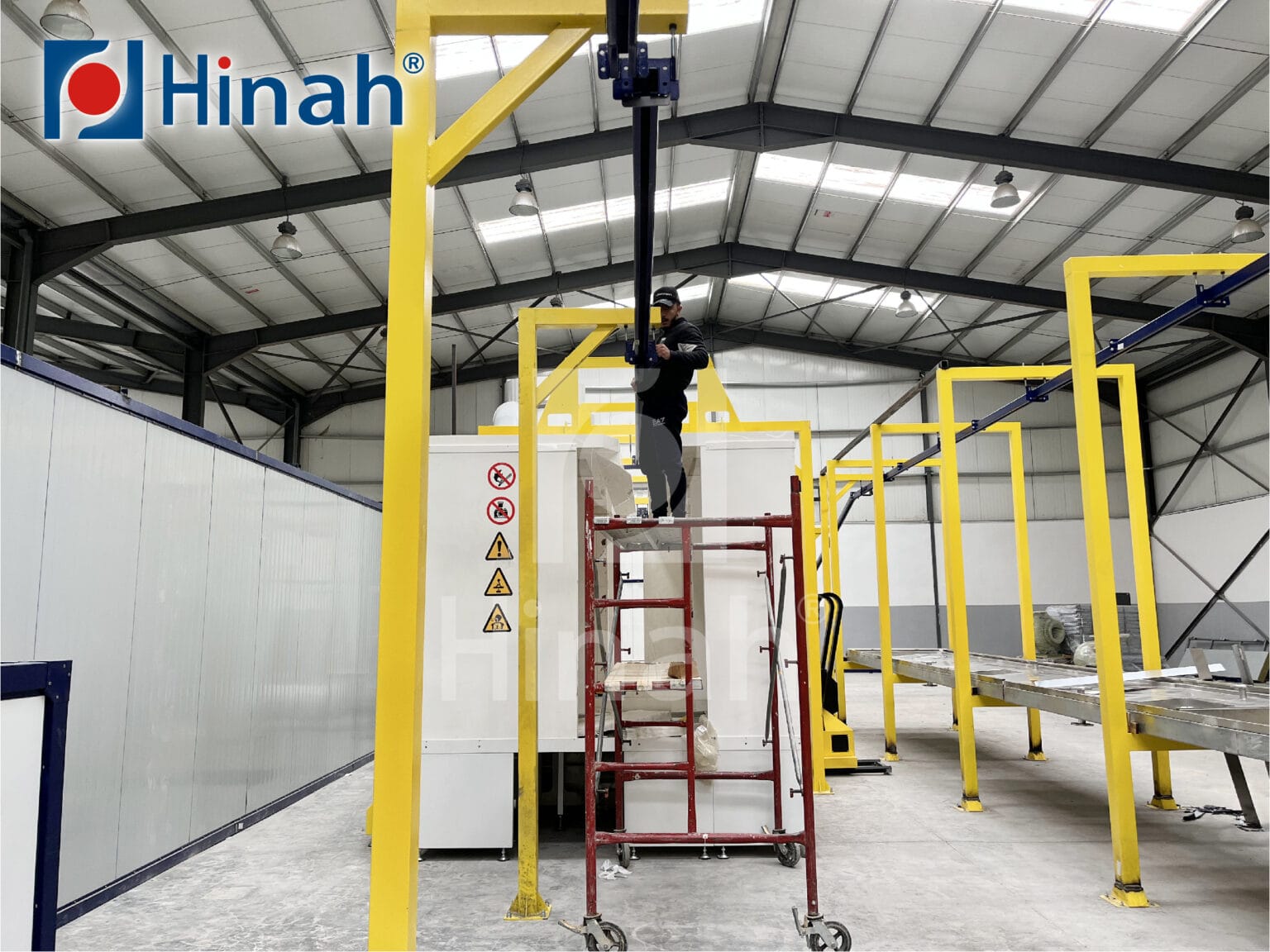
Step 2: Choose the right automated powder coating equipment
After evaluating the needs of the factory, the next step is to choose the right automated powder coating equipment. Different production needs and goals may require different types of equipment. Here are some key equipment introductions to help you make the right choice:
Powder Coating Robot
The powder coating robot is the core equipment in the automated powder coating system. It achieves uniform and efficient powder coating application through a precise control system. It is suitable for mass production and can provide higher coating quality and consistency. The robot usually has intelligent path planning, which can cover complex-shaped workpieces to ensure uniform coating.
