Aluminum powder coating line is widely used in fields such as construction, automobiles, and consumer goods. It’s the key to achieving the functionalization and decoration of aluminum surfaces. However, with the continuous growth of market demand, companies not only need to meet the requirements of high-quality coating, but also must optimize cost control, production efficiency, and environmental performance. Therefore, how to design an efficient powder coating line has become the focus of industry attention. This article will discuss key elements such as the layout planning, equipment selection, process optimization, and management strategies of the coating line, and provide companies with a set of systematic design ideas to help improve their overall competitiveness.
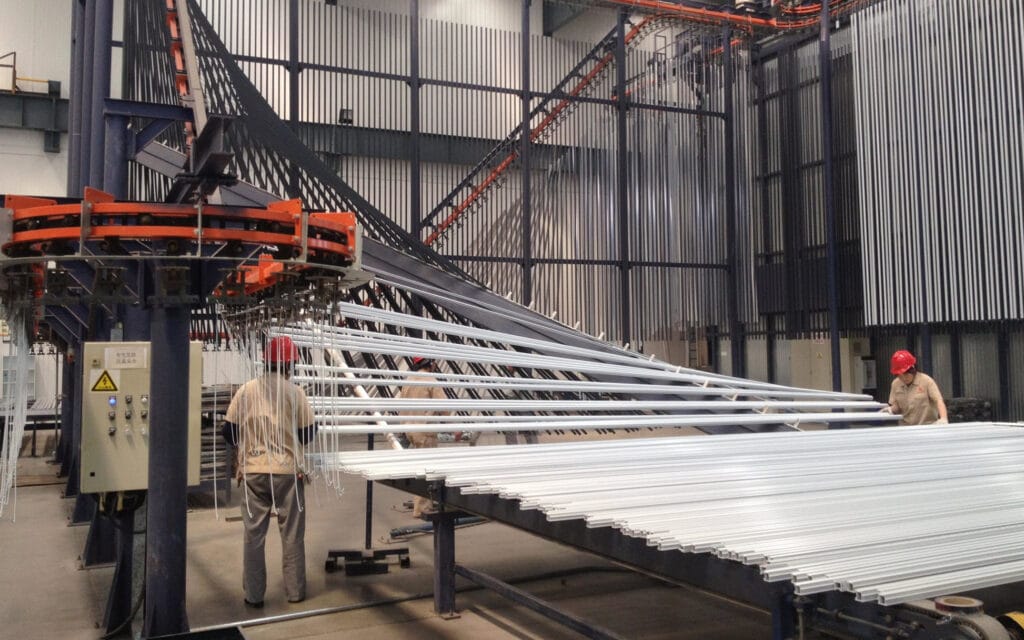
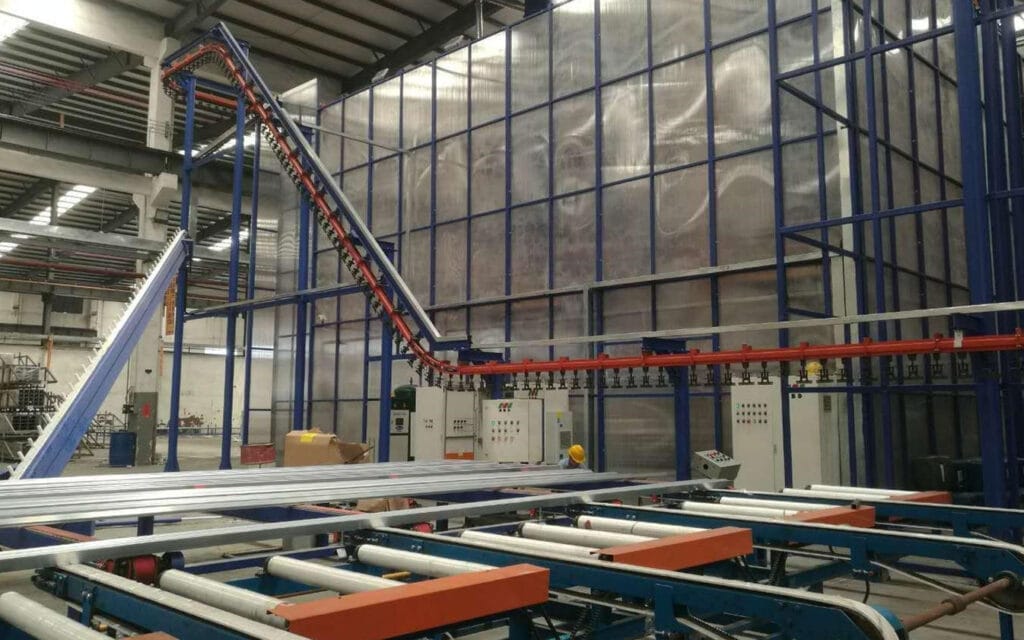
I.Reasonable planning of coating line layout
1.Process optimization
Ensuring the smooth flow of workpieces from pretreatment to curing and reducing handling and waiting time can be achieved through reasonable production line layout, such as adopting linear, U-shaped or circular layout, optimizing the design according to the factory space and workpiece characteristics to maximize efficiency and production continuity.
