In the modern industrial coating process, powder coating technology is widely used because of its high efficiency, environmental protection and superior coating quality. The powder coating conveyor, as a core component of the spraying production line, plays an important role. It not only directly affects the efficiency and quality of the coating operation, but is also closely related to the overall performance and cost of the production line. Choosing a suitable powder coating conveyor system can effectively improve production efficiency, reduce material waste, and reduce maintenance costs, thereby ensuring the competitiveness of products in the market. However, among the many different types and configurations of powder coating conveyor systems, how to make a suitable choice has become a challenge faced by many manufacturers.
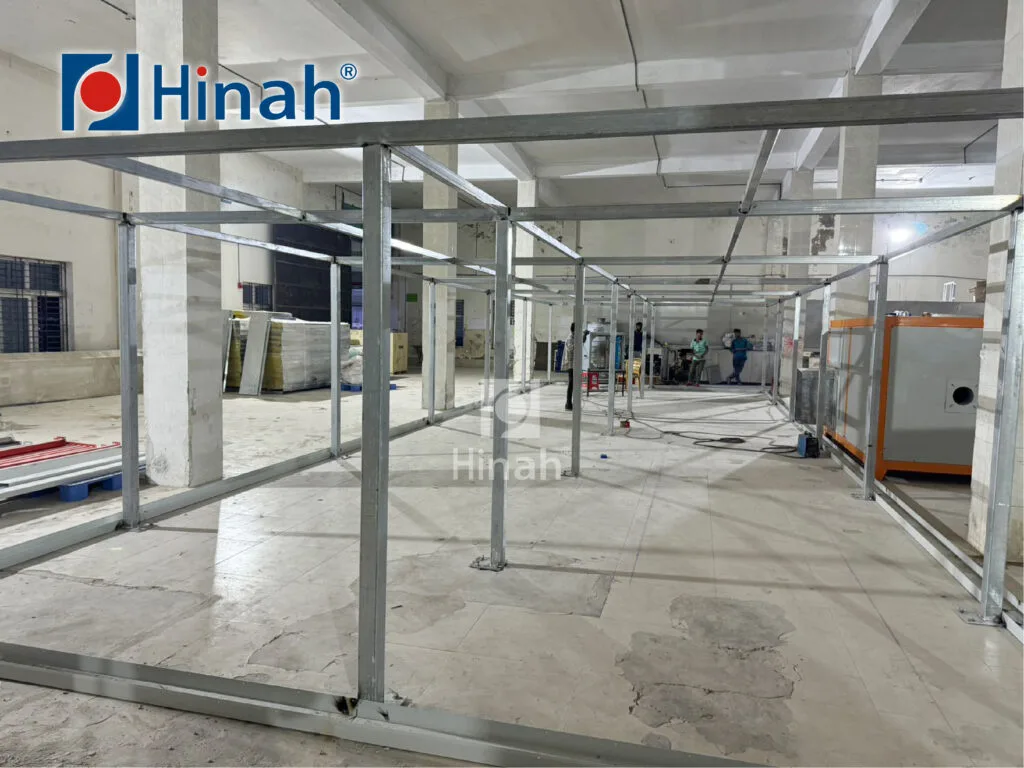
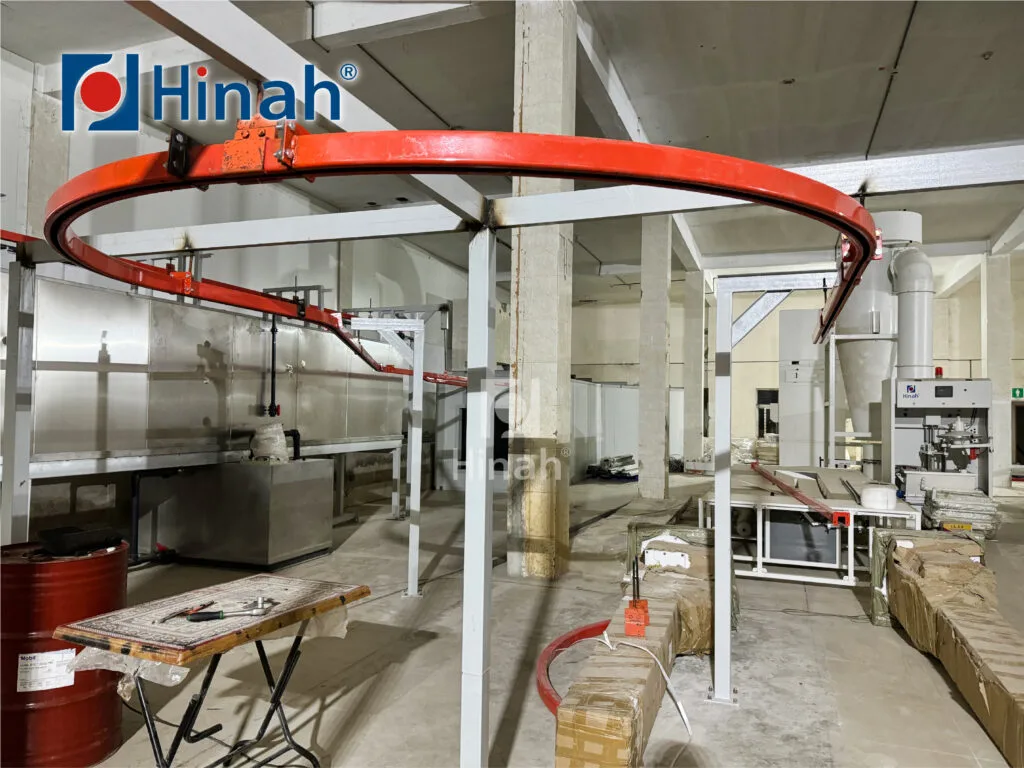
I. Analysis of core components of powder coating conveyor
The efficient operation of powder coating conveyor system depends on the coordinated work of multiple core components. Understanding the role and characteristics of each key part will help make wise decisions when choosing.
1. Drive system
The drive system is the power source of the powder coating conveyor system, which usually includes motors, transmission devices and power control systems. It is responsible for providing sufficient power to transfer powder to the designated target area through the conveyor. The selection of the drive system should consider its power, efficiency and adaptability to ensure that the system can operate stably and efficiently, and can still ensure stable production under high load conditions.
2. Conveyor structure
