Regular maintenance of your aluminium powder coating line is not just a routine task—it’s a critical driver of profitability and product quality. While often overlooked, neglecting upkeep can lead to costly downtime, inconsistent coating results, and accelerated equipment wear.
A well-maintained line ensures optimal adhesion, uniform finishes, and compliance with industry standards, directly impacting customer satisfaction. For instance, industry reports reveal that unplanned downtime due to equipment failure can cost manufacturers up to $10,000 per hour in lost productivity. Conversely, proactive maintenance reduces powder waste by up to 20% and extends machinery lifespan by 3-5 years.
In this article, we’ll share actionable strategies to keep your aluminium powder coating line operating at peak performance, from daily checks to troubleshooting.
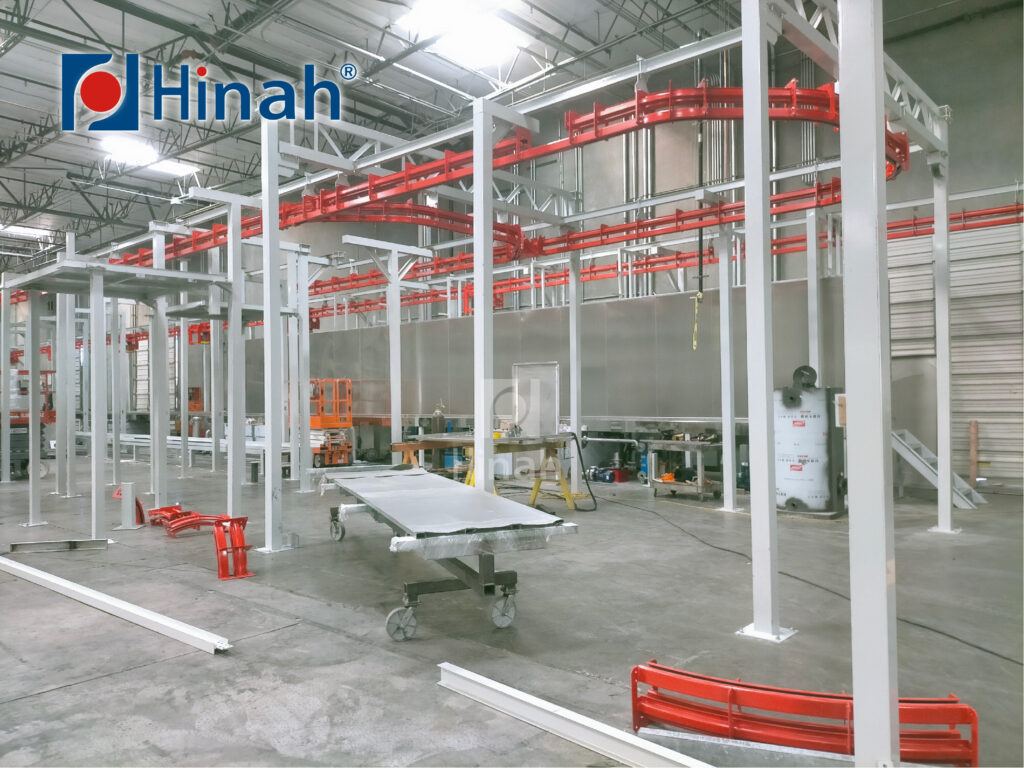
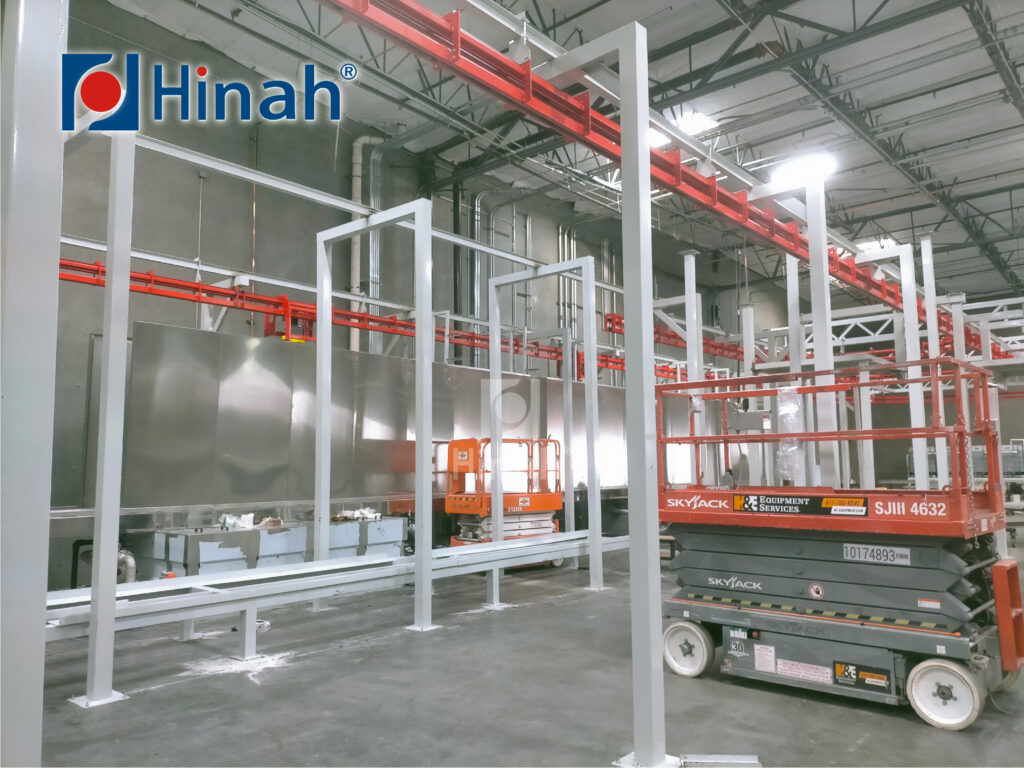
I. Daily Checklist for Aluminium Powder Coating Line
A consistent daily routine is vital to sustain the performance of your aluminium powder coating line. Below are three critical tasks to prioritize:
1. Spray Gun and Electrostatic Equipment Cleaning
Regular cleaning of spray guns and electrostatic components prevents clogs and contamination, which are common culprits of uneven powder distribution. Start by disassembling the spray guns and wiping them thoroughly with lint-free cloths to remove residual powder. Use compressed air to clear any buildup in electrostatic parts, paying close attention