2.Maximizing space utilization
Design a compact and efficient layout according to the factory area and production needs, optimize the spacing between equipment, and reasonably plan the operation area and maintenance space to ensure that the production line can fully utilize the site and facilitate daily operation and equipment maintenance.
3.Environmental protection and safety measures
Emissions are effectively controlled by setting up exhaust gas treatment devices (such as VOC adsorption systems), and reasonable safety exits and fire prevention measures are planned to ensure that the production line meets both environmental protection requirements and safety production standards.
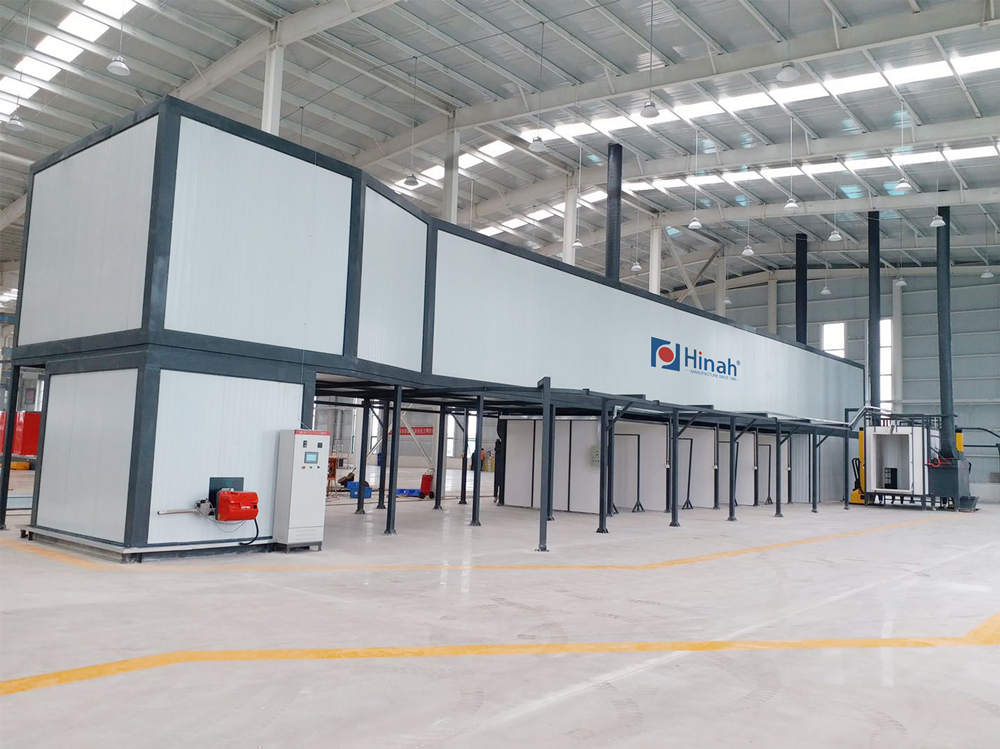
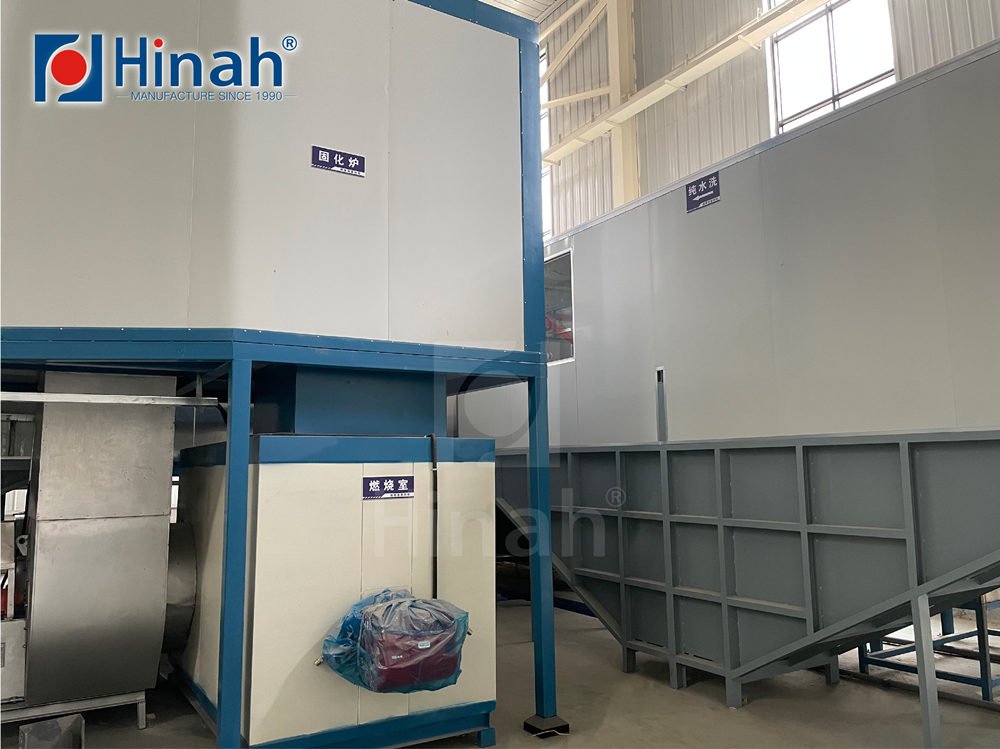
II.Selection and configuration of key powder coating equipment
1. Powder coating equipment
Select the automated powder coating robot or electrostatic coating guns to improve the uniformity and efficiency of coating, and customize the design of coating equipment according to the size and shape of aluminum workpieces to ensure that the equipment can meet the coating requirements of different workpieces and achieve the best coating effect.
2. Powder coating curing oven
For the coating requirements of aluminum profiles, the type of curing oven should be selected in combination with its production characteristics for analysis:
- Tunnel curing oven is suitable for mass-produced standard aluminum profiles, because of its strong continuous conveying capacity and high efficiency, it can meet the high production requirements of the assembly line, but requires a large space;
