In modern manufacturing, industrial powder coating has emerged as a game-changer, offering durability, efficiency, and environmental benefits over traditional liquid coatings. As industries demand higher productivity and consistent quality, the adoption of automatic powder coating lines has surged. These systems streamline the finishing process, reducing waste and ensuring uniform coatings on a large scale. This quiet revolution in surface finishing is reshaping production standards, making powder coating the preferred choice across various industries.
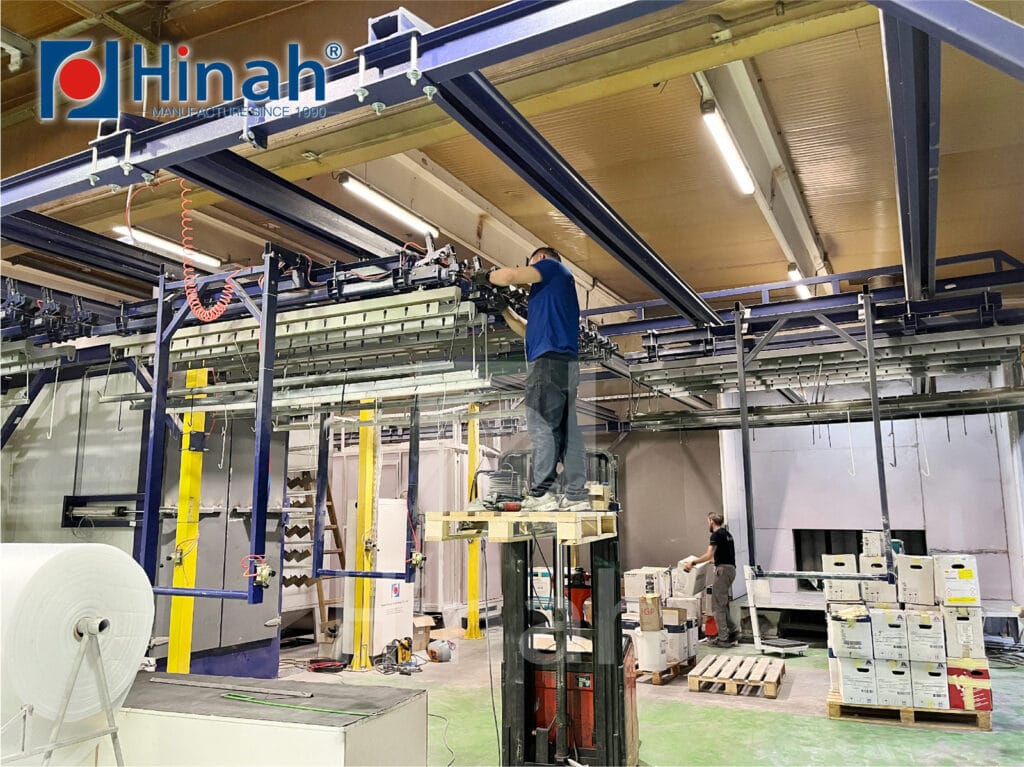
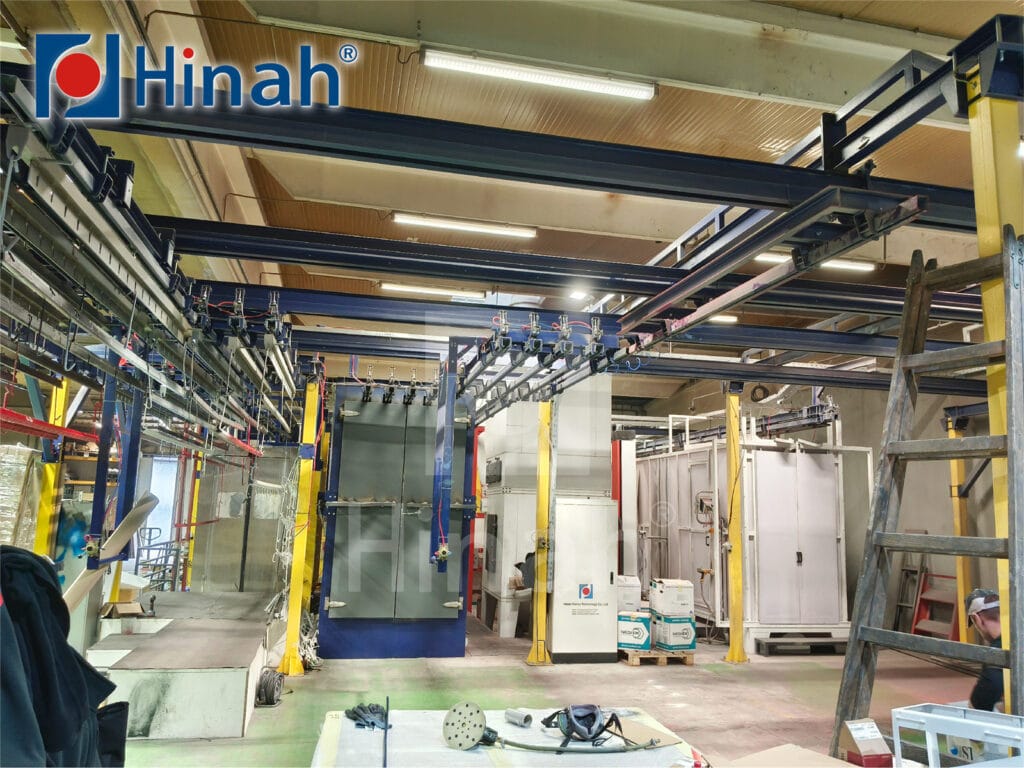
Secret #1: The Cost-Effective Industrial Powder Coating Formula
In modern manufacturing, cost efficiency is a decisive factor in selecting a finishing method. Industrial powder coating stands out as a superior choice, offering significant savings across materials, energy, labor, and long-term maintenance.