The conveyor structure is the skeleton of the powder coating conveyor system, which is usually composed of conveyor belts, rollers, chains, etc. Its function is to transport workpieces or powder coatings from one work area to another. Different types of conveyor structures are suitable for different production needs, such as pneumatic conveyors are suitable for high-speed production, and mechanical conveyors are more suitable for production lines that need to carry heavier workpieces.
3. Workpiece fixture
The workpiece fixture is used to fix the workpiece to be coated on the conveyor system to ensure that it will not be offset or damaged during the conveying process. Common workpiece fixing devices include fixtures, hooks, brackets, etc.
4. Control system
The control system is the “brain” of the powder coating conveyor system, responsible for coordinating the operation of various parts. It includes automated control panels, sensors, feedback systems, etc., which monitor the parameters of the conveying process in real time to ensure that the system operates efficiently according to the set standards. Modern control systems usually have intelligent functions, which can improve the flexibility and convenience of operation through program settings, remote operations, etc.
5. Conveyor mechanism
The conveyor mechanism refers to all physical components in the conveying system, including conveyor belts, chains, air flow channels, etc., which are responsible for realizing the movement of materials or workpieces. Depending on different process requirements, the conveyor mechanism is sometimes equipped with additional functions such as heating, cooling or drying to ensure uniform coating of the paint or optimal treatment of the workpiece.
