In today’s fast-paced manufacturing world, efficiency isn’t just a bonus—it’s essential. Every step in the production line matters, and when it comes to surface finishing, powder coating remains one of the most trusted methods for achieving durability, precision, and environmental compliance. But here’s the catch—not all powder coating lines are created equal.
For many manufacturers, especially those dealing with large, heavy, or uniquely shaped components, traditional vertical lines often present more challenges than solutions. That’s where the horizontal powder coating line steps in—not just as an alternative, but as a smarter, more flexible system designed to meet real industrial demands.
From improving material handling to enhancing coating consistency, horizontal setups are quietly transforming factories around the world. If you’re wondering how to boost your productivity while keeping costs and downtime under control, it might be time to take a closer look.
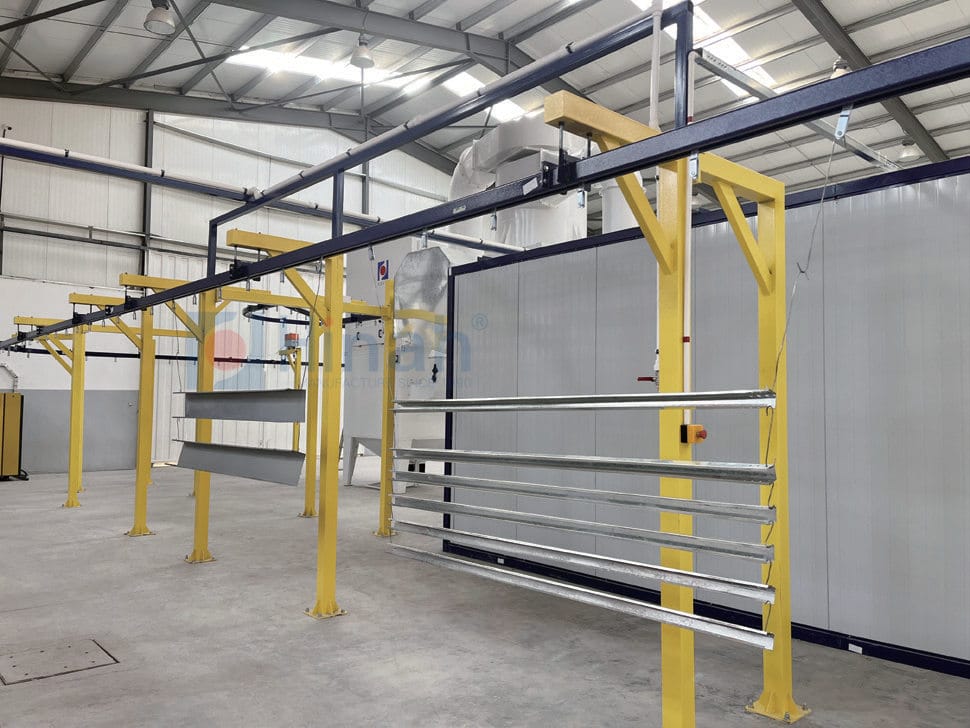