- Less Waste, More Savings
Unlike liquid coatings, which result in significant overspray loss, industrial powder coating boasts a high transfer efficiency. With the automatic powder coating line, excess powder can be collected and reused, minimizing material waste and maximizing cost-effectiveness.
- Smarter Curing, Reduced Costs
Advancements in curing technology have optimized energy use in powder coating processes. Modern powder coating ovens, such as infrared and convection curing systems, operate more efficiently than traditional drying methods, cutting energy expenses without compromising quality.
- Automation Reduces Overhead
The integration of automatic powder coating line eliminates much of the manual labor required in traditional painting methods. Automated spraying, recovery, and curing systems reduce human intervention, lower labor costs, and minimize maintenance efforts.
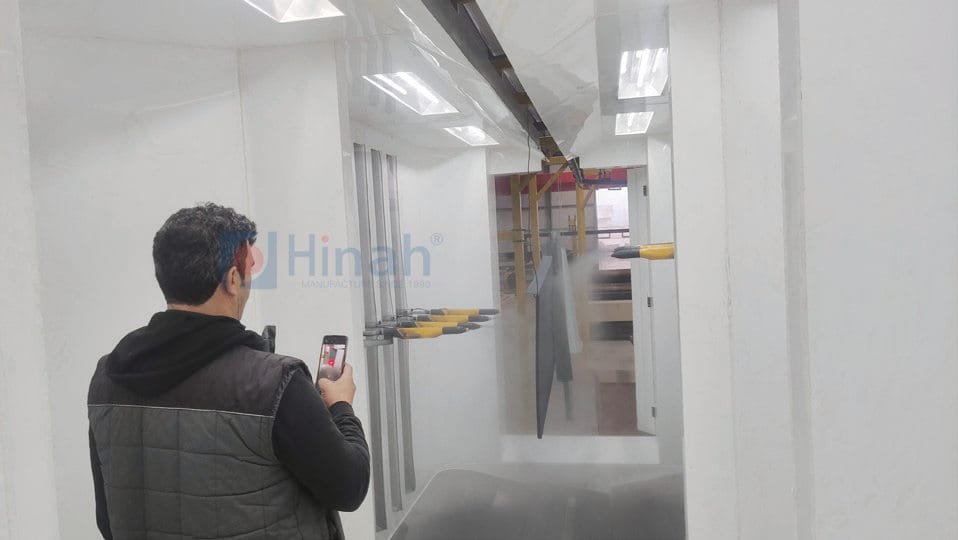
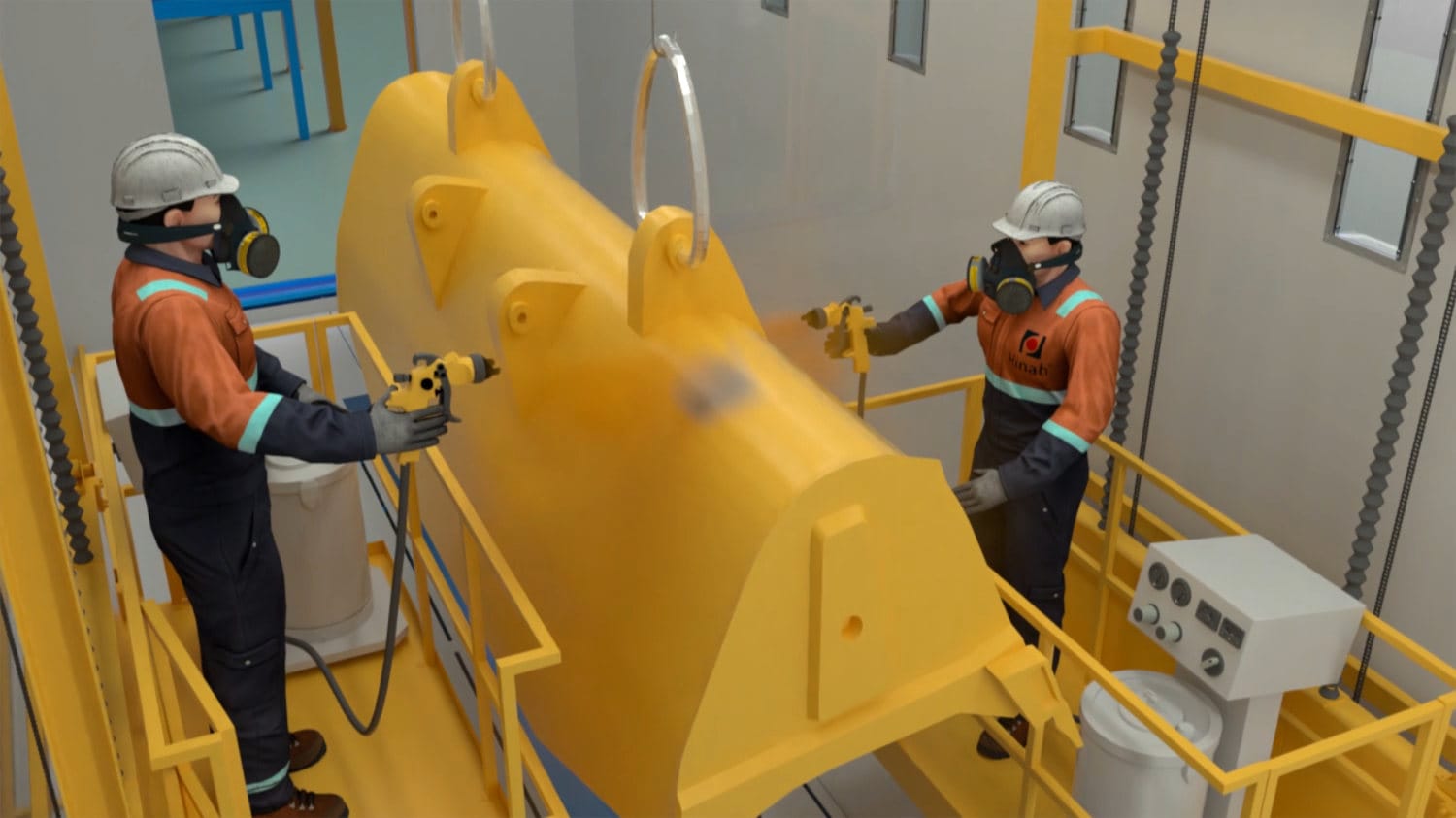
Secret #2: Industrial Powder Coating for Eco Compliance
As environmental regulations tighten, industrial powder coating has become the go-to solution for manufacturers seeking sustainable finishing methods. Unlike traditional liquid coatings, it is VOC-free, eliminating harmful solvent emissions and improving workplace safety. Additionally, its high material efficiency allows overspray to be collected and reused, significantly reducing waste. Many industries rely on powder coating to meet strict global standards such as REACH and EPA regulations, ensuring compliance without compromising performance. By adopting this eco-friendly process, manufacturers not only lower their carbon footprint but also enhance overall production efficiency, making sustainability a core advantage.