to nozzle tips, which should be inspected for wear and replaced if damaged. To avoid cross-contamination between powder colors, adopt a strict post-shift cleaning protocol. This simple habit minimizes defects like pinholes and ensures consistent adhesion across batches.
2. Conveyor Belt Inspection and Alignment
Misaligned conveyor belts disrupt workflow, leading to product jams or uneven coating. Begin by verifying belt tension and alignment using a laser level, adjusting rollers as needed to maintain precise positioning. Lubricate chains with high-temperature grease to reduce friction and extend component lifespan, while also clearing debris from tracks to prevent impurities from compromising coating quality. For quick visual checks during shifts, mark “ideal alignment” reference points directly on the conveyor frame. These steps help prevent premature wear and ensure smooth material handling.
3. Compressed Air System Testing
The quality of compressed air directly impacts coating integrity, as moisture or oil contamination can cause bubbling or poor adhesion. Daily maintenance involves draining water from air filters and verifying stable pressure levels within the recommended 4–6 bar range. Use a hygrometer to monitor humidity, ensuring it remains below 15% to avoid moisture-related defects. Immediately replace clogged filters and consider installing an inline desiccant dryer for long-term air purity control. By maintaining clean, dry air supplies, you safeguard the uniformity and durability of powder-coated finishes.