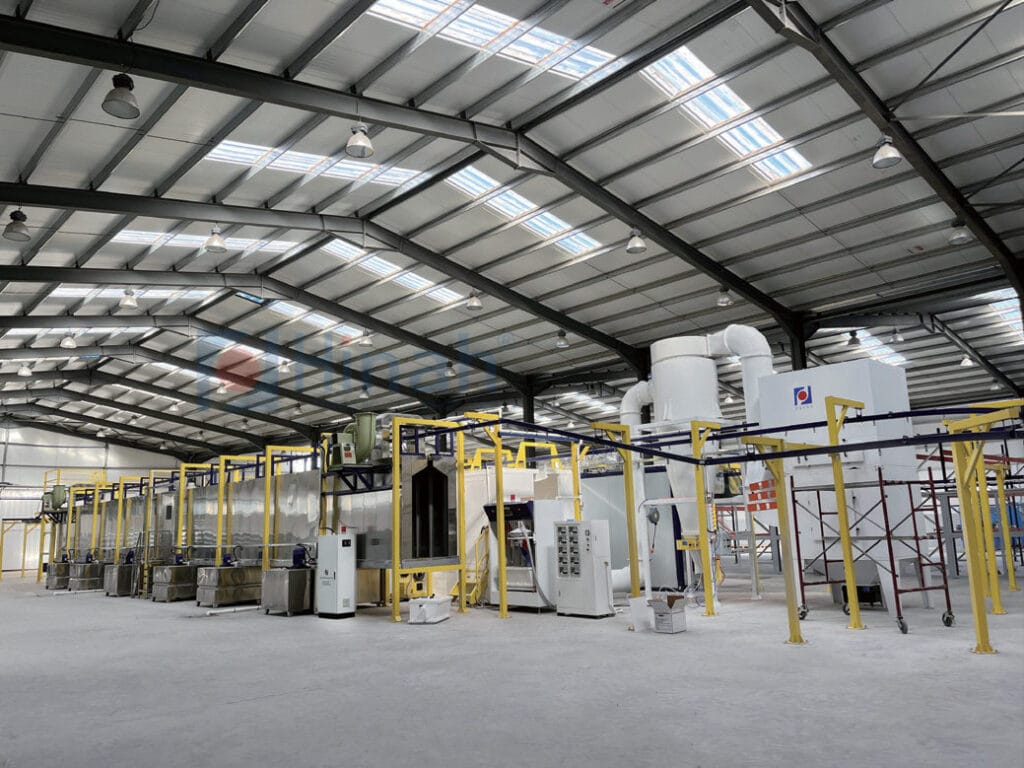
I. Consistent Coating Quality with Horizontal Powder Coating Line
In powder coating line, quality isn’t something you leave to chance. Your clients rely on you to deliver finishes that are not only visually flawless but also durable and long-lasting. A horizontal powder coating line helps you meet that expectation with confidence.
1. Better Control Over Coating Uniformity
One of the biggest advantages of a horizontal layout is stability. Parts remain level during the entire process, reducing the risk of uneven powder distribution, drips, or missed spots. Whether using manual spray guns or automated systems, the consistent positioning makes it easier to achieve an even finish across every surface.
2. Easier Access to All Surface Areas
Complex geometries are common in industrial parts, and proper coverage can be challenging. With a horizontal setup, spray equipment can reach deep corners and contours more effectively. The clear, open positioning allows operators—or robotic arms—to coat components with greater precision.