- Bridge curing oven is suitable for complex process production lines, which can flexibly connect between coating, curing, and cooling, and is particularly suitable for the production of aluminum profiles that require multi-step processing;
- Box curing oven is more suitable for the coating of small batches, multiple varieties or special-shaped aluminum profiles, with high flexibility and land advantages, but relatively low efficiency.
3. Powder coating recovery system
In the aluminum powder coating line, the selection of the recovery system directly affects the recovery efficiency and loss of powder. The large cyclone recovery system is suitable for processing larger particles of powder and can effectively recover the coarse powder generated during the spraying process, but the recovery effect of fine powder is poor, usually between 60% and 80%; while the filtration system can efficiently capture fine powder and has a high recovery efficiency, especially for powders less than 5 microns, which can reach more than 90%. In order to improve the utilization rate of powder and reduce waste, the two can be used in combination. The cyclone separator first performs coarse separation, and then captures fine powder through the filtration system. At the same time, the filter medium is cleaned regularly and the air flow parameters are optimized to ensure the efficient operation of the recovery system and minimize powder loss.
4. Powder coating conveyor system
In the design of aluminum powder coating line, the selection of automated powder coating conveyor systems is crucial. It can ensure the smooth transportation of aluminum profiles during the production process and avoid damage or waste caused by unstable transportation.