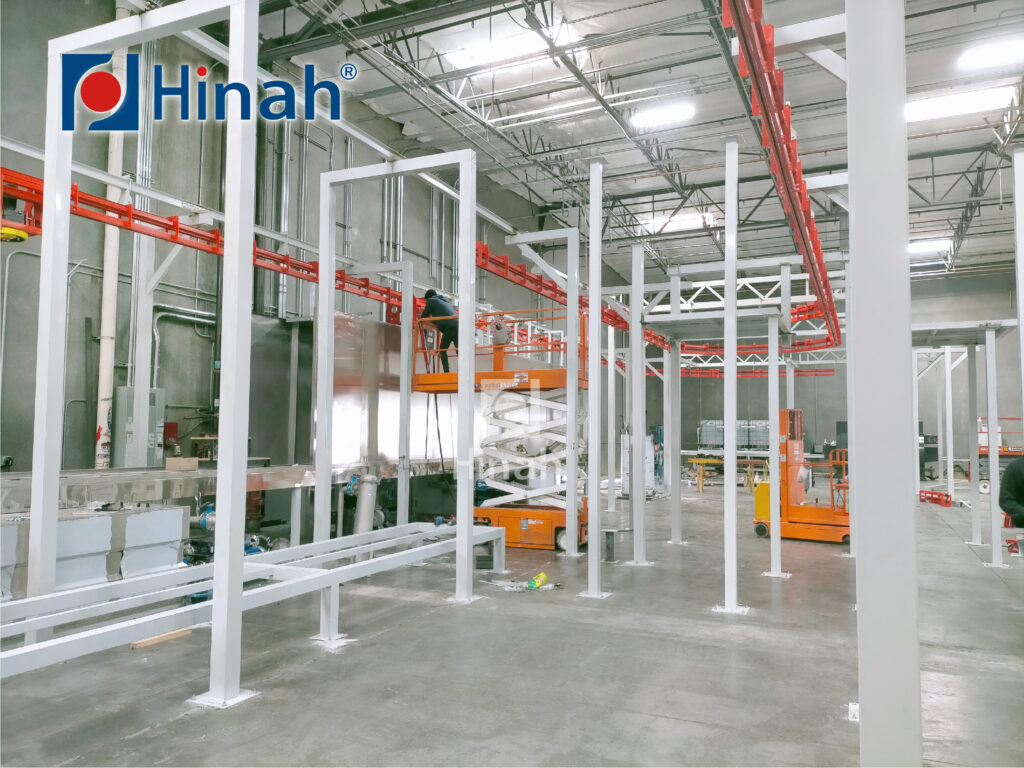
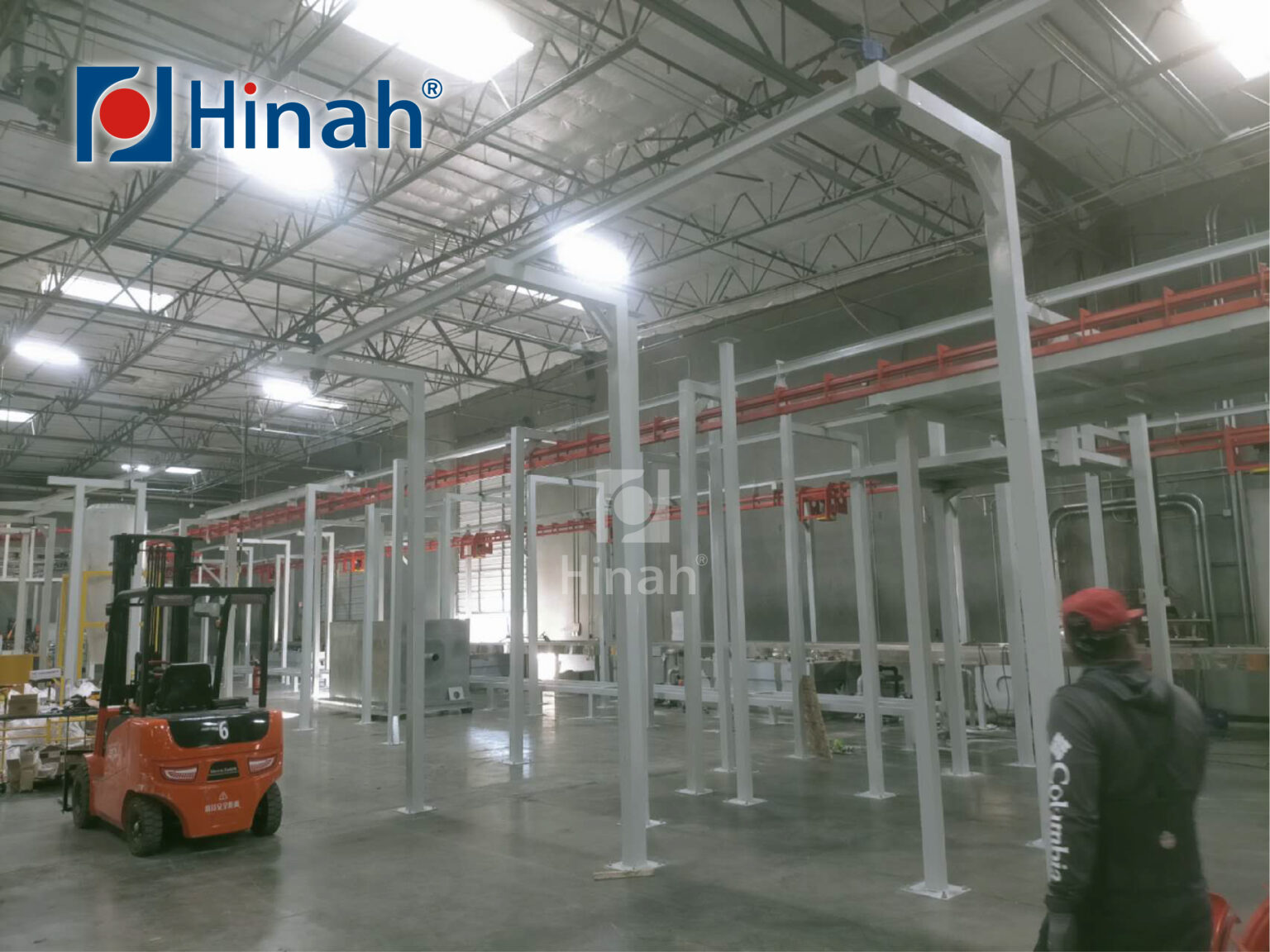
II. Preventive Maintenance for Aluminium Powder Coating Line
Proactive maintenance of key components in your aluminium powder coating line prevents unexpected breakdowns and ensures long-term operational efficiency.
Powder Coating Curing Oven
The curing oven is the backbone of your coating process, where improper temperature control leads to under-cured or burnt finishes. Schedule monthly inspections to verify temperature uniformity across all zones using a calibrated thermal sensor. Clean air circulation ducts and replace clogged filters to prevent hot spots, while inspecting heating elements for signs of corrosion or wear. For gas-powered ovens, check burner nozzles and gas pressure settings to maintain consistent heat distribution. Annual recalibration of the oven’s control system ensures compliance with manufacturer specifications, reducing energy waste and rework rates.
Powder Recovery System
A well-maintained recovery system maximizes powder reuse and minimizes waste. Weekly tasks involve emptying cyclone separators and cleaning filters with compressed air to prevent blockages that reduce suction power. Check hoses and ductwork for leaks, especially at joints, and apply silicone sealant if airflow drops below optimal levels. For cartridge-based recovery units, monitor pressure differential gauges and replace cartridges when resistance exceeds 20% of the baseline. Annually, disassemble and lubricate the system’s fan motor bearings to prevent overheating, and recalibrate the powder-to-air ratio for efficient recycling.