3. Cleaner Application Environment
Horizontal powder coating lines are typically designed with optimized airflow and booth control. This means less turbulence, reduced overspray, and minimal contamination. As a result, you get smoother finishes and fewer defects, which directly translates into higher product quality and lower rework rates.
4. Repeatable Results, Every Time
By minimizing variables like shifting parts or inconsistent gun angles, the horizontal system supports a more repeatable process. Whether it’s the first part of the day or the last one before shutdown, you can trust the results to be just as consistent.
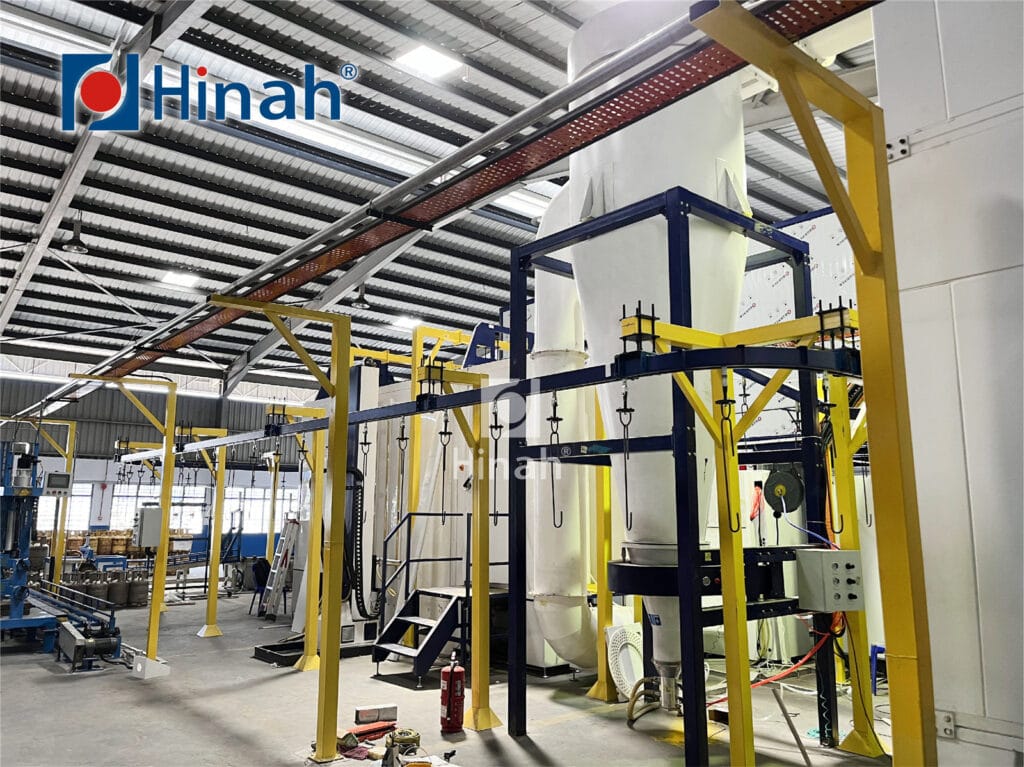
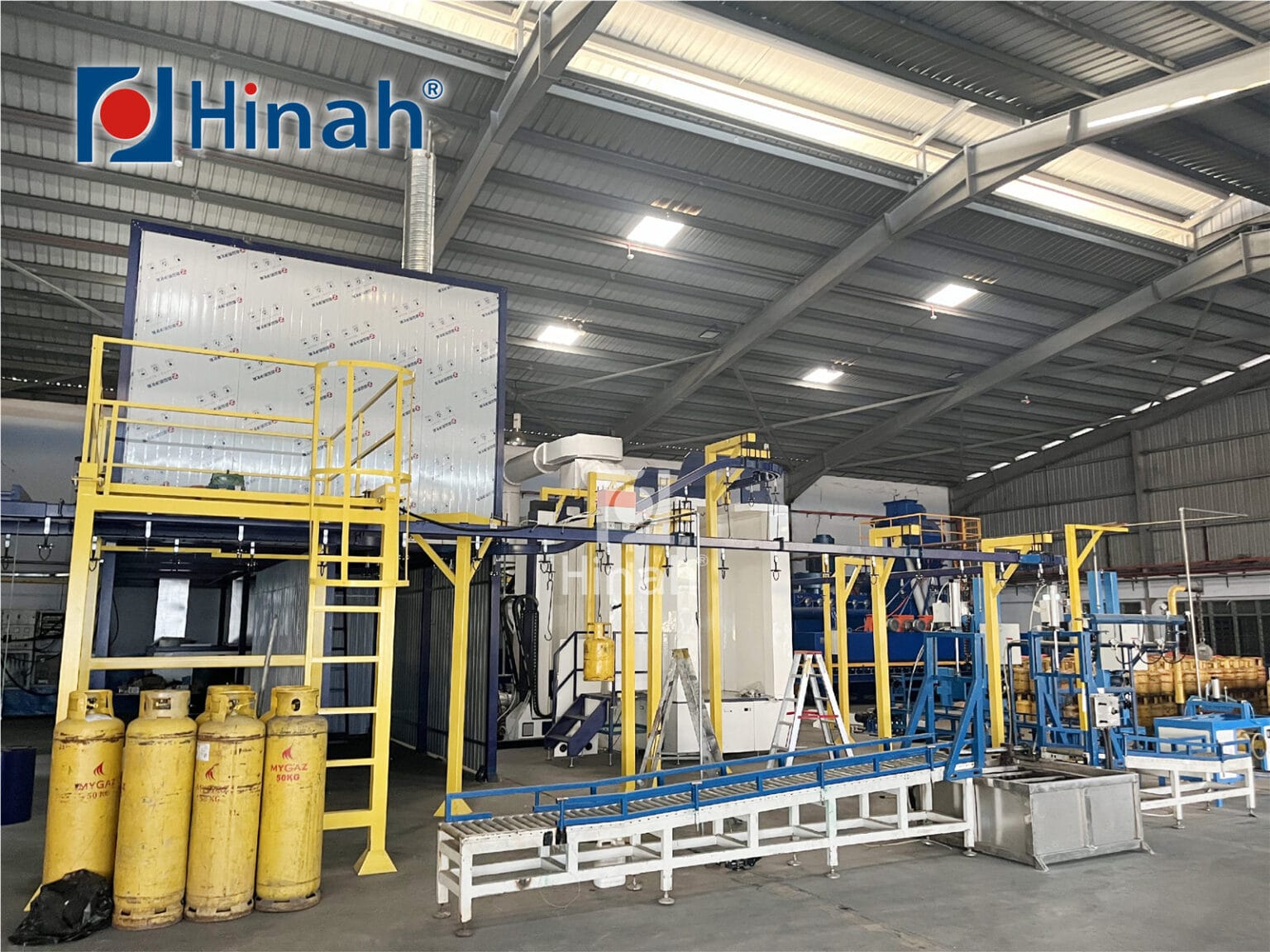
II. Improved Workflow and Material Handling Efficiency
Imagine this: it’s 8 a.m., your production line is just kicking off, and parts are already moving smoothly through each stage—pre-treatment, spraying, curing—without a single hiccup. No scrambling, no lifting parts onto awkward hooks, no delays. That’s the kind of flow a horizontal powder coating line is built to support.
