As an important equipment in the coating industry, automatic powder coating machine is gradually replacing traditional manual spraying, significantly improving production efficiency and product quality. In many manufacturing industries, especially the automotive and home appliance fields, the automated powder coating line helps companies shorten production cycles, reduce costs and improve coating consistency. This article will explore how automatic powder coating machines can promote technological progress in the manufacturing industry by improving production efficiency, reducing costs and optimizing quality.
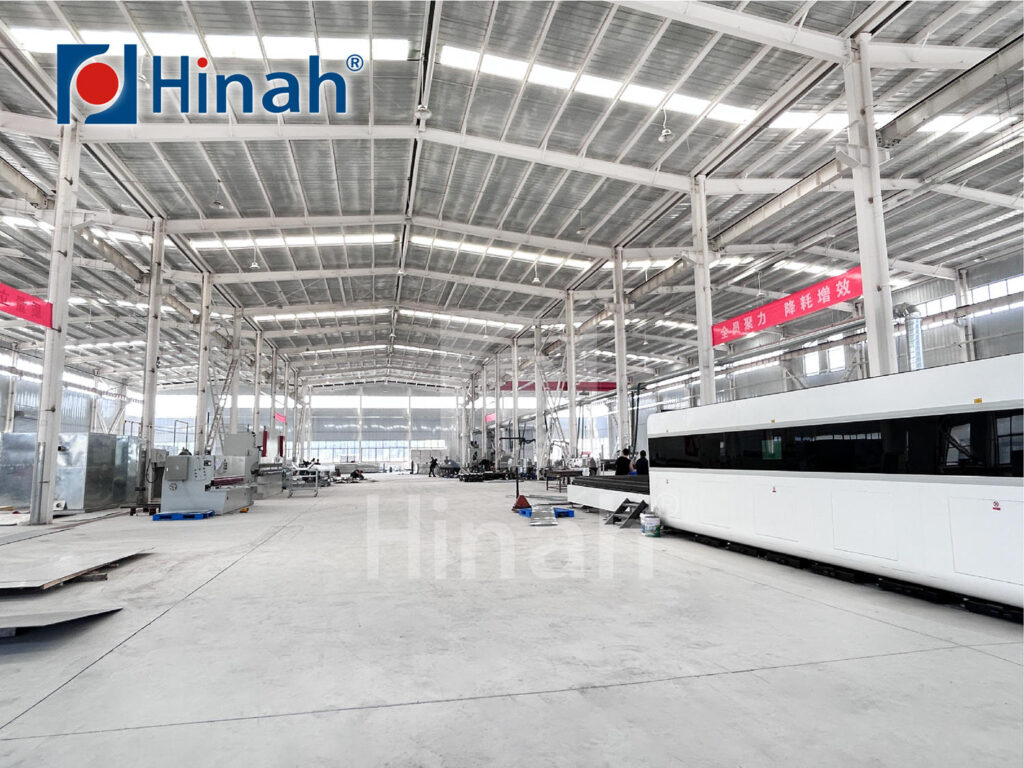
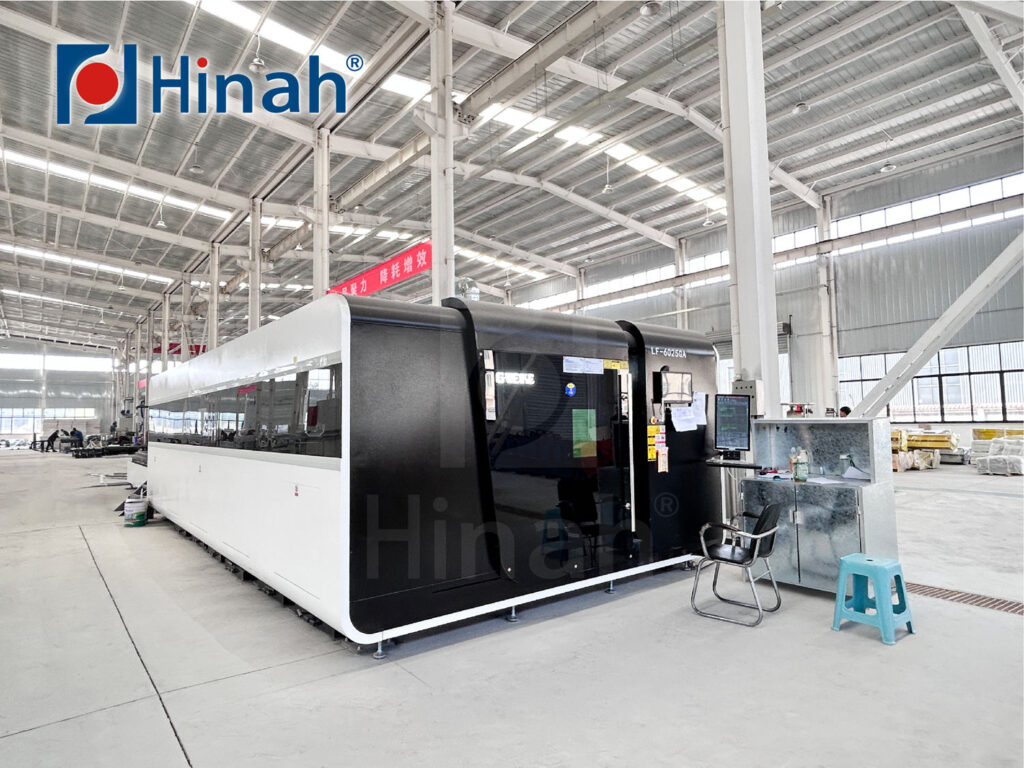
I. What is automatic powder coating machine?
Automatic powder coating machine is an automated equipment that uses electrostatic action to evenly spray powder coating on the surface of the object to be coated. Unlike traditional liquid coating spraying, automatic powder coating machine uses dry powder coating, which makes it have obvious advantages in environmental protection, coating quality and production efficiency