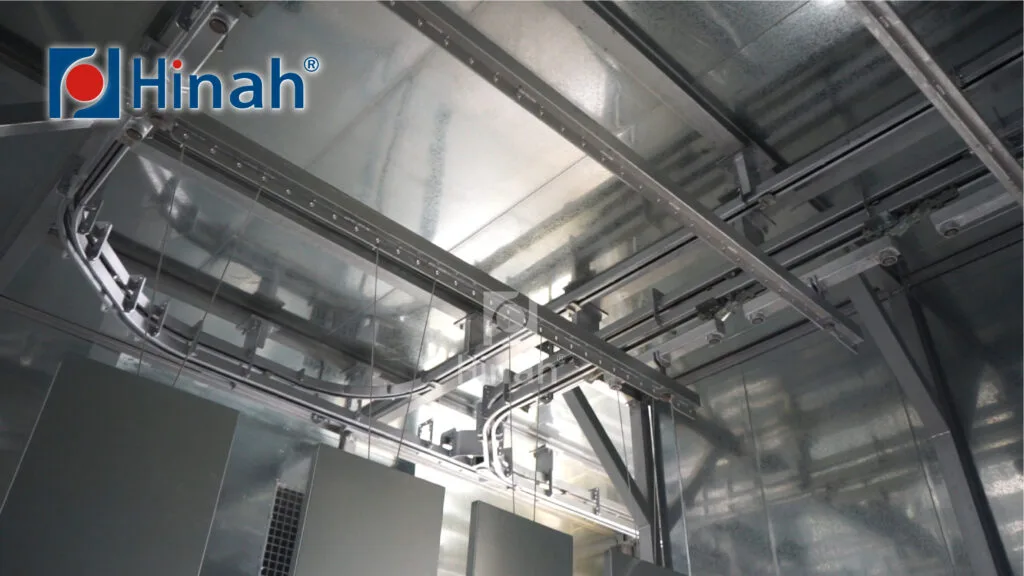
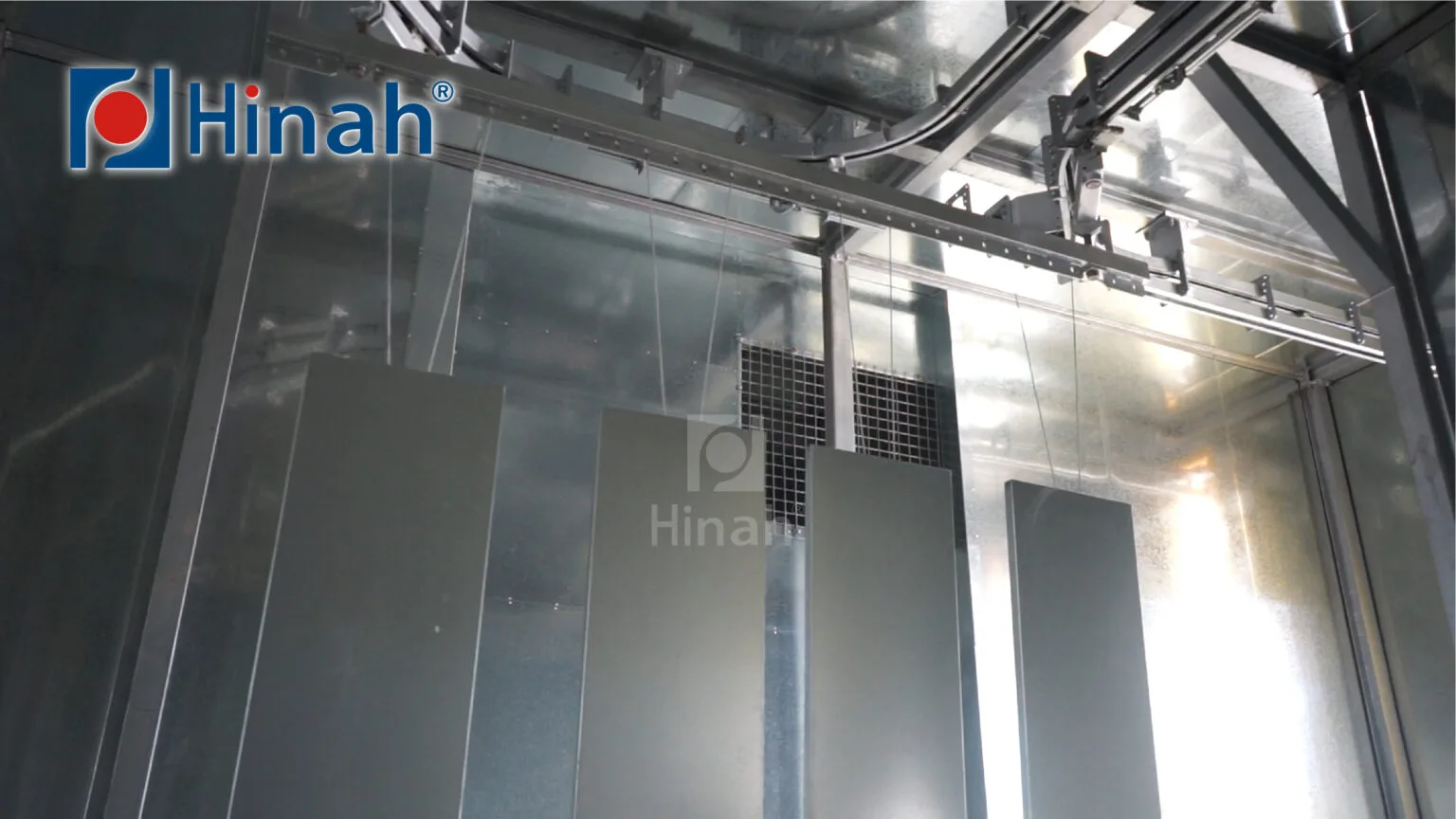
II. Comparison of different types of powder coating conveyor systems
When choosing a powder coating conveyor, it is important to understand the different types of systems and their characteristics. The following is a comparison of several common types of powder coating conveyor systems:
1. Automatic conveyor system
Automatic conveyor systems usually use motorized belt or roller conveyors that move at a predetermined speed to accurately and reliably transport workpieces from one station to the next. The advantages of this system are high efficiency, stability, and the ability to achieve large-scale production and reduce human intervention. Automatic conveying systems can ensure stable throughput of the production line, and through automated control, manual operations can be minimized, reducing labor costs. Suitable for efficient, high-capacity production environments, especially in situations where there are strict requirements for production speed and consistency.
2. Power and free conveyor system
The power and free conveyor system consists of a track-type conveyor chain with a powered trolley (power chain) and an auxiliary load-bearing trolley (free trolley) running along an elevated track. A key feature of this configuration is that the workpiece carrier can move independently along the track, which allows the system to achieve selective start and stop functions and asynchronous operation. Power and free conveyor systems are well suited for complex coating processes with multiple stages or different cycle times. It can flexibly adjust the work rhythm and improve the diversity and flexibility of the production line, especially when different process stages need to operate independently.
3. Vertical lifting conveyor system
Vertical lifting conveyor is used to transfer workpieces between workstations at different heights in multi-layer automatic coating lines. This equipment is usually used in production lines with limited space to optimize space utilization by moving workpieces vertically. It is particularly suitable for large or high-capacity production lines.
4. Air conveyor system
The air conveyor system mainly relies on air flow to transport powder coating to the spraying area and is often used for the transportation and recovery of powder coating. The advantages of this system are efficient material flow and less mechanical wear, which can increase the service life of the system and reduce maintenance costs. The air conveyor system is suitable for materials that are not easily contaminated or fragile by paint, and can be efficiently transferred between different workstations.