Instead of constantly working against the setup, your team works with it. Parts are loaded at ground level, minimizing strain and making the job safer and faster. No overhead lifts, no climbing ladders—just a simple, intuitive flow from start to finish.
And because the layout follows a clear, horizontal path, materials don’t double back or zigzag through the facility. Each station connects naturally to the next, and your conveyor keeps everything moving in rhythm. No one’s standing around waiting for parts to catch up, and no time is wasted fixing preventable snags.
Even better? When changes come—new part sizes, new coatings, higher volumes—you can adjust. Horizontal systems give you the flexibility to tweak speeds, add inspection points, or shift layouts with minimal disruption. That kind of adaptability matters when the market moves fast and customer demands change even faster.
At the heart of it all, a horizontal powder coating line is not just equipment—it’s a workflow enabler. It keeps your operation smooth, your team efficient, and your productivity exactly where you need it to be.
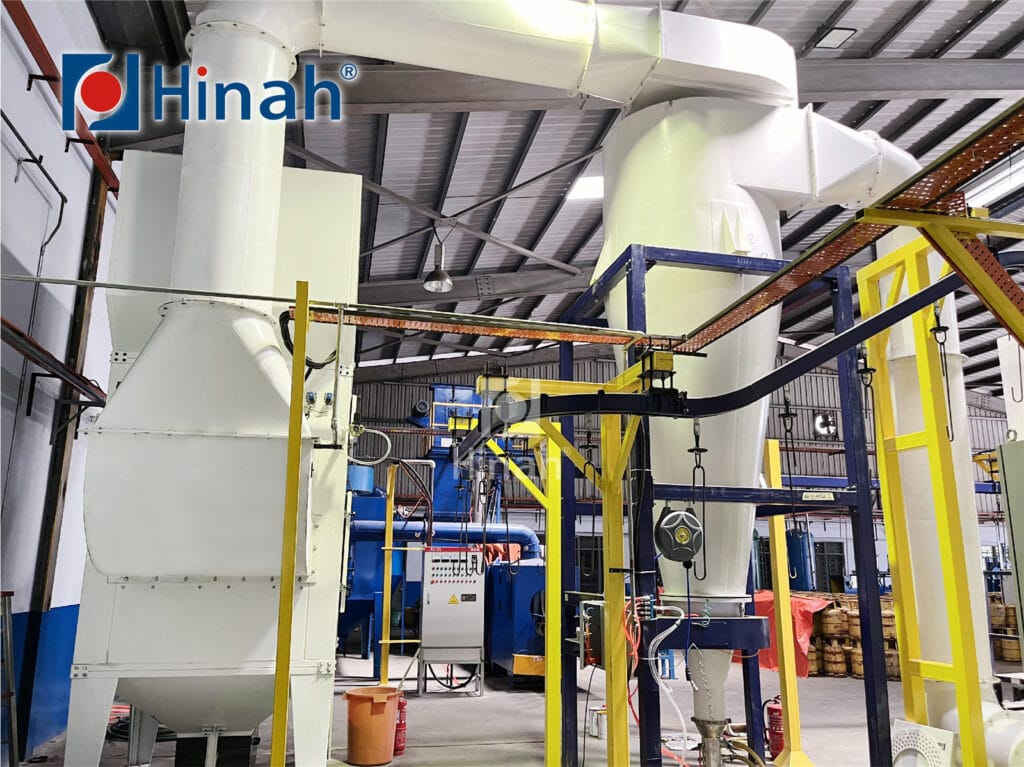
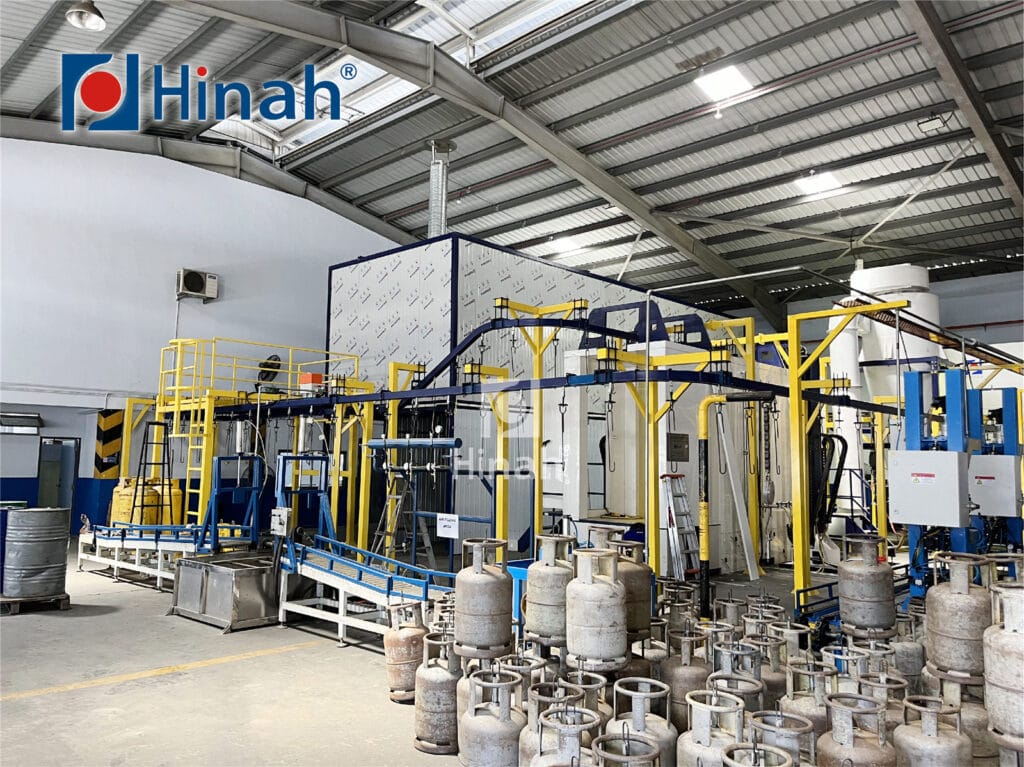
III. Reduced Downtime and Maintenance Costs
Downtime doesn’t just slow things down—it eats into your deadlines, your profits, and sometimes even your client relationships. Every hour a line isn’t running is an hour of lost opportunity. That’s why more manufacturers are turning to horizontal powder coating lines—because reliability matters just as much as performance.
- Fewer Moving Parts, Fewer Headaches
Horizontal lines are typically simpler in structure compared to complex vertical systems. Fewer lifts, fewer height adjustments, and less strain on mechanical components means fewer chances of something breaking. This reduces the need for emergency stops and gives your team more peace of mind during daily operations.