Working principle of automatic powder coating machine
- Spraying: The spray gun sprays powder coating to the surface of the object to be coated through compressed air or airflow.
- Electrostatic adsorption: The paint particles are charged by corona action and adsorbed by the surface of the object.
- Curing: The object enters the curing oven, and the paint melts at high temperature to form a solid coating.
The basis of automatic spraying technology
Automatic spraying technology accurately adjusts the spraying parameters through the control system to ensure uniform coating. The equipment is equipped with a powder recovery system to effectively reduce waste and reduce costs. Automation makes the production process more efficient and flexible, while reducing manual operations and errors.
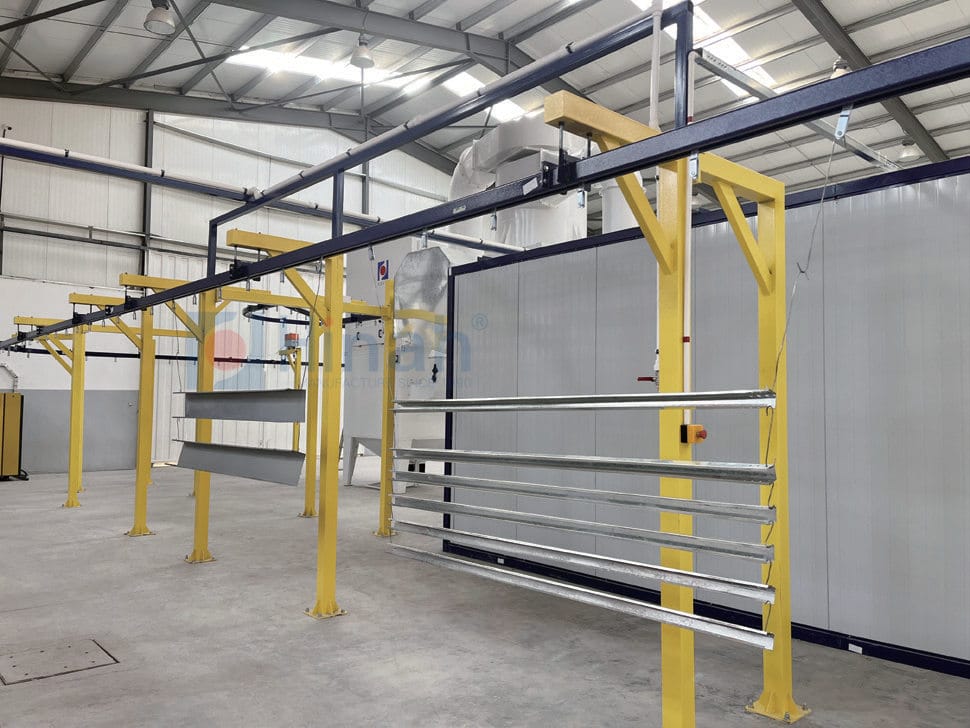
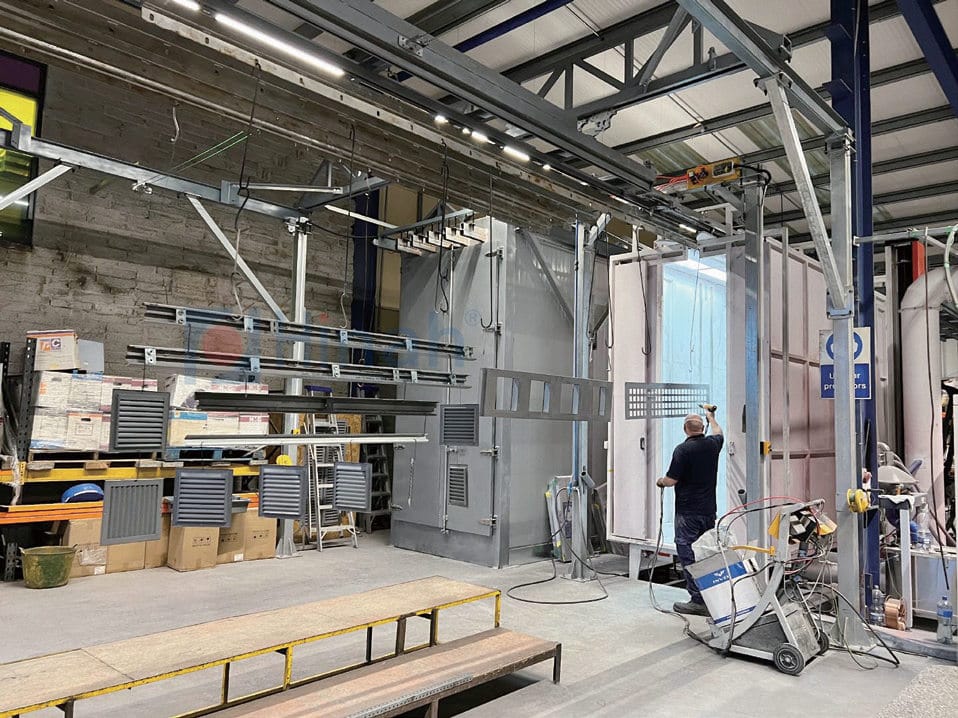
II. How does an automatic powder coating line work?
An automated powder coating line is an integrated production system designed to efficiently complete the coating process through automated technology. It usually consists of multiple key parts, each of which plays a vital role to ensure the quality of the coating and production efficiency.
Components of an automated powder coating line
1. Powder coating pretreatment system
This is the first part of the automated powder coating line, which is mainly responsible for cleaning and preparing the surface of the object to be coated. The pretreatment process includes steps such as sandblasting, chemical cleaning, and phosphating to remove oil, rust, and impurities to provide better adhesion for the coating.
2. Powder coating booth
The powder coating room is the core part of the coating line, including a powder coating gun, a powder supply system, and a control device. The spray gun sprays the powder coating evenly onto the surface of the object through electrostatic action, and the powder supply system ensures a stable coating flow. Spraying parameters (such as powder flow, spray pressure, and spray angle) are automatically adjusted by the control system.
