With the advent of Industry 4.0, the manufacturing sector is undergoing unprecedented transformation. Intelligentization, digitalization, and automation have become new development trends, driving continuous progress across various industries. In this wave of change, automated powder coating technology has gradually emerged as a critical component in manufacturing due to its advantages in efficiency, precision, and environmental friendliness.
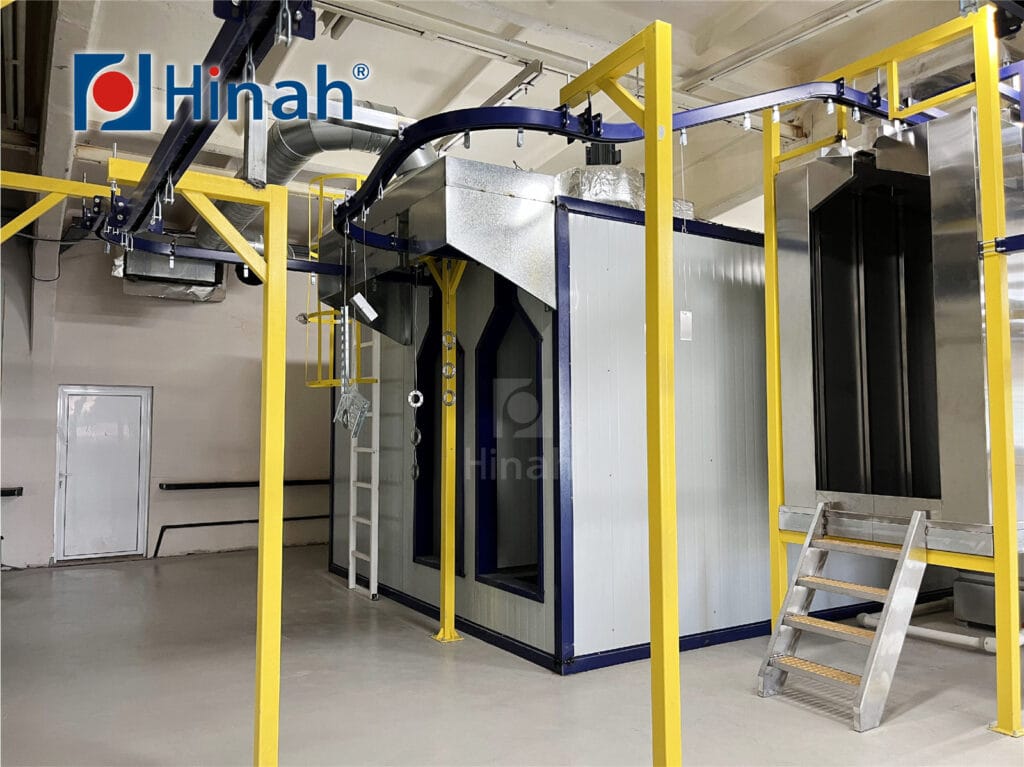
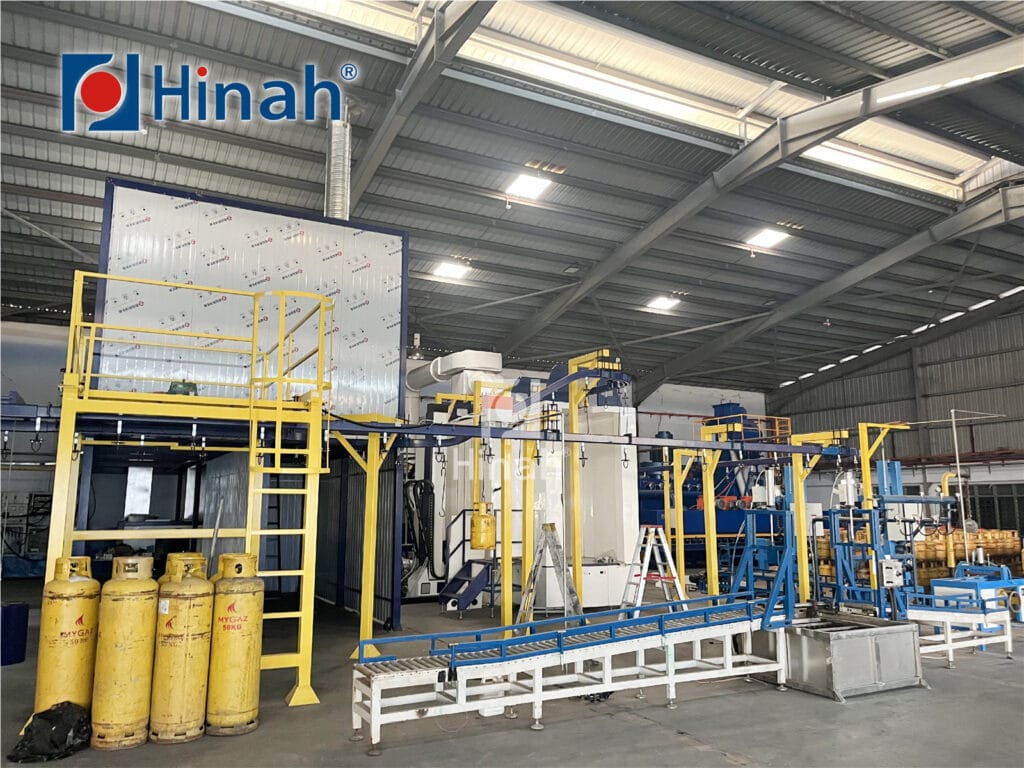
Technological innovation of automated powder coating
1. Technical principles and core equipment
From electrostatic spray guns to intelligent control systems
Automated powder coating uses the principle of electrostatic adsorption to make powder coatings evenly adhere to the surface of the workpiece. The electrostatic spray gun charges the paint particles and creates an attraction with the coated object, thereby ensuring a uniform and stable coating. The curing process solidifies the coating through high temperature to form a strong and durable surface. The intelligent control system further optimizes this process, adjusts the spraying parameters, curing temperature, etc., to ensure that the entire coating process is efficient and accurate.
Key equipment
The powder coating robot is one of the core equipment of automated powder spraying. Through precise movement paths and spraying control, it can achieve uniform spraying of every corner of the workpiece. The powder recovery system can collect excess powder