- Easier Access for Maintenance Crews
When something does need attention, accessibility makes a big difference. Technicians can easily inspect, clean, and repair components on a horizontal line without needing ladders or scaffolding. That means maintenance is faster, safer, and less disruptive to the workflow.
- Predictable, Lower Maintenance Costs
Because the system runs more smoothly and parts wear out more slowly, your maintenance schedule becomes more predictable. You’re not constantly reacting to issues—you’re staying ahead of them. That kind of control helps you avoid surprise expenses and better plan your production cycles.
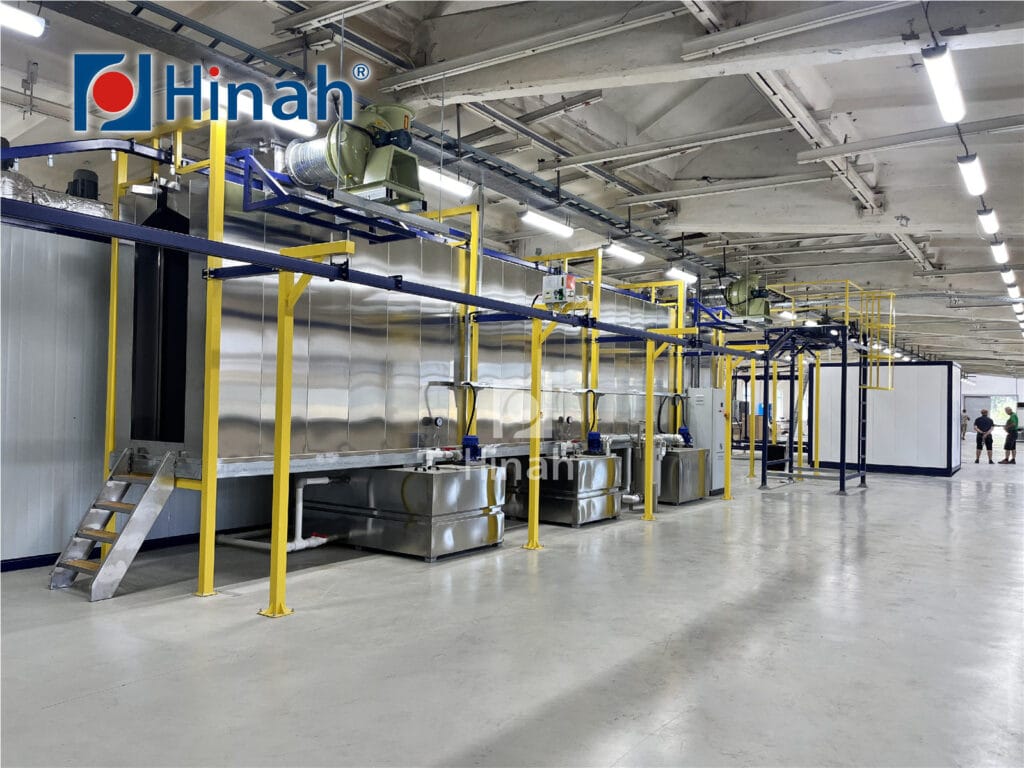
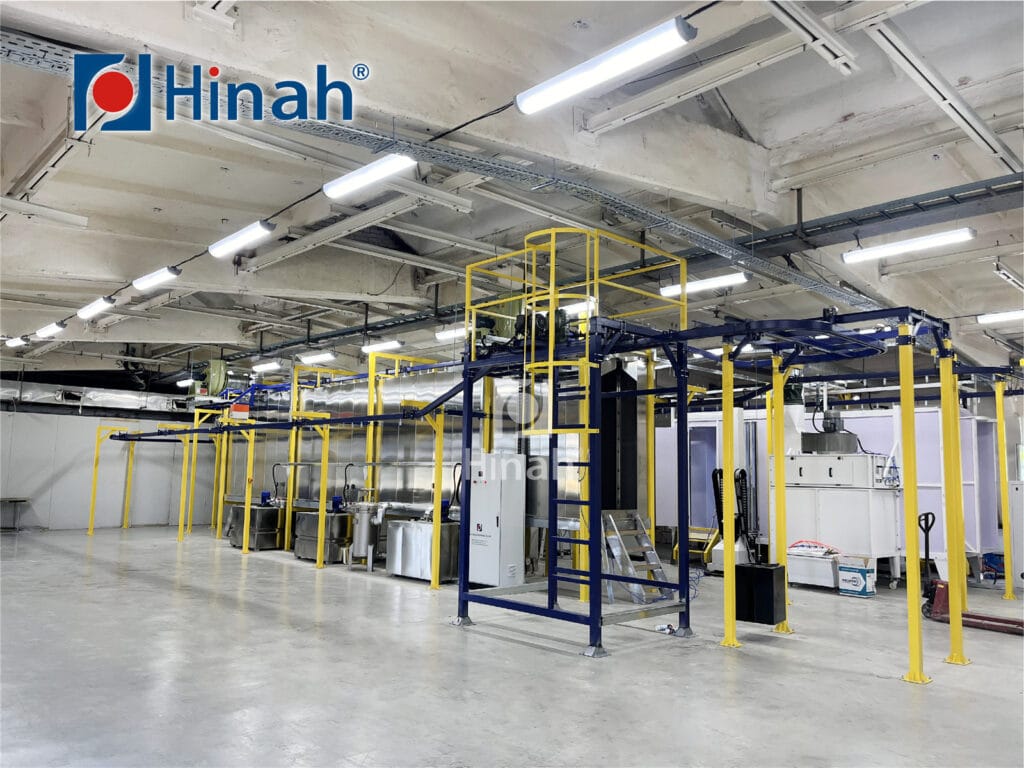
IV. Space Optimization for Industrial Facilities