Fast Color Change Powder Coating Booth With Large Cyclone Recovery System
The fast color change powder coating booth is the key to improving production efficiency. It allows switching between different colors of powder in a very short time, reducing waste during cleaning and switching. Equipped with a large cyclone recovery system, it can efficiently recover powder, with a powder recovery efficiency of up to 98%, reducing waste and reducing production costs.
Automatic Powder Coating Conveyor System
Automatic powder coating conveyor system is used to automatically transport the workpiece to be sprayed. The system ensures that each step of the workpiece from spraying to curing can be carried out efficiently and continuously. By integrating an automatic conveyor system, you can reduce manual intervention and improve the overall operating efficiency of the production line.
When selecting these equipment, make sure they are compatible with the existing production line and can meet the needs of future growth. The right equipment combination will directly affect your production efficiency, quality control and operating costs.
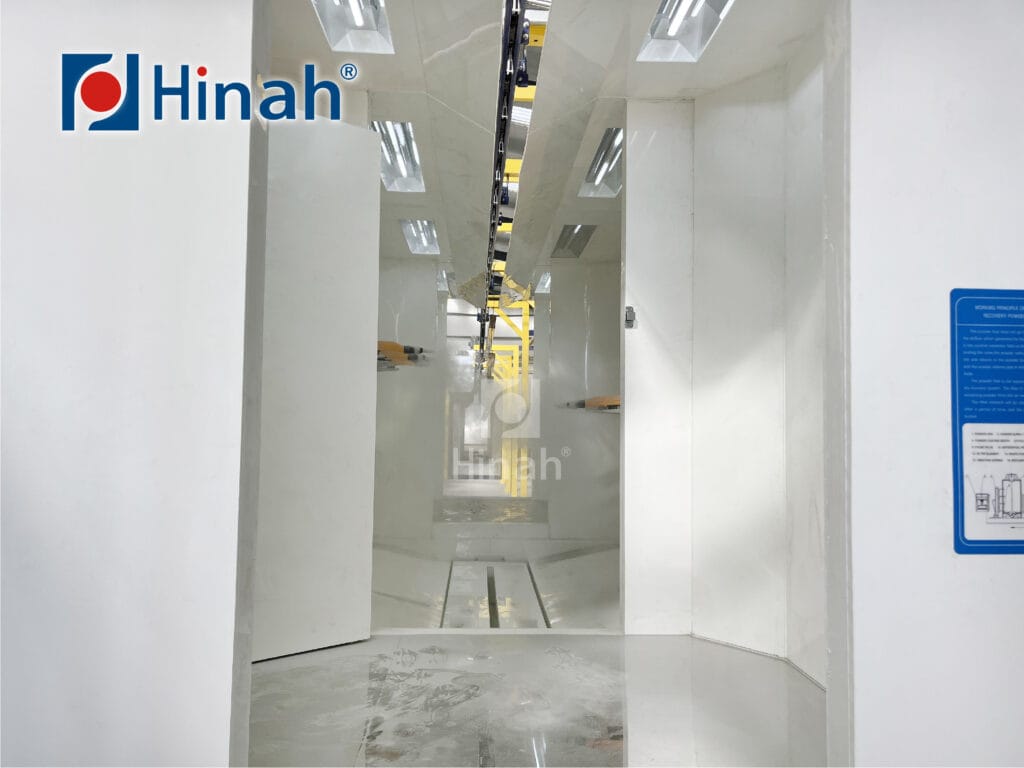
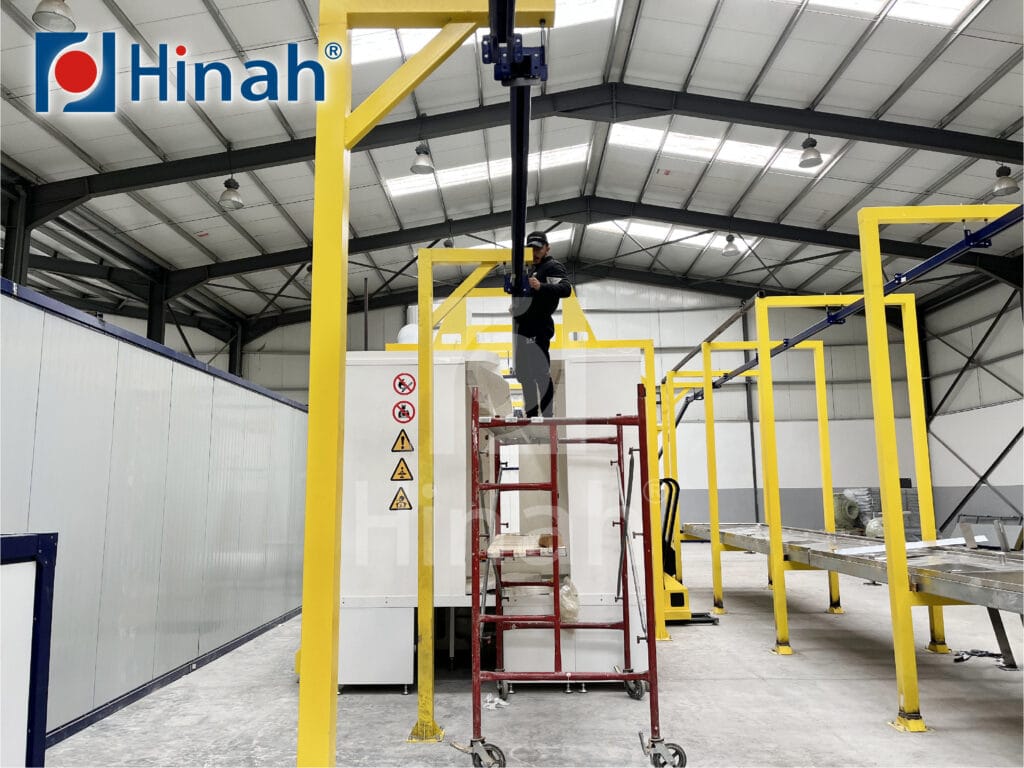
Step 3: Planning and designing an automated powder coating system
After selecting the right equipment, the next key step is to plan and design an automated powder coating system. This is not just about placing the equipment in the factory, but also about considering the optimization of the overall production process and the effective integration of the equipment. The following are several aspects that need to be focused on during the design process:
Design a reasonable production process and layout