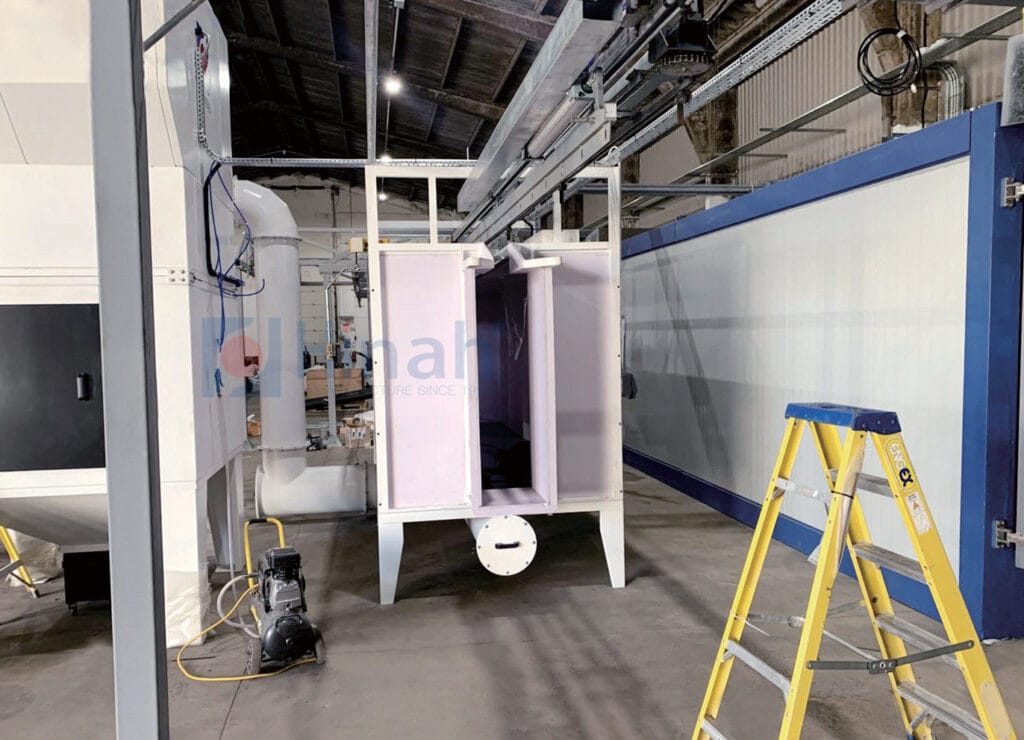
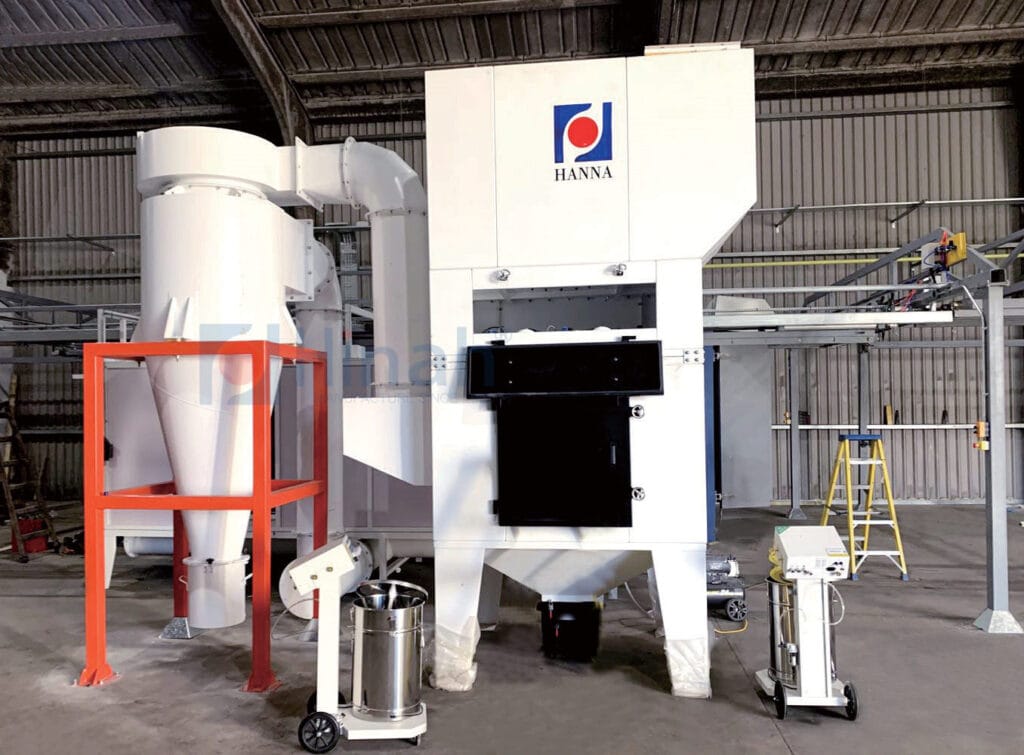
III.Optimization of process flow
1. Importance of surface pretreatment
Degreasing, decontamination, oxide film treatment and anti-corrosion treatment of aluminum materials are important technical steps to ensure the surface quality and coating adhesion of aluminum profiles. Oil removal and decontamination technology usually uses chemical cleaning or ultrasonic cleaning to ensure that the surface is pollution-free by dissolving oil and impurities; oxide film treatment uses an anodization process to form a dense oxide film on the surface of the aluminum to improve its corrosion resistance. , adhesion and coating stability. Anti-corrosion treatment generally adopts the method of sealing the pores of the oxide film, and improves the corrosion resistance of aluminum materials through the pore sealing process. Different treatment processes have a significant impact on the adhesion and coating durability. The anodized film can increase the adhesion between the coating and the substrate, while the sealing treatment enhances the corrosion resistance of the coating. Choosing the right process can improve the weather resistance and durability of aluminum while ensuring coating adhesion.