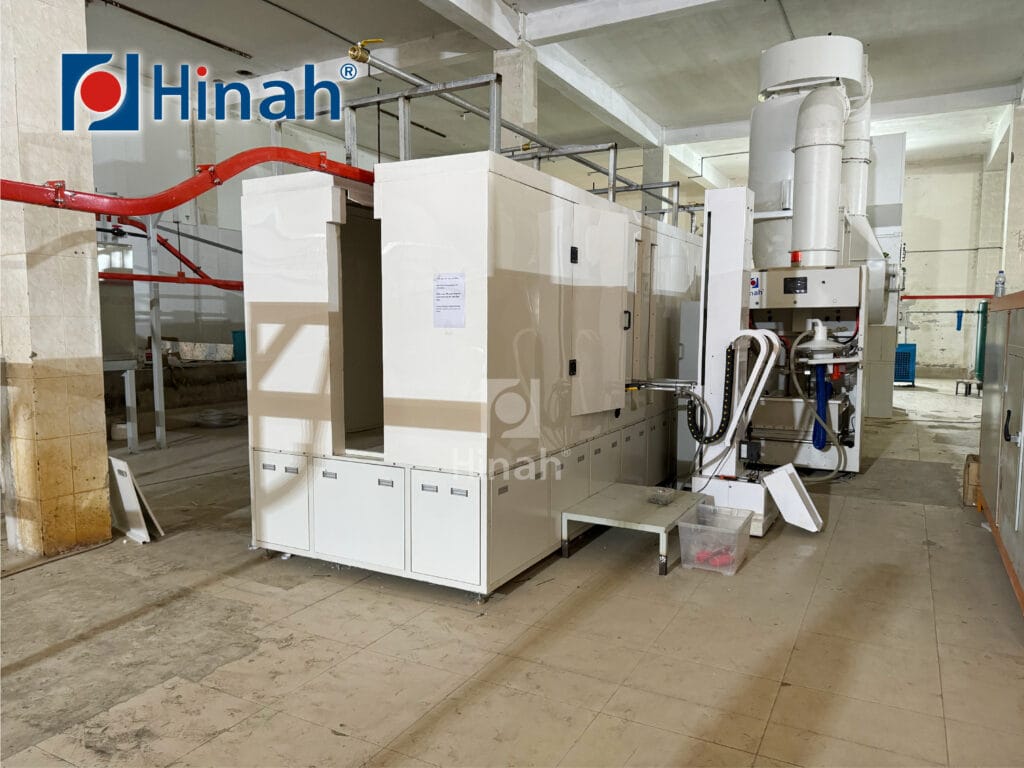
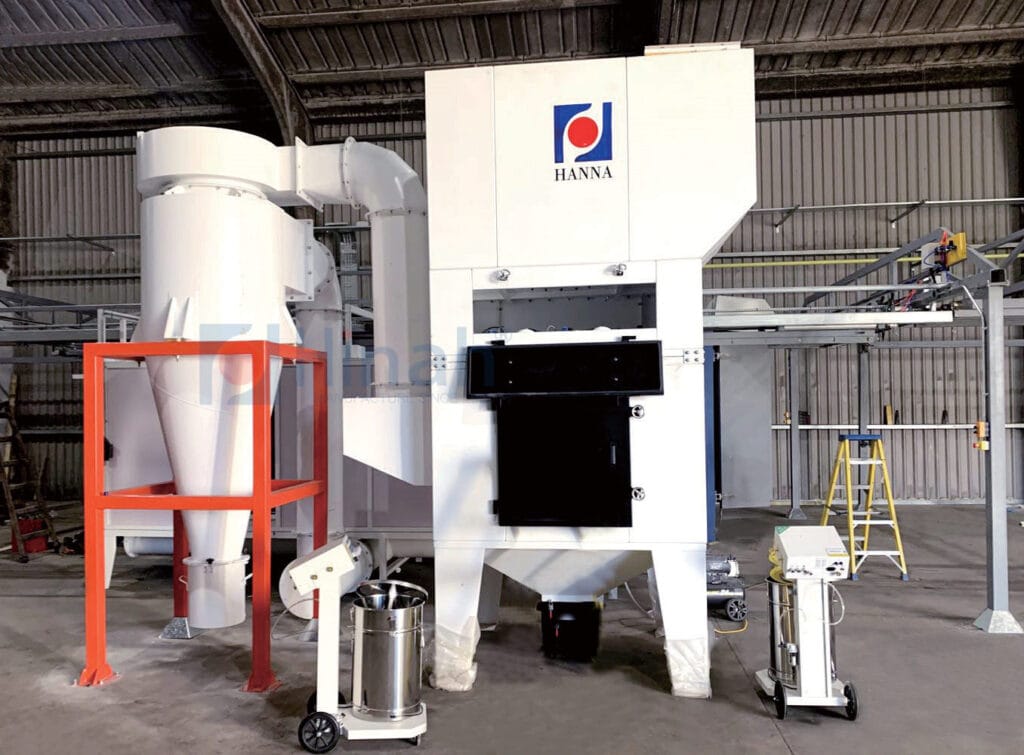
III. Troubleshooting Aluminium Powder Coating Line Issues
Even well-maintained aluminium powder coating lines occasionally encounter challenges. Addressing the three most common defects—orange peel texture, powder adhesion failure, and curing defects—requires a systematic approach. Below are actionable solutions to restore coating quality and minimize downtime.