The core of the production process design is to achieve efficient flow of workpieces at various processing stages. First, consider the preparatory work before coating (such as cleaning, drying, etc.), then the spraying process, the curing process, and finally the finished product inspection and packaging. Each link should be efficiently connected to avoid bottlenecks and unnecessary waiting.
In terms of layout, the automated powder coating system should ensure streamlined, reduce the distance and time of material handling, avoid frequent transfer of workpieces between production lines, and improve production efficiency. In addition, the installation location of the equipment should be reasonably planned to ensure a reasonable distance between the equipment for easy operation and maintenance.
Consideration of compatibility of integrated equipment with existing production lines
When introducing an automated powder coating system, it is necessary to ensure the compatibility of the new equipment with the existing production line. For example, the automatic powder coating delivery system needs to match the existing workpiece delivery method to avoid production interruptions or inefficiencies caused by equipment incompatibility.
In addition, infrastructure such as power supply, gas and water sources also need to be compatible with the new system. For robotic spraying equipment, special consideration should be given to integration with existing production lines, including interconnection of control systems, data exchange and coordination of automated control.
Step 4: Implement the installation and commissioning of the automated powder coating system
After completing the design and equipment selection, the next step is to smoothly install and commission the automated powder coating system. This stage is crucial because correct installation and commissioning can not only ensure the smooth operation of the equipment, but also help avoid later production problems.
