More and more manufacturers are turning to automatic painting line to improve product quality and reduce rework rates. Traditional manual spraying is easily affected by human factors, resulting in uneven coating, thickness deviation and other problems. Modern automated painting lines, with precise control and intelligent technology, have successfully reduced rework rates by 63%, significantly improving production efficiency and cost-effectiveness. Today we will explore the secrets of automatic painting line.
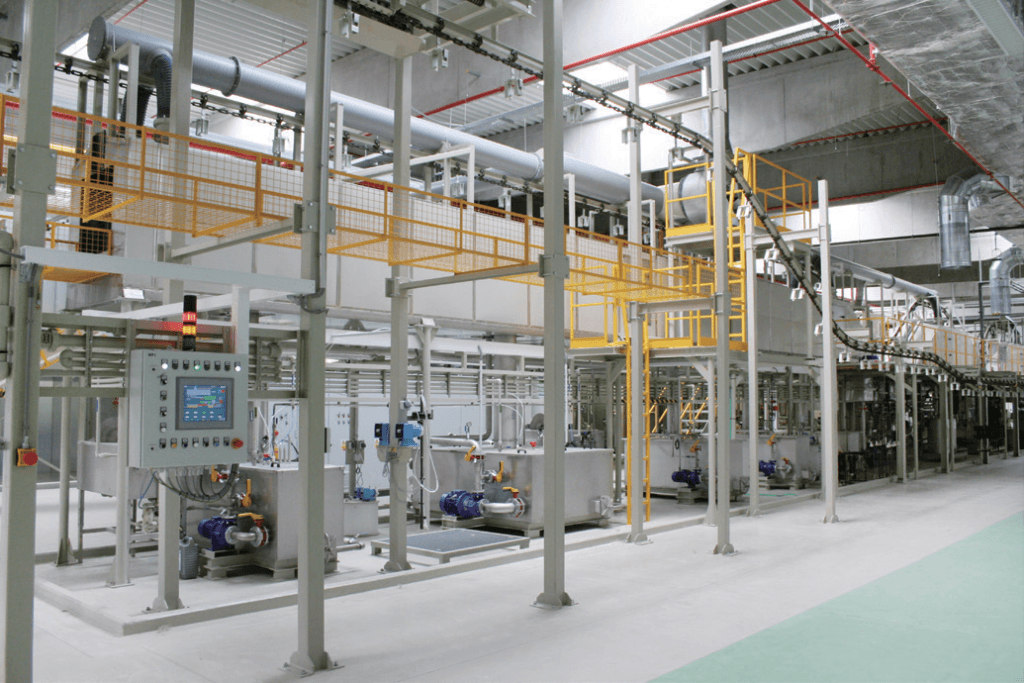
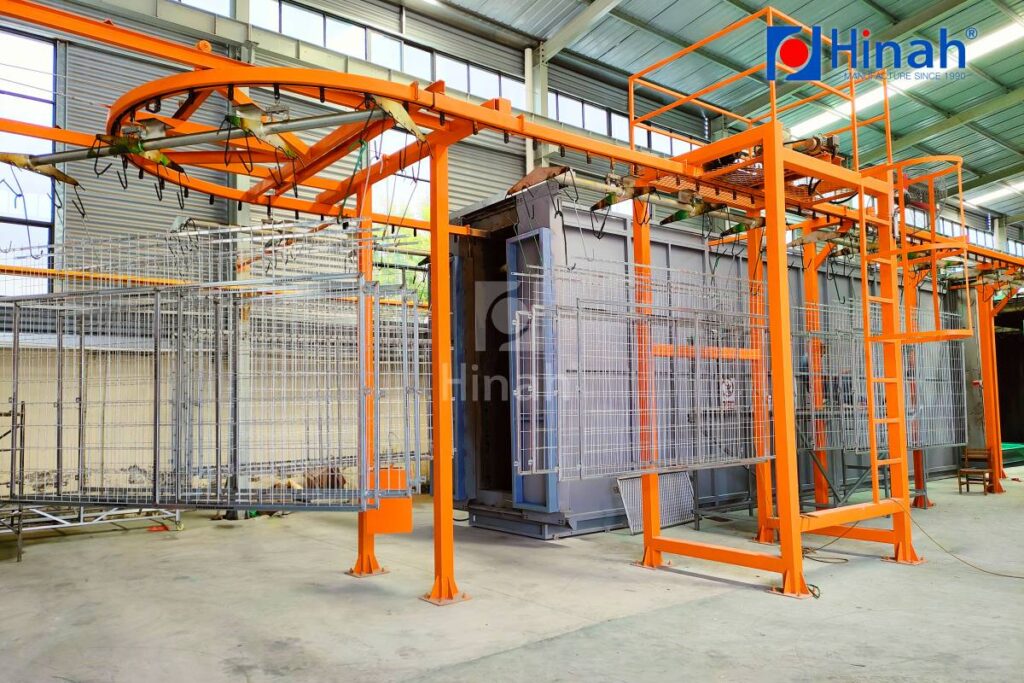
The Hidden Cost of Manual Painting Errors