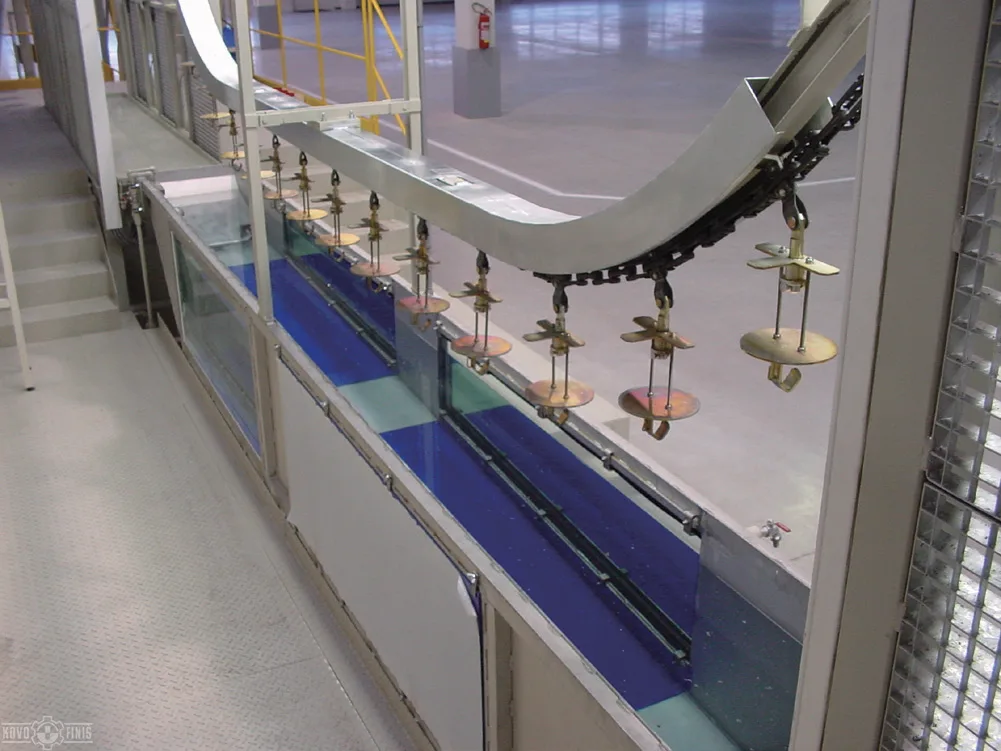
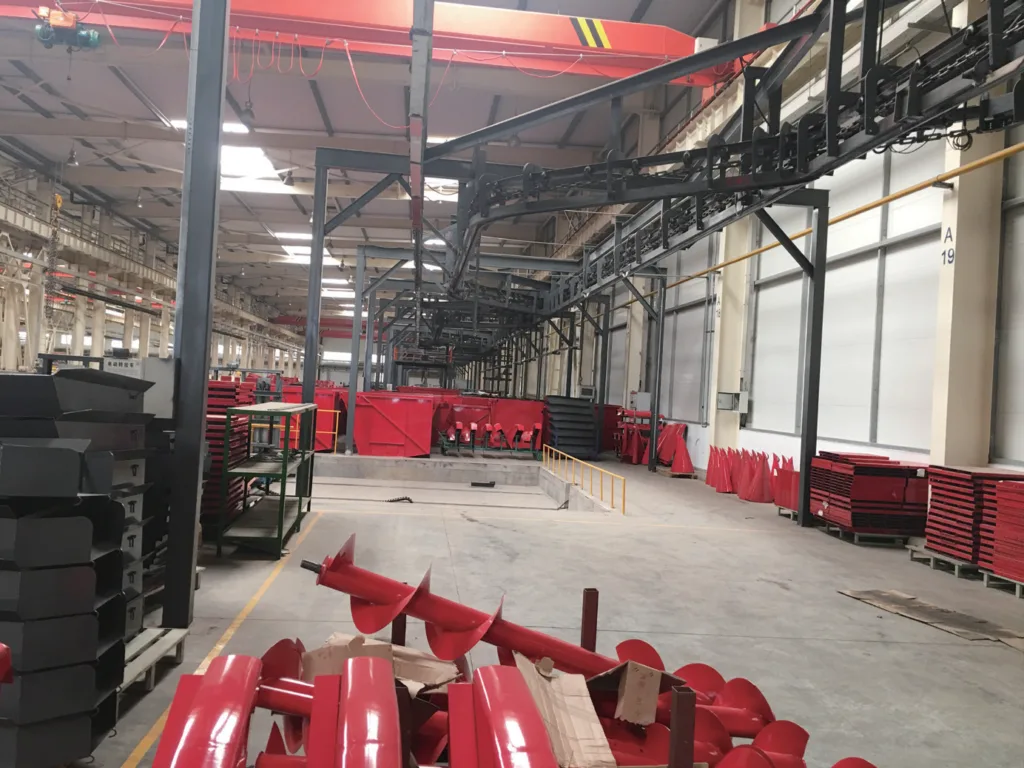
III. How to choose a suitable powder coating conveyor system?
Choosing a suitable powder coating conveyor is not only related to the performance of the equipment, but also directly affects production efficiency and cost. The following are several key factors to consider when choosing:
- Production scale
Depending on the scale of production, the selection of powder coating conveyor is also different. If it is a small batch production, you may prefer a small conveyor system with higher flexibility, while large-scale production requires a system with higher processing capacity. Large-scale production also requires equipment to have high durability and long-term stability.
- Production environment
Different production environments have different requirements for conveyor systems. For example, high temperature or humid environment may affect the performance of the conveyor