Let’s be honest—not every facility was built with powder coating in mind. Space is always at a premium, and sometimes you’re trying to fit a new line into a layout that’s already packed. That’s where the flexibility of a horizontal powder coating line really shines.
These systems can be custom-built to fit the space you do have—not the space you wish you had. Whether it’s a narrow corridor or a production hall that needs to multitask, the layout can curve, stretch, or compress to suit your real-world constraints.
And if you’re integrating it into an existing line? No problem. Horizontal lines play well with others—they can be positioned alongside other processes without throwing off your production rhythm. It’s efficiency that fits.
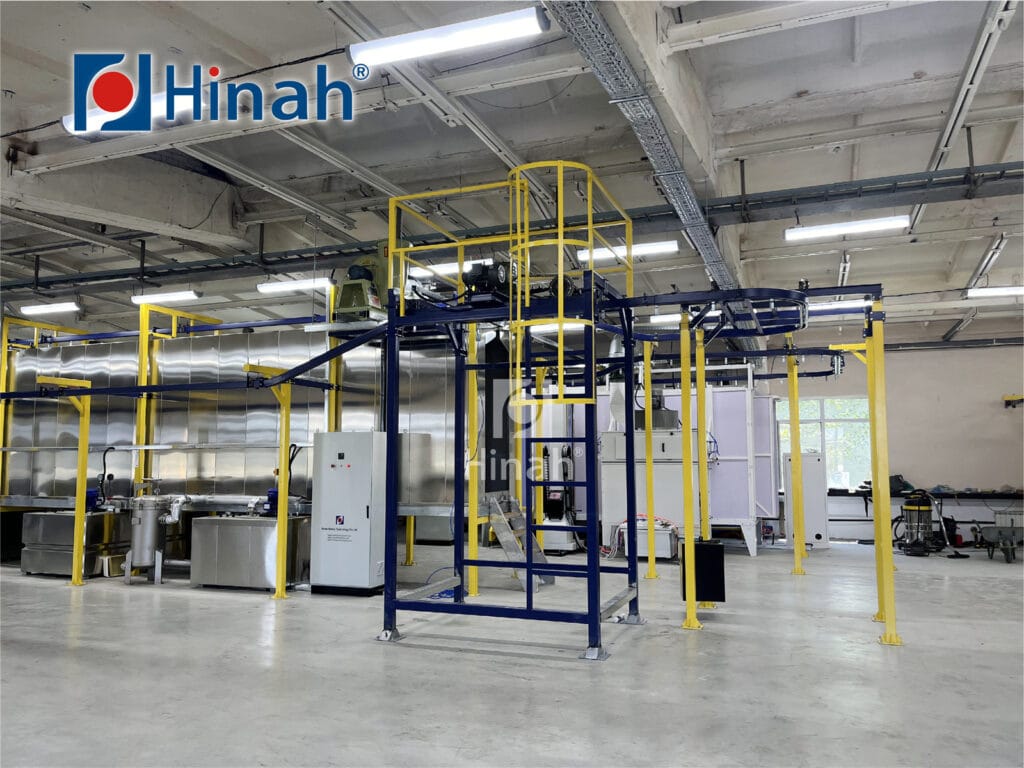
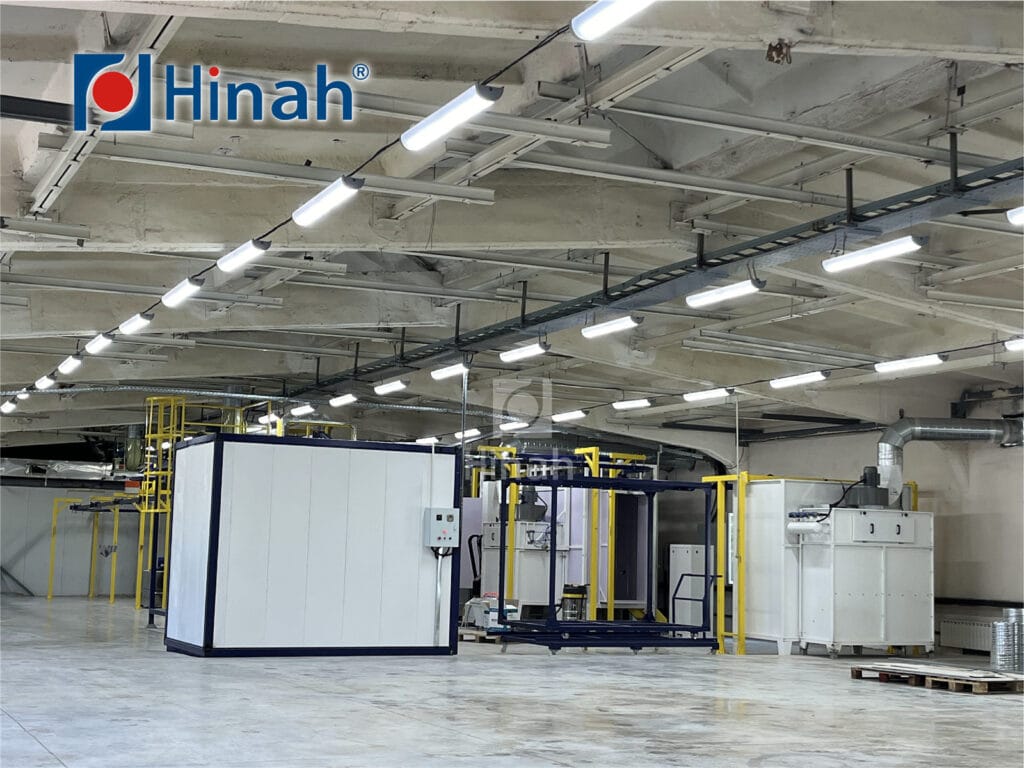
V. Better Compatibility with Automated Systems
When you’re planning for the future—or just trying to stay ahead in the present—automation is no longer optional. It’s a competitive edge. And here’s the good news: a horizontal powder coating line is built to work seamlessly with automated systems.
Powder coating robot arms? Automatic powder coating guns? Smart control software that adjusts spray patterns and curing times in real time? This setup is ready for it all. The horizontal orientation offers clear, consistent part positioning—exactly what automation systems need to perform at their best.
The result?
Faster cycle times.
Fewer errors.
Lower labor costs.
And beyond the numbers, there’s a real shift on the floor. Instead of chasing after inefficiencies, your team can focus on quality control, continuous improvement, and higher-value work. It’s not just about automation—it’s about freeing up your people to do what humans do best.
In the end, this isn’t just a smarter line. It’s a smarter way to grow.