2. Control of powder spraying process parameters
Optimizing electrostatic voltage, spray distance and powder particle size are key to ensuring coating uniformity and quality. The electrostatic voltage should be adjusted according to the shape of the aluminum material and the characteristics of the powder, and is generally controlled at 60-90kV to ensure uniform adsorption of powder; the spraying distance is usually kept between 15-30cm to avoid being too close to cause powder accumulation or being too far away to affect adhesion; The particle size should be selected between 10-45 microns. Excessive particle size will reduce the fineness of the coating, while too small a particle size may increase recycling loss. In order to avoid coating defects, it is necessary to control the spray thickness to avoid sagging; ensure that the workpiece and powder are dry to prevent bubbles; adjust the baking temperature and time to avoid orange peel caused by uneven heating. Stabilizing equipment parameters and cleaning the spray gun can also help improve coating quality.
3. Refined management of curing process
Control of curing time and temperature profile is critical to powder coating quality. The curing temperature is usually set at 180°C-220°C, and the curing time is 10-20 minutes to ensure that the coating is completely cured. The temperature curve should be smooth and avoid sharp rises and falls to prevent cracks, bubbles or loss of adhesion in the coating. By precisely controlling the curing process, the durability and performance of the coating can be ensured.
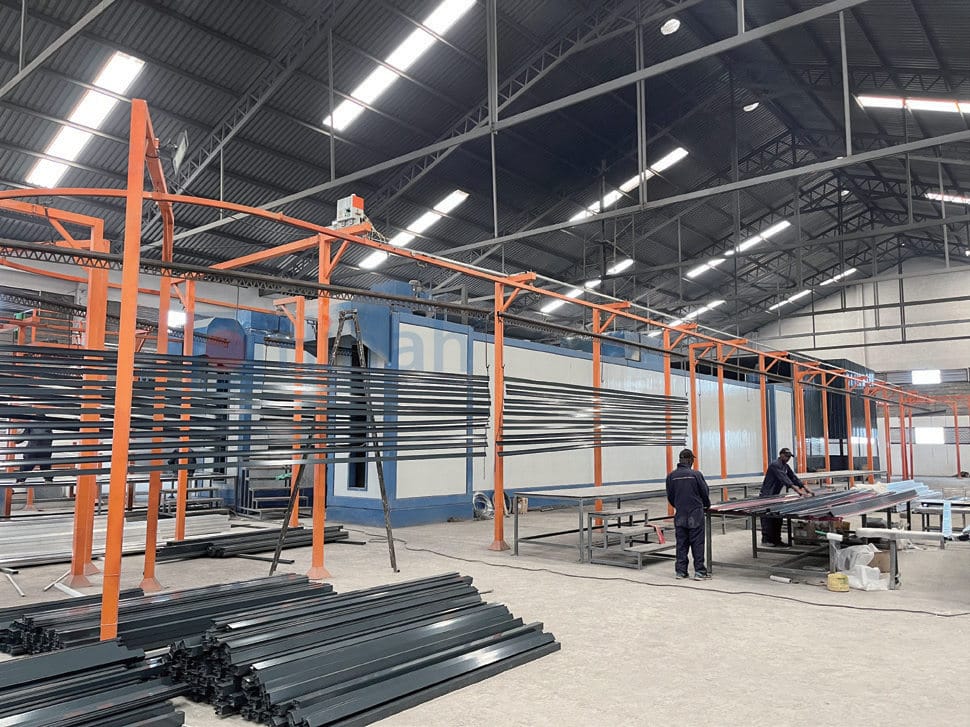