Orange Peel Texture
What it looks like: A bumpy, uneven surface resembling orange skin (include a side-by-side image of defective vs. smooth coating).
Root causes:
– Incorrect spray gun distance (too far or too close to the substrate).
– Inadequate fluidization of powder in the hopper.
– Fast curing oven temperature ramping, causing premature surface hardening.
Solutions:
Adjust the spray gun to maintain a consistent distance of 15–30 cm from the aluminium profile, depending on powder type. Ensure proper fluidization by checking the fluidizing air pressure (recommended: 0.1–0.3 bar) and sieve the powder to remove clumps. For curing-related orange peel, slow the oven’s temperature ramp rate to 5–10°C per minute to allow even flow before cross-linking.
Powder Adhesion Failure
What it looks like: Powder flakes off easily during handling or testing.
Root causes:
– Poor substrate preparation (e.g., residual oils, oxides, or phosphating layer defects).
– Insufficient electrostatic charge due to faulty grounding or low generator voltage.
– Humidity levels exceeding 65%, causing moisture contamination.
Solutions:
Reinforce pre-treatment protocols: degrease profiles with alkaline cleaners, rinse thoroughly, and ensure phosphating baths are within pH 3.5–4.5. Verify grounding continuity by testing resistance (<1 megaohm) between the conveyor chain and earth. Increase electrostatic generator voltage to 70–90 kV for complex geometries. Install dehumidifiers in the coating booth if ambient humidity rises.