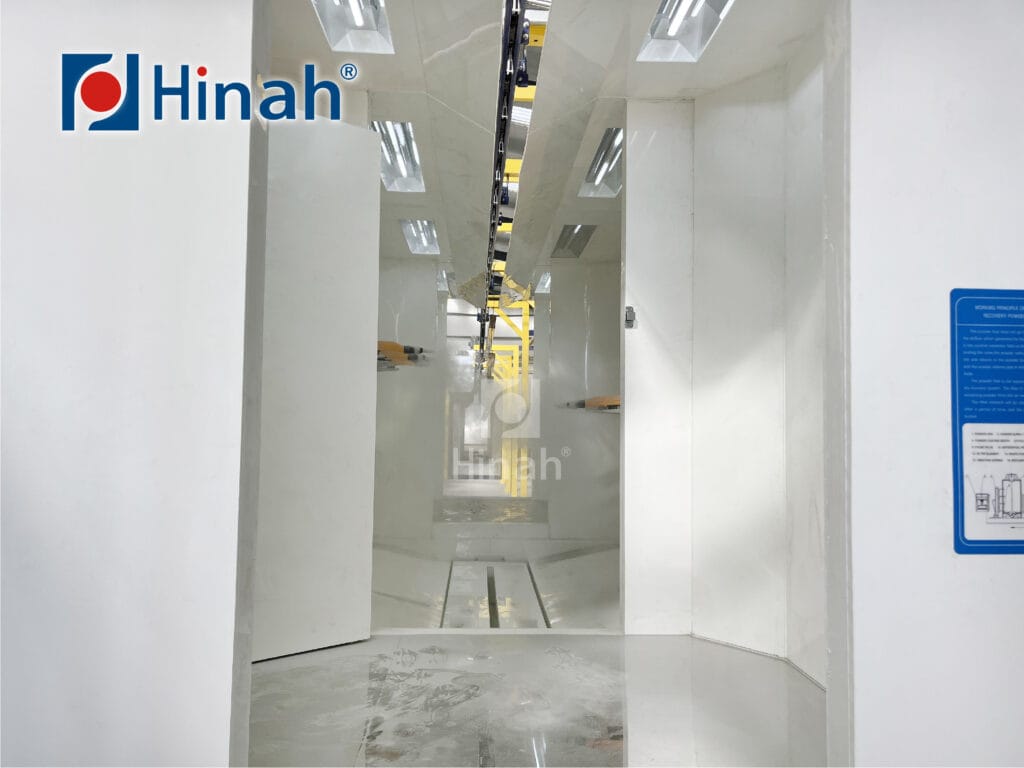
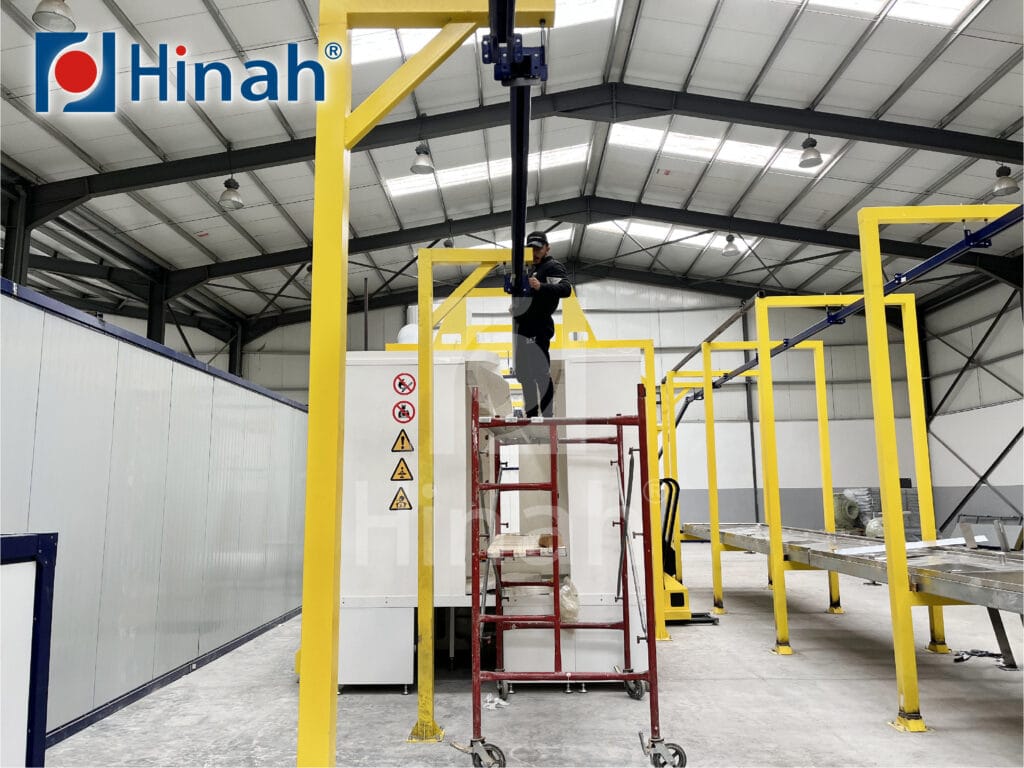
Secret #3: Military-Grade Durability with Industrial Powder Coating
In demanding industries where performance and longevity are critical, industrial powder coating stands out for its superior durability. Whether exposed to extreme weather, heavy use, or chemical exposure, powder-coated surfaces maintain their integrity far longer than traditional finishes.
- Superior Corrosion Resistance
Industrial equipment and metal components often face corrosive conditions, from moisture and salt exposure to industrial chemicals. Industrial powder coating forms a seamless, protective barrier that resists oxidation, rust, and chemical degradation. This makes it a preferred choice for marine, aerospace, and heavy machinery applications, where long-term corrosion resistance is essential.