3. Powder coating curing oven
The painted workpiece will enter the curing oven, where the powder coating is heated and cured to form a strong and durable coating. The curing oven usually heats with hot air or infrared rays to ensure that the coating is completely cured within the specified time.
4. Powder coating conveyor system
The conveyor system is used to convey the workpiece to be coated from one process to the next process, reducing manual intervention and improving production efficiency. The conveyor system usually uses a chain or roller conveyor to ensure the smooth movement of objects on the production line.
5. Powder recovery system
In order to reduce paint waste, the automated powder coating line is usually equipped with a powder recovery system. The system uses a negative pressure device to suck back the powder coating that fails to adhere to the object and recycles it to reduce production costs.
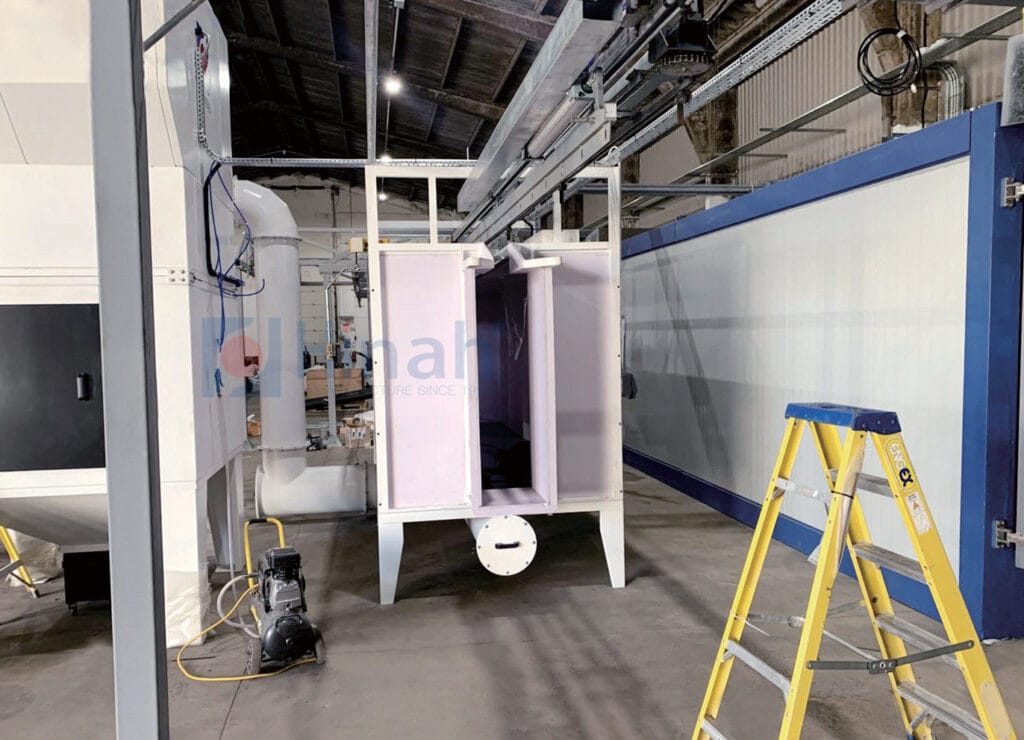
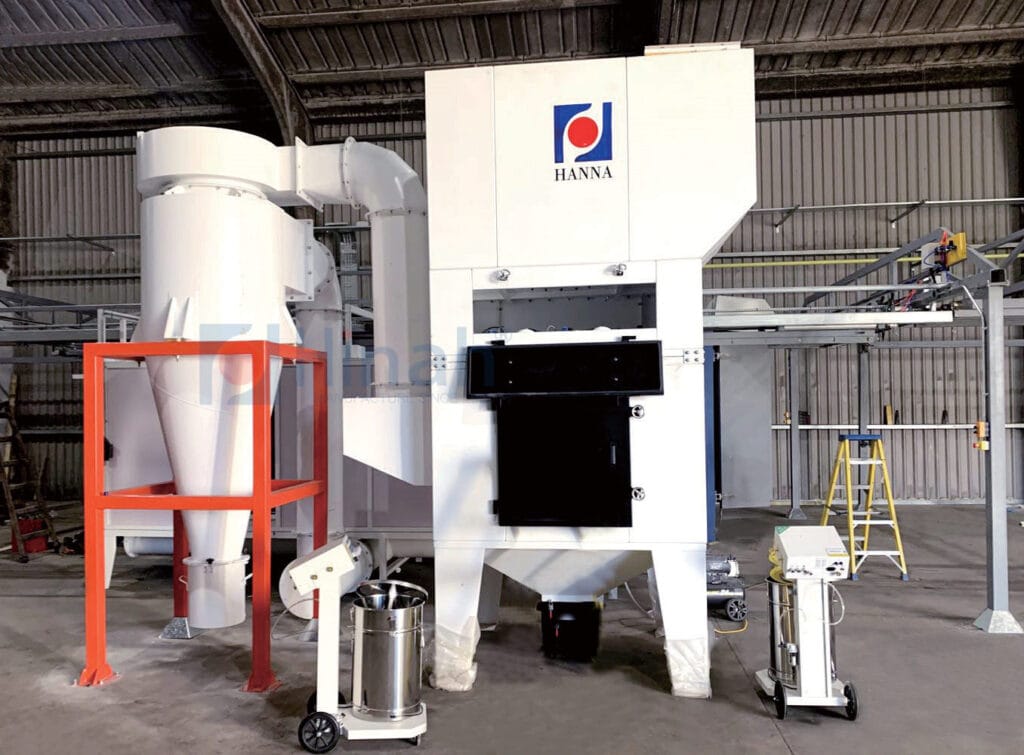
III. How does the automatic powder coating machine improve production efficiency?
Automatic powder coating machines significantly improve production efficiency through some advanced technologies and automation features. Here are the main ways:
Increase production speed
The automatic powder coating machine adopts high-speed spraying technology and can complete the coating task in a shorter time. Compared with traditional manual spraying, automated equipment can run continuously without manual pauses and adjustments, thus greatly increasing the overall speed of the production line. In addition, the automatic spraying system ensures the uniformity and quality of the coating by optimizing parameters such as spraying angle and spraying pressure, reducing the coating cycle and further increasing the production speed.
Reduce manual intervention
The introduction of automated powder coating machines has significantly reduced reliance on manual operations. The machine’s ability to automate spraying, adjustment and control reduces operator involvement, thereby avoiding human error and inconsistency. The automated system can also autonomously adjust spraying parameters (such as powder flow rate, spray gun position, etc.) according to preset programs to complete complex painting tasks without manual intervention. This not only improves production efficiency but also reduces labor intensity and error rates in operations.
Simplification of the production process
The automatic powder coating machine integrates many links that traditionally require manual operation, simplifying the production process. The spraying, recycling, curing, and other processes are seamlessly connected under the control of automated equipment, avoiding repeated steps and unnecessary interruptions in manual operations. In addition, automatic spraying technology can achieve continuous production, greatly reducing downtime on the production line, and making the entire production process smoother and more efficient.