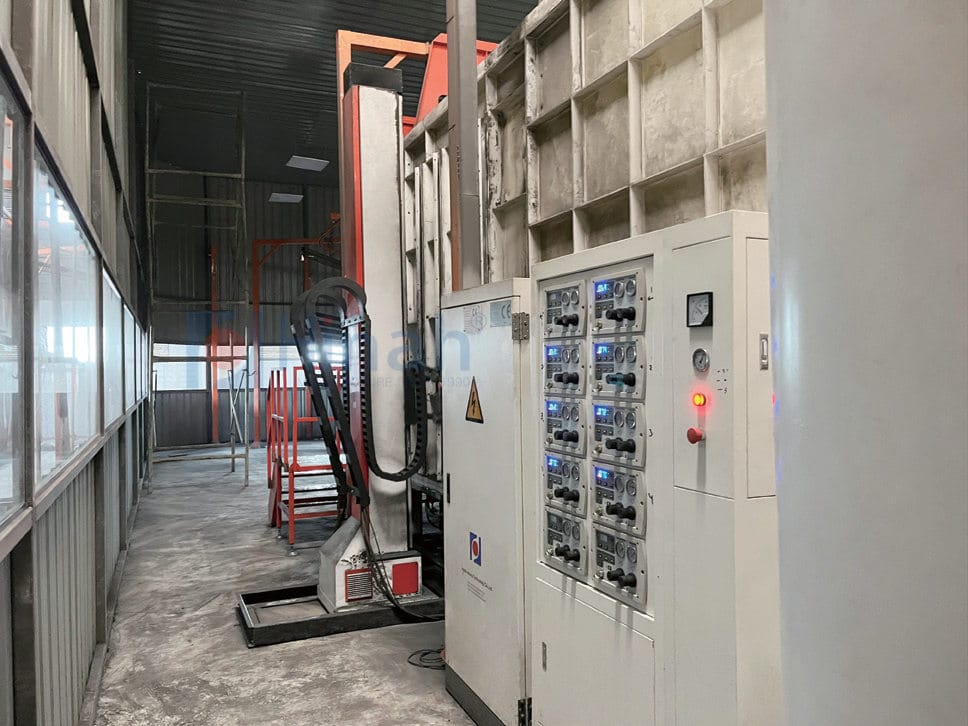
IV.Application of intelligence and automation
1.Intelligent production monitoring system
The intelligent production monitoring system collects and analyzes data in real-time to monitor key parameters during the spraying process, such as temperature, spray thickness, etc., to ensure the efficiency of the production line and the consistency of product quality. The system can also provide early warning of equipment failure and make automated adjustments to optimize the production process and reduce manual intervention and downtime.
2.Automated upgrade case
A powder coating factory achieved automation upgrades by introducing powder coating robots and automatic powder recovery systems. Spraying robots improve spraying accuracy and consistency and reduce manual intervention, while automatic powder recovery systems optimize powder use and reduce waste and environmental pollution. The upgrade significantly improves production efficiency and cost-effectiveness.
V.Paths to achieve environmental protection and energy conservation
1.Selection of green materials
Choosing low-volatility powder coatings with fewer harmful substances can help reduce environmental pollution and improve worker safety.
2.Integration of energy-saving technologies
Adopt high-efficiency heating system and energy recovery technology to optimize energy use and reduce production energy consumption.
3.Reduce waste and emissions
By optimizing the spraying process and recycling system, powder waste and exhaust emissions are reduced to achieve environmental protection goals.