Poor Curing (Under/Over-Cured Coatings)
What it looks like: Under-cured coatings feel sticky or fail scratch tests; over-cured coatings appear brittle or discolored.
Root causes:
– Inaccurate oven temperature profiles (e.g., hot/cold zones).
– Incorrect dwell time for the powder’s cure schedule.
– Blocked airflow ducts or malfunctioning exhaust fans.
Solutions:
Adjust conveyor speed to meet the powder manufacturer’s specified dwell time (e.g., 10–15 minutes at 180–200°C). Clean airflow ducts and replace damaged fan blades to restore uniform heat distribution. For gas ovens, calibrate burners to ensure stoichiometric combustion.
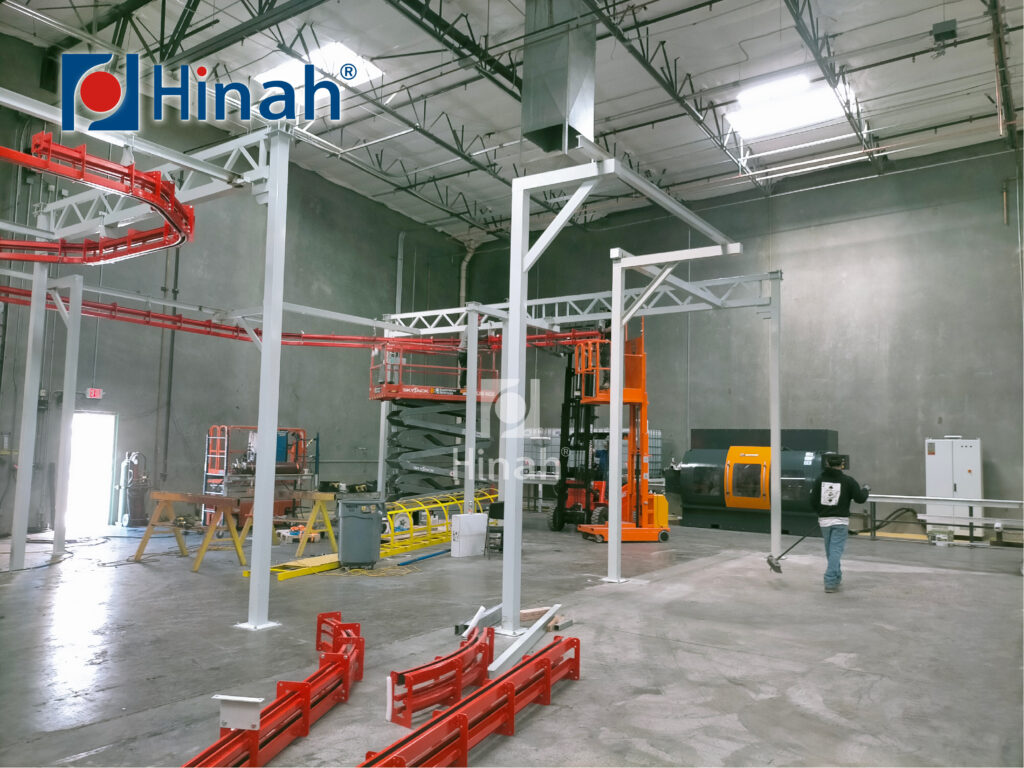
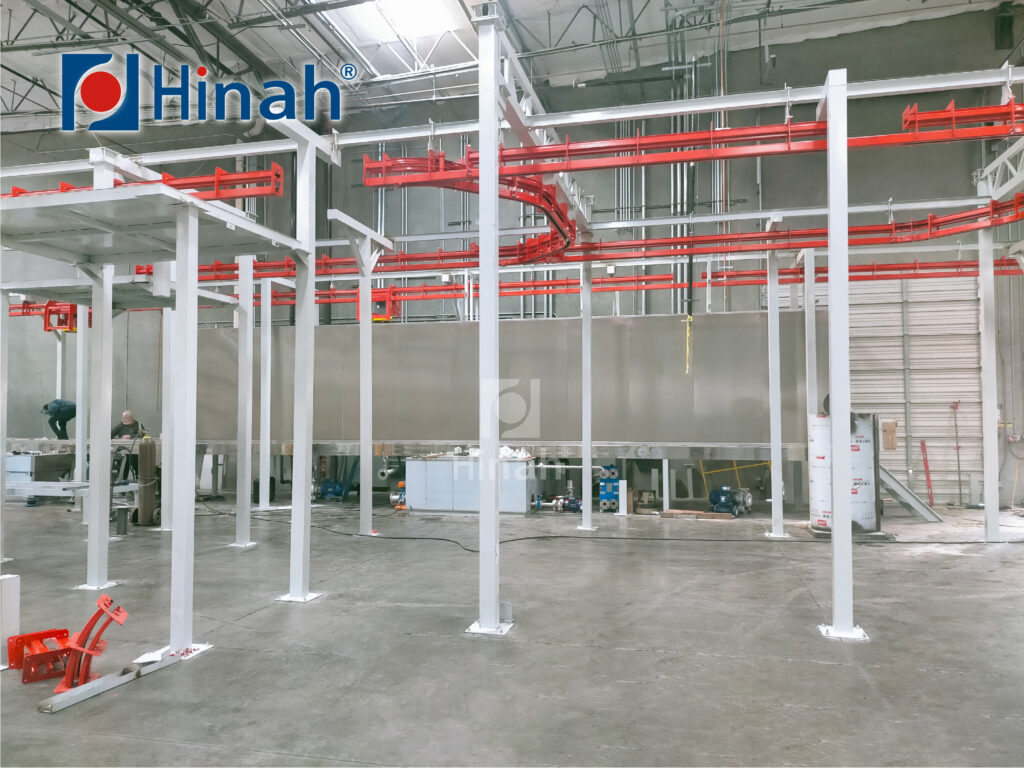
Conclusion
A high-performing aluminium powder coating line is not merely a result of advanced technology—it thrives on disciplined maintenance and swift problem-solving. By integrating daily checks, preventive strategies, and targeted troubleshooting into your workflow, you can transform operational challenges into opportunities for efficiency gains.
The true measure of success lies in long-term reliability. By prioritizing these practices, your coating line will deliver durable, visually flawless finishes that meet stringent industry standards, while keeping operational costs predictable.
Ready to elevate your powder coating line’s performance? Schedule a consultation with our engineers to tailor these strategies to your facility’s unique needs.