system, so it is necessary to choose corrosion-resistant and high-temperature resistant materials. It is also necessary to consider the cleanliness of the environment to avoid contamination by powder or other materials, which in turn affects production quality.
- Cost budget
The cost budget is an important factor in deciding which powder coating conveyor system to choose. Although high-end systems generally have better performance and longer service life, their initial investment is higher. If the budget is limited, you can choose a mid-to-low-end system with a higher cost performance, or consider upgrading gradually.
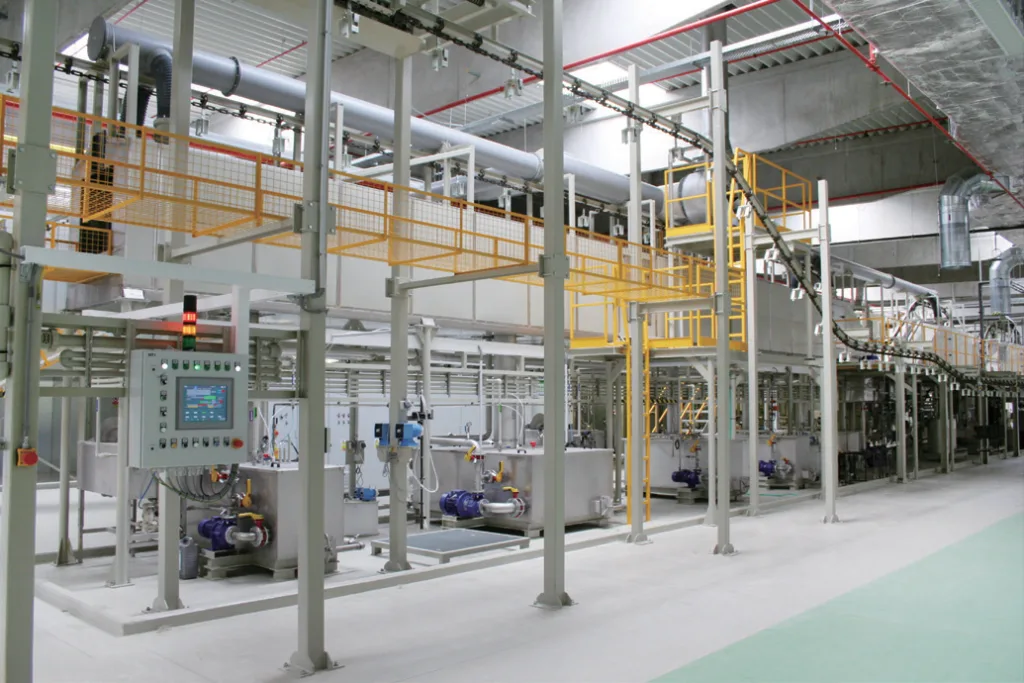
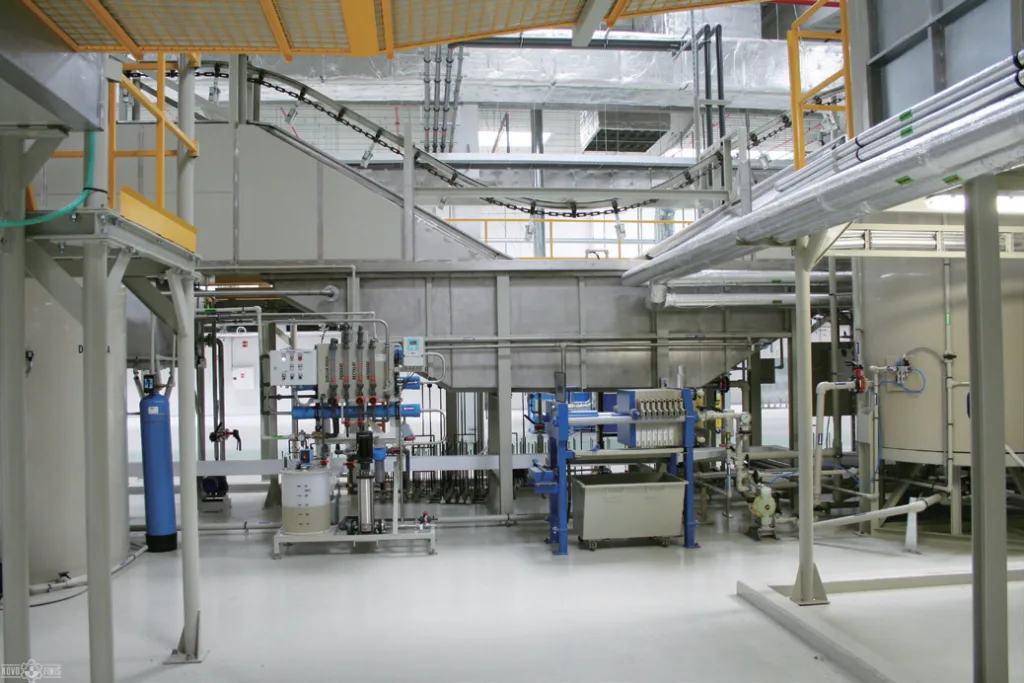
Conclusion
Choosing the right powder coating conveyor system is essential to ensure production efficiency, reduce costs, and improve spray quality. First, choosing a well-designed and sturdy system will greatly improve the operating efficiency of the production line and avoid production delays or quality fluctuations caused by equipment problems. Second, different types of powder coating conveyor systems have their own advantages and limitations. It is important to make decisions based on the characteristics of your own production line, the required delivery efficiency, and the specific challenges you face. In addition, the maintenance requirements of the equipment, the energy efficiency level, and the adaptability of the spatial layout should also be considered.
The selection of a powder coating conveyor system is a comprehensive decision that requires a balance between equipment performance, economy, and production needs. By understanding the characteristics of various system types and combining them with actual production needs, you can choose the most suitable solution to ensure the stability and efficiency of the powder coating process and further enhance the competitiveness of your company.