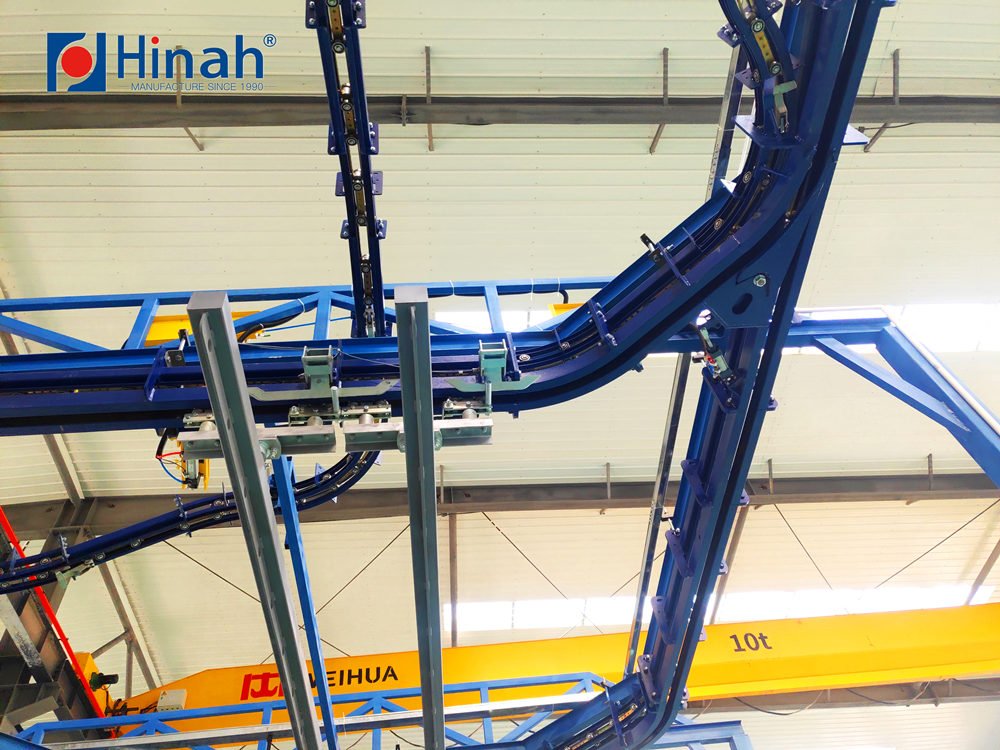
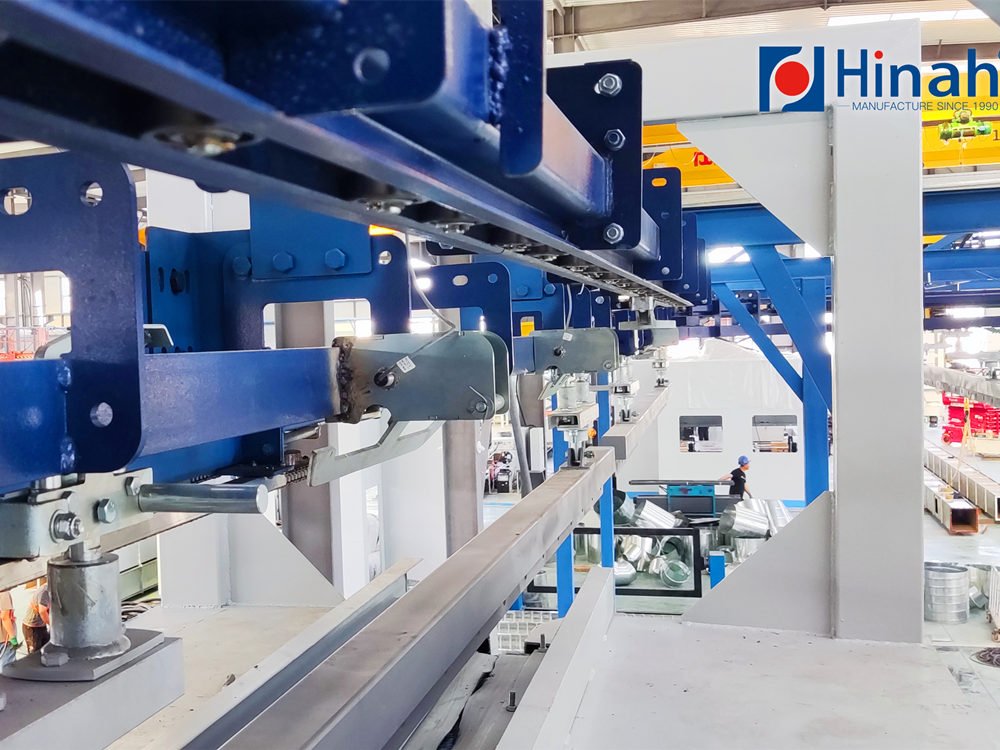
IV. How to reduce costs in the powder coating process?
- Reduce raw material waste
Automatic powder coating lines significantly reduce paint waste by precisely controlling the powder paint used. The powder coating equipment automatically adjusts the spray amount according to the object’s size, shape, and coating thickness requirements to ensure that the powder sprayed can effectively adhere to the object’s surface each time. Modern automatic powder coating lines are also equipped with a powder recycling system, which can collect powder coatings that have failed to adhere and reuse them, greatly reducing coating consumption and improving the efficiency of raw material use.
- Reduce energy consumption
The curing oven and heating system of the automatic powder coating line can accurately adjust the temperature and heating time according to production needs. Compared with traditional manual operations, automated systems can reduce unnecessary energy waste by optimizing the heating process. For example, automatic powder coating lines can intelligently adjust curing time and temperature settings according to different coating requirements to maximize energy efficiency. In addition, the heat recovery system can effectively recover excess heat and reuse it, further reducing energy consumption.
- Reduced labor costs