Relying on manual painting methods may seem cost-effective at first, but the hidden costs can quickly add up. Inconsistent coating thickness, uneven coverage, and operator fatigue often lead to defects that require costly rework.
- Material Waste: Manual painting frequently results in excessive overspray, wasting expensive coating materials.
- Labor Costs: Skilled operators must spend additional time correcting mistakes, increasing overall labor expenses.
- Production Delays: Rework and touch-ups slow down the production line, reducing throughput and affecting delivery schedules.
- Quality Risks: Poor paint adhesion or uneven finishes can lead to product recalls or customer dissatisfaction, damaging your brand reputation.
Switching to an automated painting line can minimize these issues, ensuring consistent results while reducing costs.
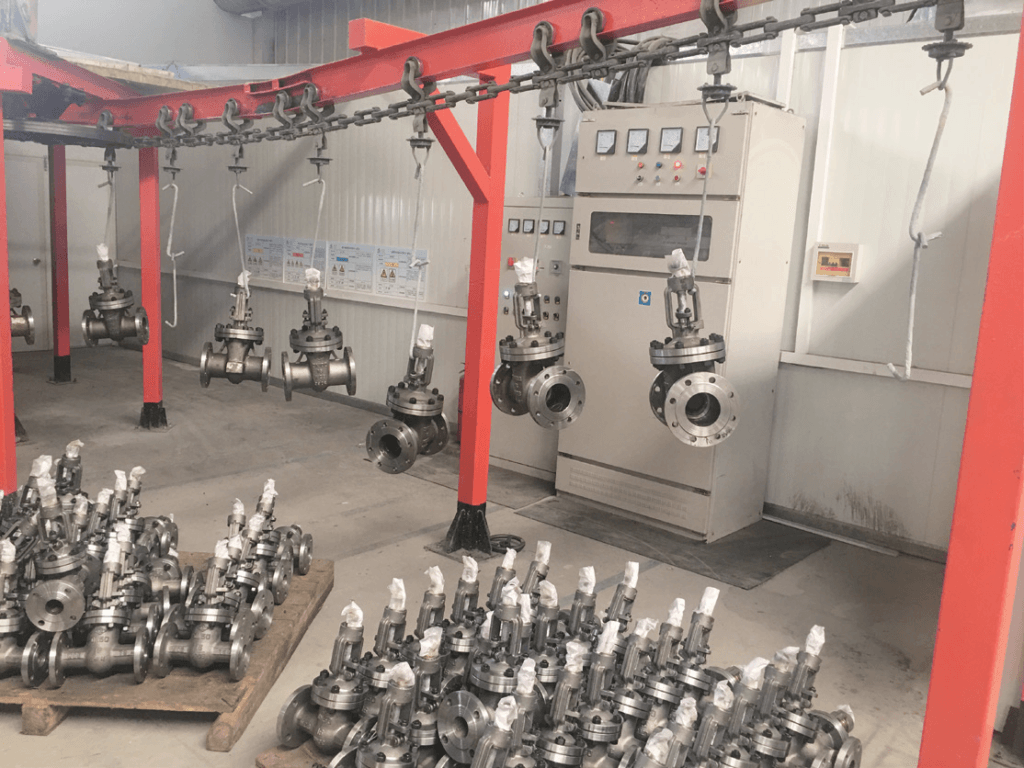
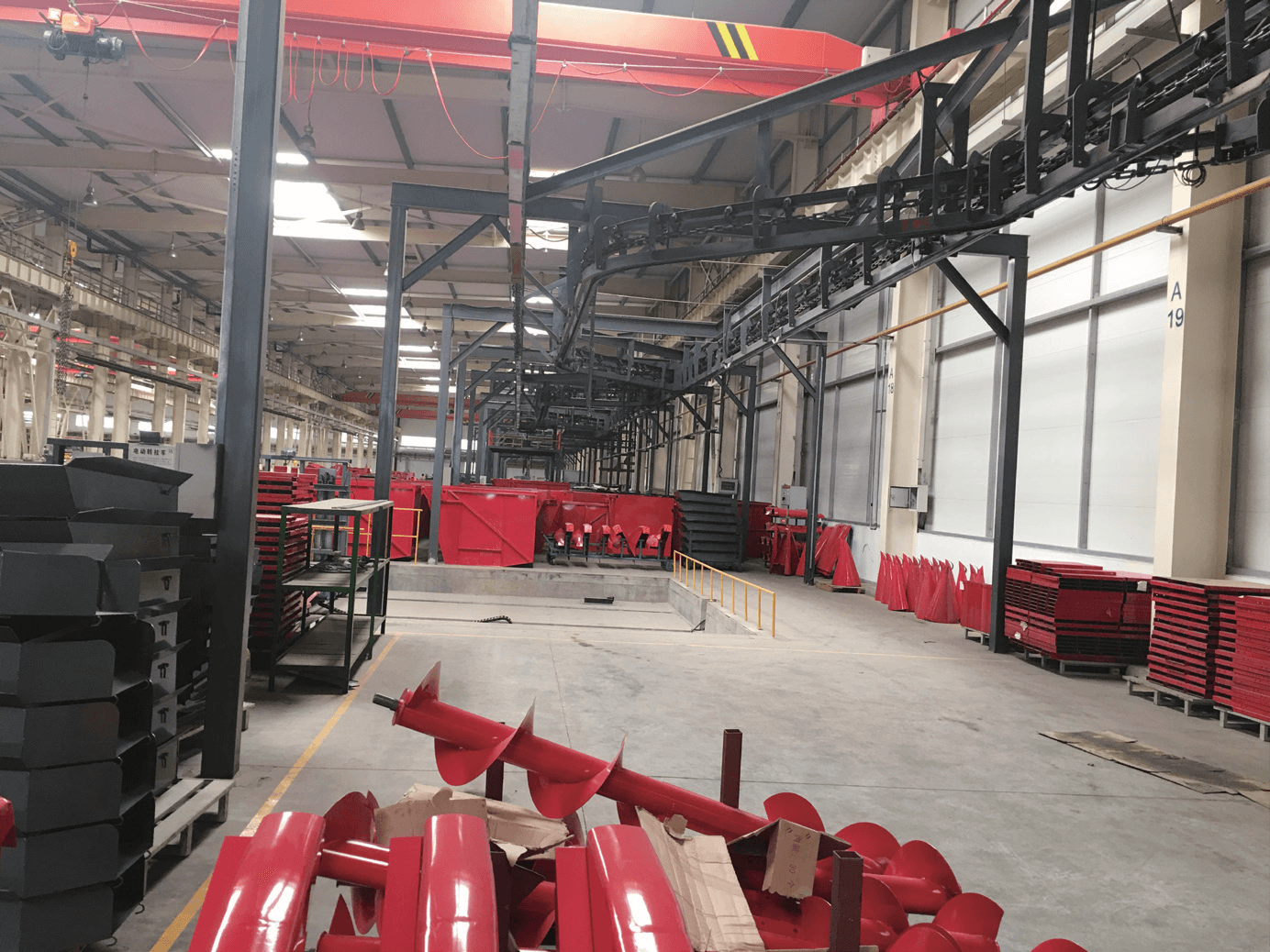
3 Core Technologies Powering Modern Automatic Painting Lines
Modern automatic painting lines leverage advanced technologies to ensure precision, efficiency, and minimal rework. Three key innovations drive their superior performance:
Robotic Painting Systems
Robotic arms equipped with intelligent programming can follow precise spray paths, ensuring consistent coverage across complex surfaces. These systems adapt to various product shapes, reducing overspray and ensuring uniform coating thickness. Additionally, automated robots can operate continuously with minimal downtime, boosting productivity.