- Impact and Abrasion Toughness
Unlike conventional liquid coatings, powder coatings bond electrostatically and cure into a tough, resilient layer. This provides excellent resistance against impact, chipping, and abrasion, ensuring that coated surfaces withstand mechanical stress without premature failure. Whether applied to automotive frames, military-grade equipment, or industrial tools, industrial powder coating delivers unmatched toughness.
- Long-Lasting Aesthetic and Performance
Durability isn’t just about protection—it’s also about maintaining appearance and functionality. Industrial powder coatings offer superior UV resistance, preventing fading and chalking even under prolonged sun exposure. Additionally, these coatings maintain their gloss and texture over years of use, ensuring that products not only perform reliably but also look professional and well-maintained.
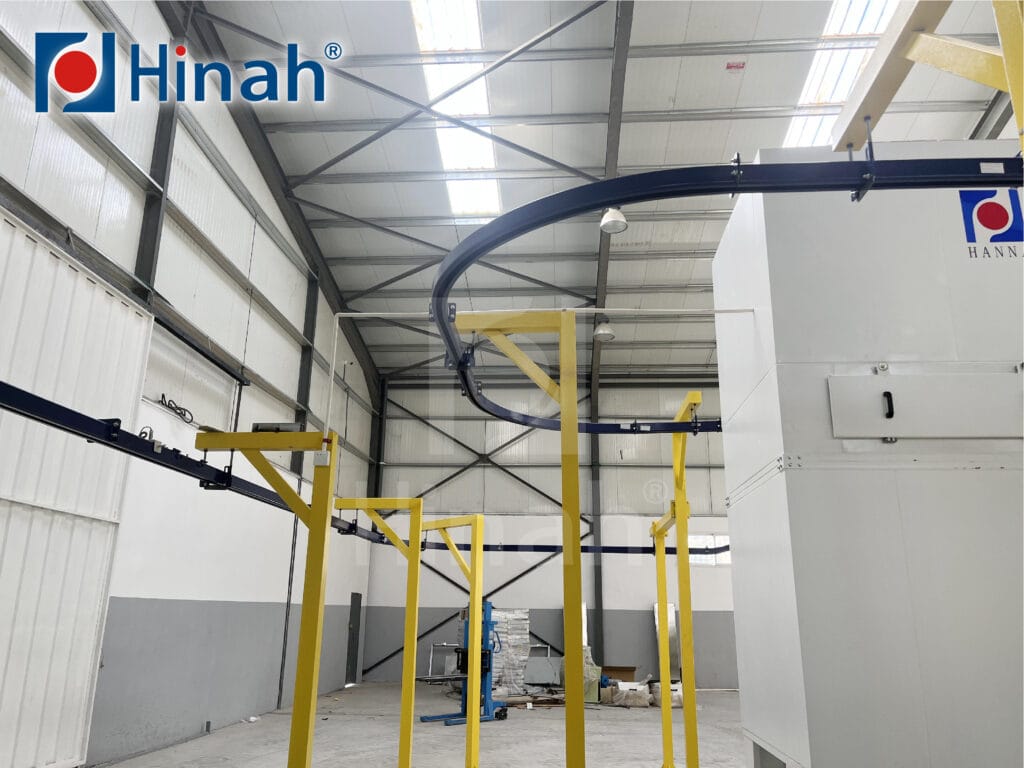
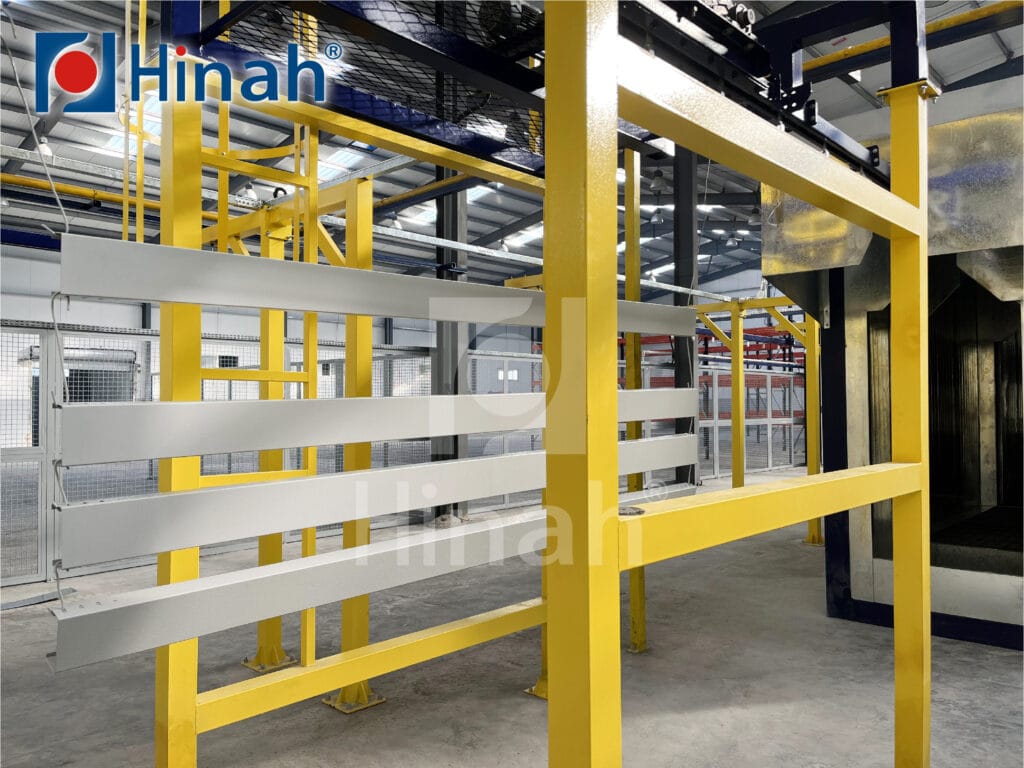
Secret #4: Speed Optimization in Industrial Powder Coating Lines
Modern industrial powder coating lines are designed for maximum efficiency, leveraging automation to accelerate production without compromising quality. Robotic application systems ensure rapid and consistent coverage, reducing manual intervention and errors. Advanced curing technologies, such as infrared and convection ovens, further cut processing time by optimizing heat distribution. Meanwhile, streamlined conveyor systems minimize downtime and eliminate bottlenecks, keeping operations smooth and continuous. With real-time monitoring and control, manufacturers can fine-tune every stage of the coating process, enhancing precision and overall productivity.