The automatic powder coating line significantly reduces dependence on labor by automating many traditional manual operations. The machine automatically completes tasks such as spraying, adjusting and recycling powder coatings, reducing manual intervention and improving production efficiency and quality consistency. The automated spraying system can operate around the clock, reducing the error rate and maintenance costs of manual operations, thus significantly reducing the company’s labor expenses.
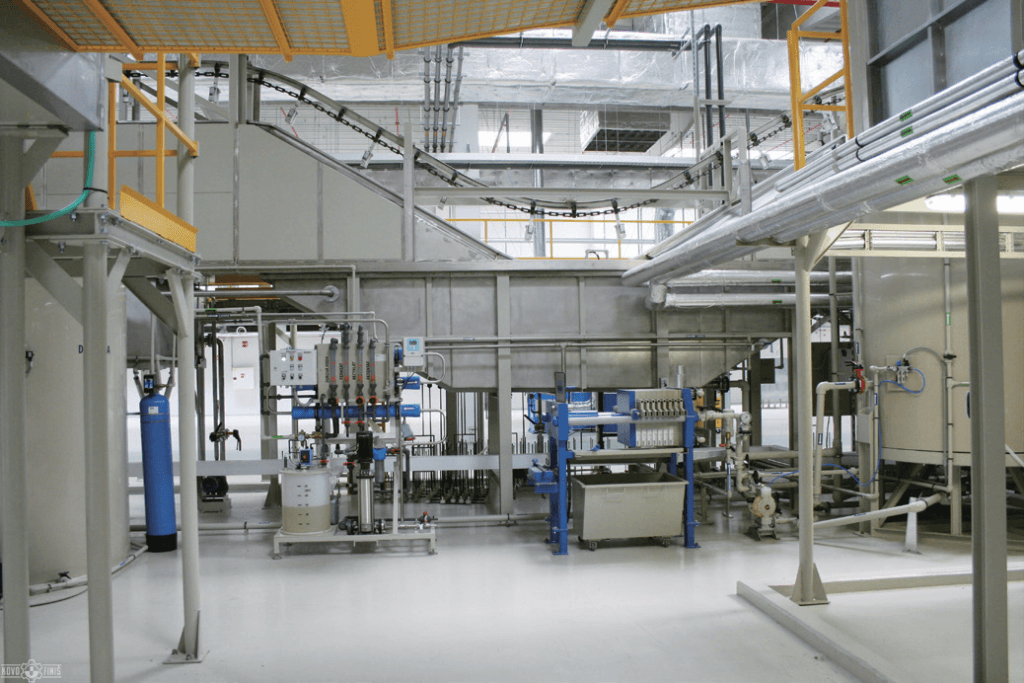
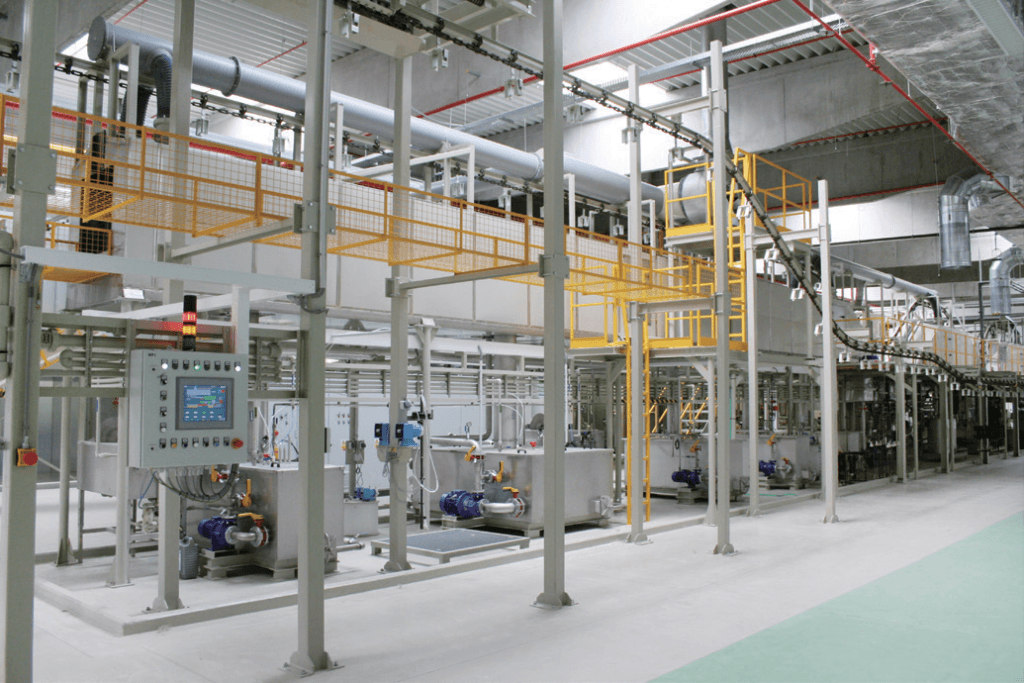
V. How to improve coating quality?
Improving coating quality is a key goal when using automatic powder coating machines.
- Precisely control coating thickness and uniformity
The automatic powder coating machine can adjust spraying parameters (such as spray gun angle, powder flow and air pressure, etc.) through a precise control system to ensure uniform coating thickness. Such precise spraying not only avoids uneven coating and improves the appearance and durability of the coating, but also reduces rework and paint waste, significantly improving coating quality.
- Optimize powder coating adhesion
The automatic powder coating machine uses the principle of electrostatic spraying to make the powder coating better adhere to the surface of the object. By optimizing spraying parameters and powder selection, automatic powder coating machines can enhance the adhesion of the coating to the substrate and prevent the coating from peeling off or peeling off. This not only improves the quality of the coating but also improves the durability of the coating and enhances the product’s resistance to corrosion and wear.
- Flexibly adjust painting parameters to meet different needs
The automatic powder coating machine has the ability to quickly adjust spraying parameters and can flexibly adjust spraying settings according to the size, shape, and material of different products. This high flexibility enables automatic powder coating machines to quickly adapt to different production needs, ensuring high-quality coating under changing production conditions.
VI. Conclusion
By precisely controlling the spraying process, the automatic powder coating machine not only improves production efficiency but also reduces costs by reducing paint waste and optimizing energy use. At the same time, the automatic powder coating machine ensures the uniformity and adhesion of the coating, thereby ensuring high-quality coating results.
In the future, automated powder coating technology will further develop in the direction of intelligence and environmental protection. The application of intelligent control systems and big data analysis will improve production flexibility and quality control. Advances in green and environmentally friendly technologies will make the spraying process more energy-saving and low-emission, pushing the industry toward sustainable development.