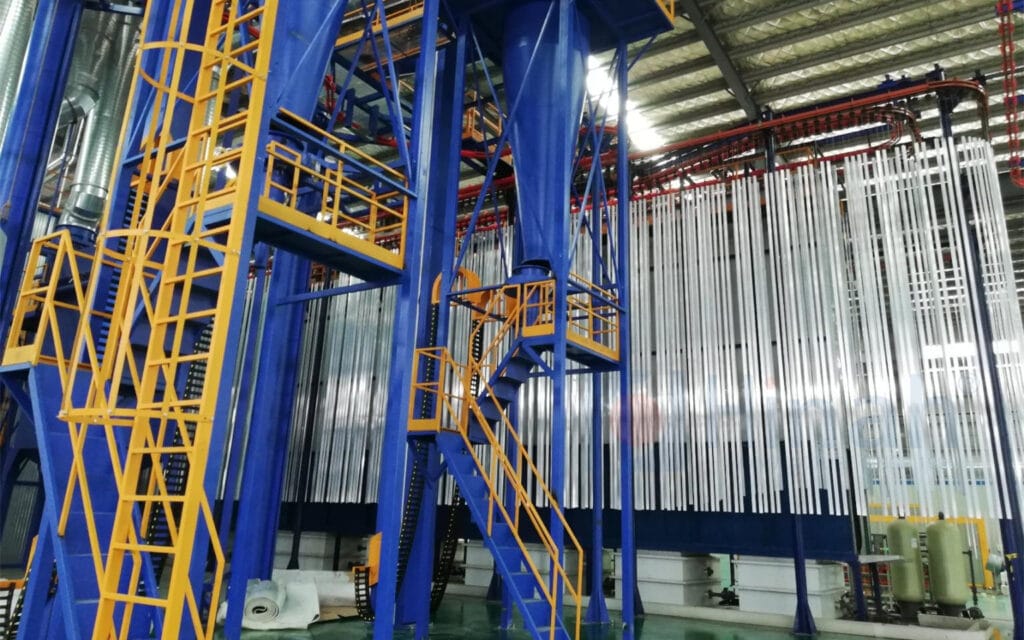
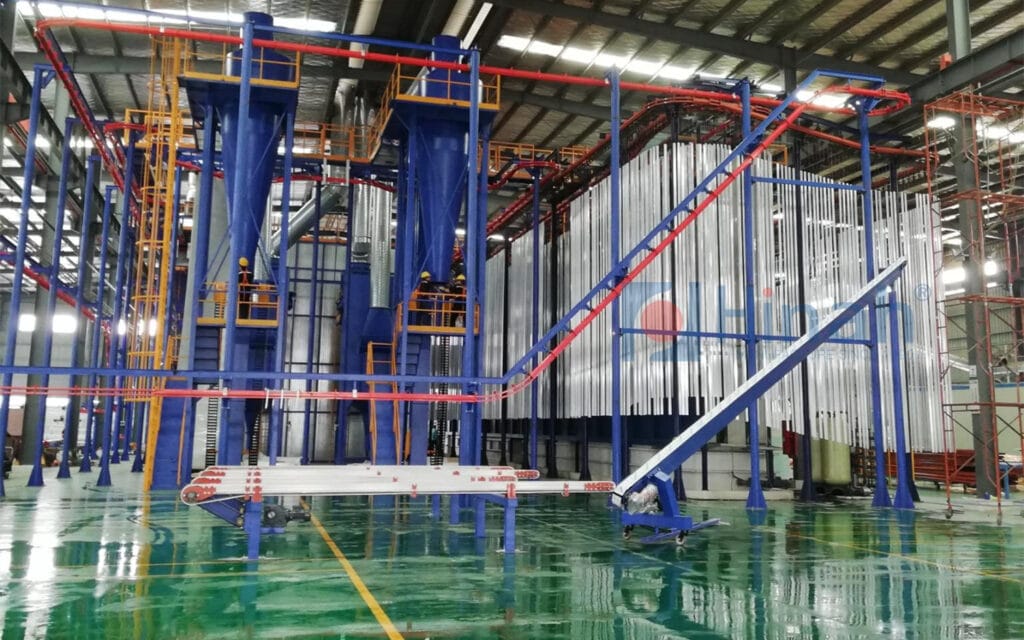
VI.Conclusion
Designing an efficient aluminum powder coating line requires comprehensive consideration of multiple factors such as layout, equipment, technology, and environmental protection to ensure production efficiency and product quality. At the same time, automation, intelligence, environmental protection and energy conservation will become future development trends, driving the industry to transform into a more efficient and green direction. Enterprises should continue to optimize the design of coating lines based on their own needs and market changes, and continuously improve their competitiveness to cope with increasingly fierce market competition.