Key steps in system installation
- Equipment location confirmation and installation
According to the previously planned layout, each device must first be installed at the designated location. Ensure that the powder coating robot, powder coating room, conveyor system and other equipment are installed in accordance with the design requirements, and maintain sufficient operating space and maintenance channels. After the equipment is fixed, check the stability of its installation to avoid unnecessary vibration or displacement during operation.
- Electrical and pneumatic system connection
Automation systems usually require the support of power and air sources. Ensure the correct connection of electrical lines and pneumatic pipelines, and that all connection points meet safety specifications. Especially for spraying robots and automatic conveying systems, ensure the correct access of signal transmission and control systems so that the system can operate stably.
- Connection between powder system and recycling system
Ensure smooth connection between powder coating system and recycling system to avoid blockage or waste of powder during transportation or recycling. Check the performance of recycling system to ensure that it can efficiently recycle unused powder.
Precautions during debugging
- Preliminary system operation test
After installation, conduct preliminary operation test. Check the start, stop and working status of each device to ensure that each function works as expected. In particular, the powder coating robot needs to debug its spraying path and spraying parameters to ensure uniform and precise coating.
- Debug spraying room and color change function
During the debugging process of fast color change powder coating room, ensure that the color change system switches smoothly without powder leakage or pollution. Adjust parameters such as powder spraying amount and wind speed to ensure the best coating effect. At the same time, check the working efficiency of large cyclone recovery system to ensure that the recovery rate reaches the expected level.