Real-Time Coating Thickness Monitoring
This technology uses sensors to measure coating thickness during application, allowing instant adjustments. By maintaining optimal thickness levels, manufacturers reduce material waste and avoid defects such as sagging or insufficient coverage. This real-time feedback system is crucial for achieving high first-pass yield rates.
Self-Cleaning Nozzle Systems
Clogged nozzles are a common cause of spray defects. Self-cleaning nozzle systems automatically purge residual paint and debris, maintaining consistent spray patterns. This reduces downtime for manual cleaning and ensures smooth, uninterrupted production.
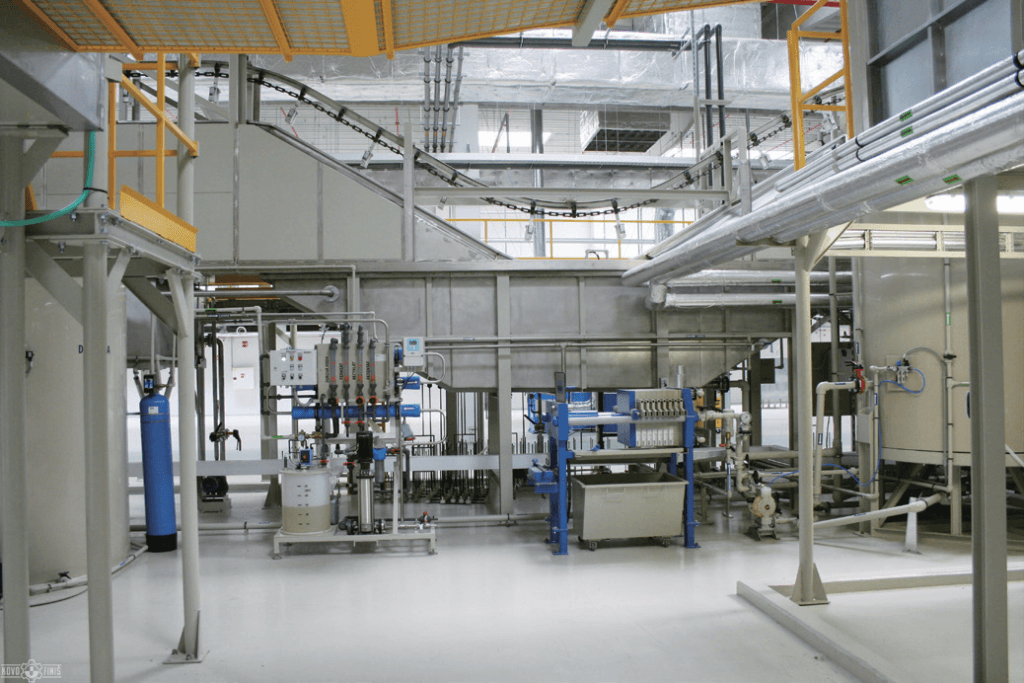
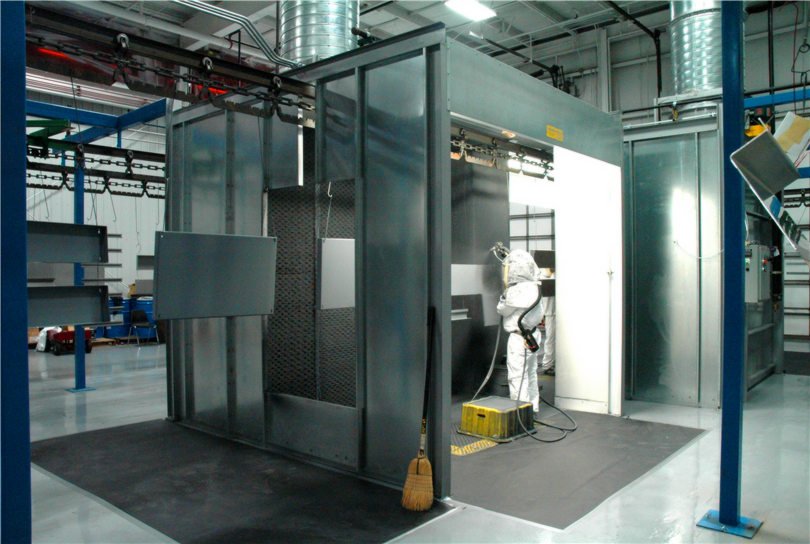
4 Metrics to Validate Your Automatic Painting Line’s Performance
Evaluating the performance of your automatic painting line requires tracking key metrics that reflect efficiency, quality, and cost-effectiveness. Here are four essential indicators to monitor:
- Transfer Efficiency
Transfer efficiency measures the percentage of coating material that successfully adheres to the product surface versus the amount wasted. A high transfer efficiency not only reduces material costs but also minimizes environmental impact. Modern automatic painting line equipped with precision spray technology can significantly improve this metric.
- First-Pass Yield
FPY reflects the percentage of products that meet quality standards without requiring rework. A well-optimized automatic painting line should achieve a high FPY by ensuring consistent coating thickness, uniform coverage, and minimal defects.
- Mean Time Between Failures (MTBF)
MTBF measures the average operational time between equipment failures. A higher MTBF indicates improved system reliability and less unplanned downtime. Regular maintenance, combined with advanced monitoring systems, can extend MTBF in automated setups.
- Energy Consumption per Unit
Energy efficiency is a crucial factor in reducing operational costs. Tracking energy consumption per coated unit helps identify inefficiencies in heating, curing, or ventilation systems. Advanced automatic painting lines often feature energy-saving technologies to minimize power usage without compromising performance.
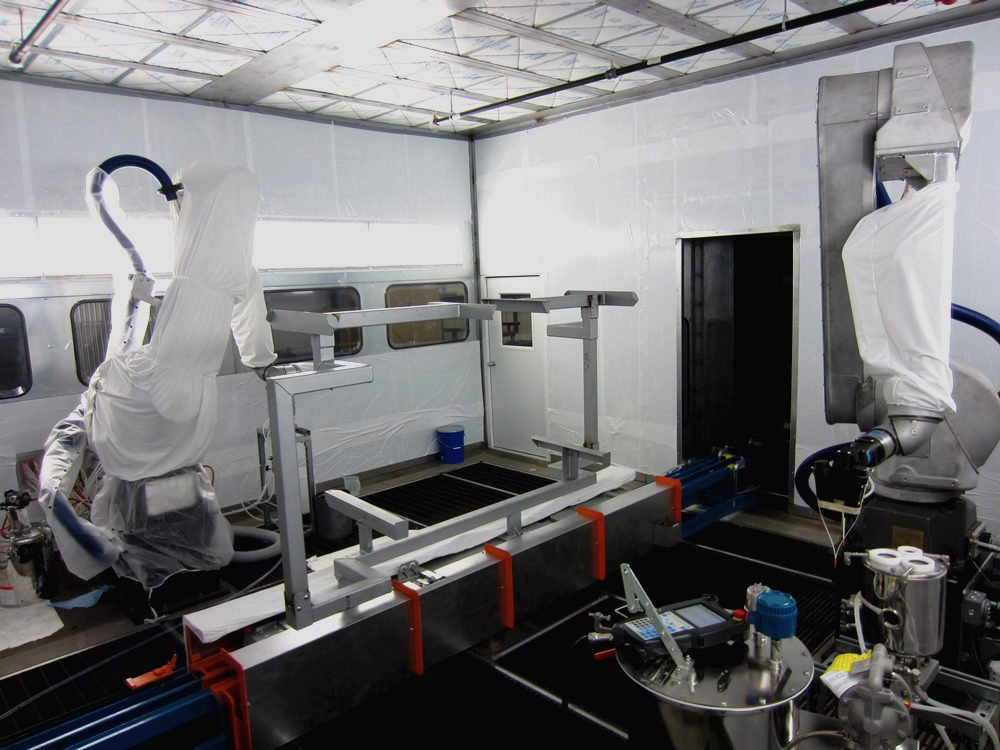
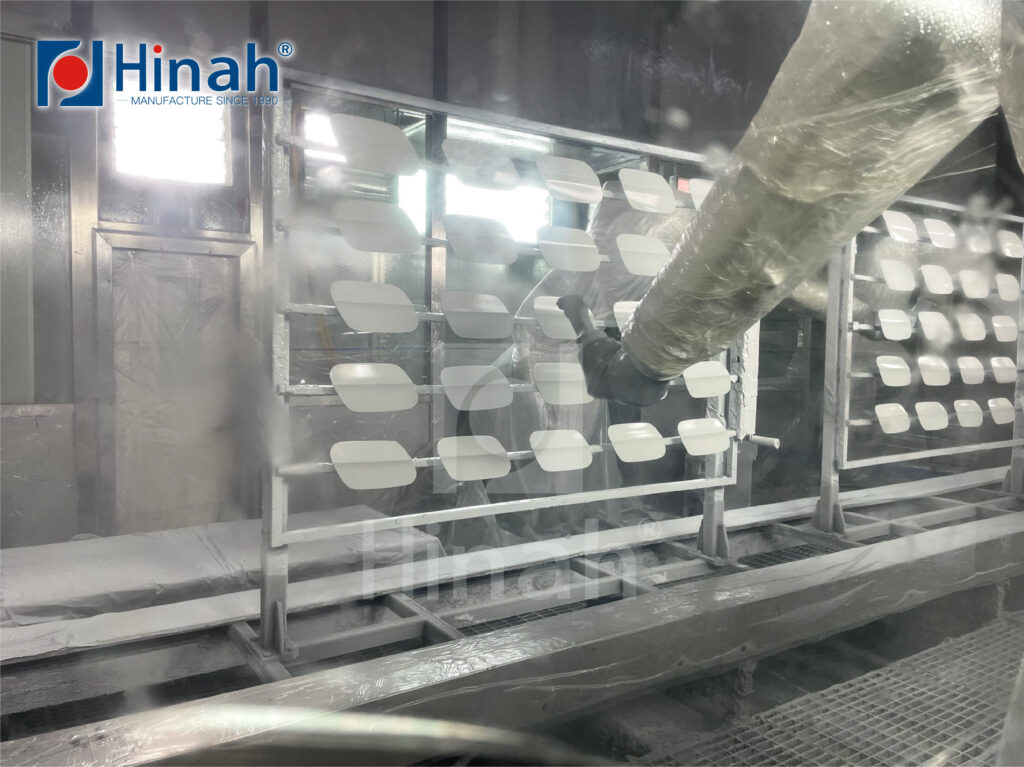
Conclusion
Investing in an automatic painting line is a strategic move for manufacturers seeking to reduce rework, improve efficiency, and maintain product quality. By adopting advanced technologies such as robotic painting systems, real-time coating monitoring, and self-cleaning nozzles, businesses can achieve higher transfer efficiency and first-pass yield. Tracking key performance metrics ensures continuous improvement, while scalable solutions provide the flexibility to grow with production demands. Embracing these innovations empowers manufacturers to deliver superior results while controlling costs and minimizing waste.