- Test automatic conveying system
The automatic powder coating conveyor system needs to be fully tested to ensure the smooth transmission of workpieces on the production line. Check the transmission speed and stability of the system, and verify the stability and adaptability of the system by simulating the operation of different workpiece loads.
- Data monitoring and feedback adjustment
During the debugging process, collect data through the monitoring function of the system to check the operating efficiency of each link. In particular, for key indicators such as spraying quality, powder utilization rate and recycling efficiency, ensure that they meet the predetermined standards. If necessary, adjust the spraying parameters or optimize the workflow.
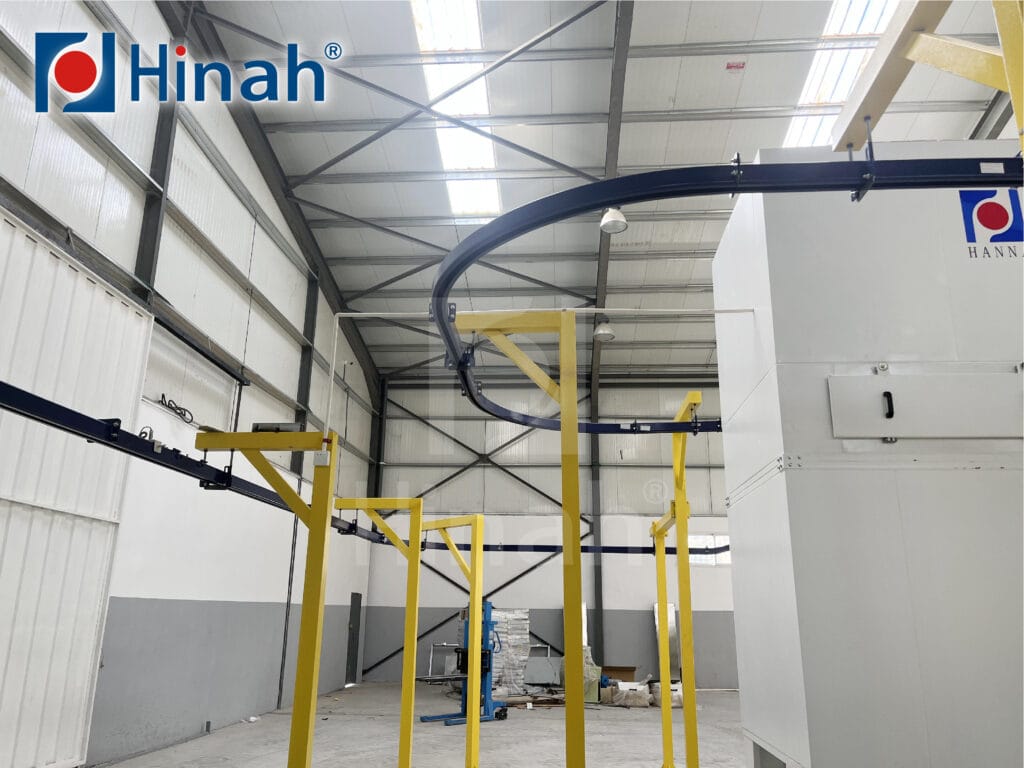
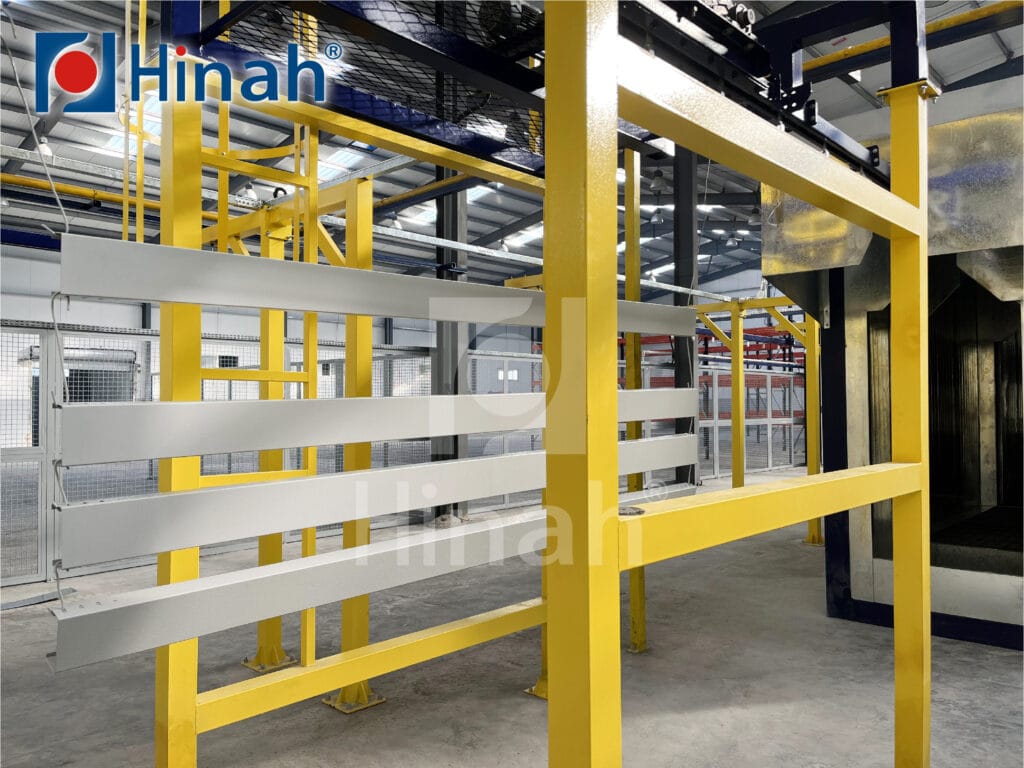
Step 5: Operation and maintenance training of automated powder coating system
Operation training
- Basic operation process: Train employees on how to start, stop and monitor the automated system, and understand how to use the spraying robot and automatic conveying system.
- Spraying parameter adjustment: Teach employees to adjust parameters such as spraying speed and powder flow according to the type of workpiece to ensure stable coating quality.
- Color change operation: Train how to change spray colors quickly and accurately to reduce waste and maintain consistency.
Maintenance training
- Regular inspection and cleaning: Teach employees how to clean the equipment, keep the powder coating room and recovery system clean, and ensure efficient operation.
- Fault diagnosis and handling: Train employees on how to identify common faults and perform simple troubleshooting to reduce downtime.
- Powder system maintenance: Ensure that employees understand how to clean the powder delivery pipeline and recovery system to improve powder utilization.