and recycle it, improve resource utilization and reduce production costs. Dynamic contour scanning technology scans the surface of the workpiece in real time to accurately adjust the spraying angle and spraying amount to meet various complex coating requirements.
2. Three breakthroughs in intelligent upgrading
- High-precision spraying
Advanced sensors and algorithms can monitor the thickness and uniformity of the coating in real time during the spraying process. The sensor measures the coating thickness, and the algorithm analyzes the data and adjusts the spraying parameters to ensure that each layer of coating meets the requirements and improves the coating quality.
- Dynamic adjustment without programming
The automated powder coating system does not require the traditional programming process, but relies on intelligent algorithms to automatically plan the spraying path according to the real-time contour of the object. This technology reduces manual intervention, improves production efficiency and accuracy, and can quickly adapt to workpieces of different shapes.
- Powder recovery rate exceeds 95%
The automated powder coating system has achieved a recovery rate of more than 95% in powder recovery, which not only greatly reduces material waste, but also effectively reduces environmental pollution. This environmental advantage enables companies to reduce costs while complying with increasingly stringent environmental regulations and improving the sustainability of production.
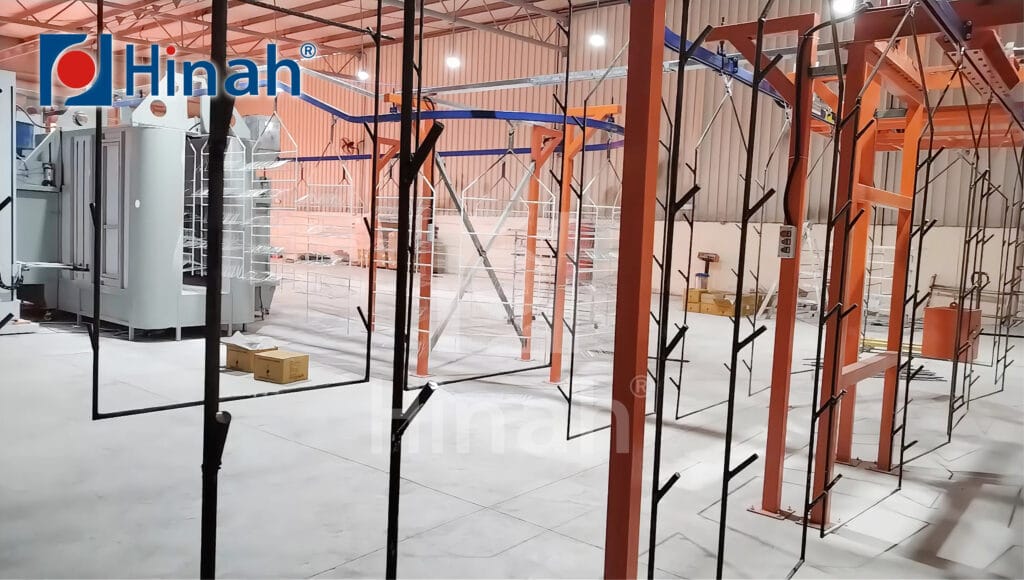
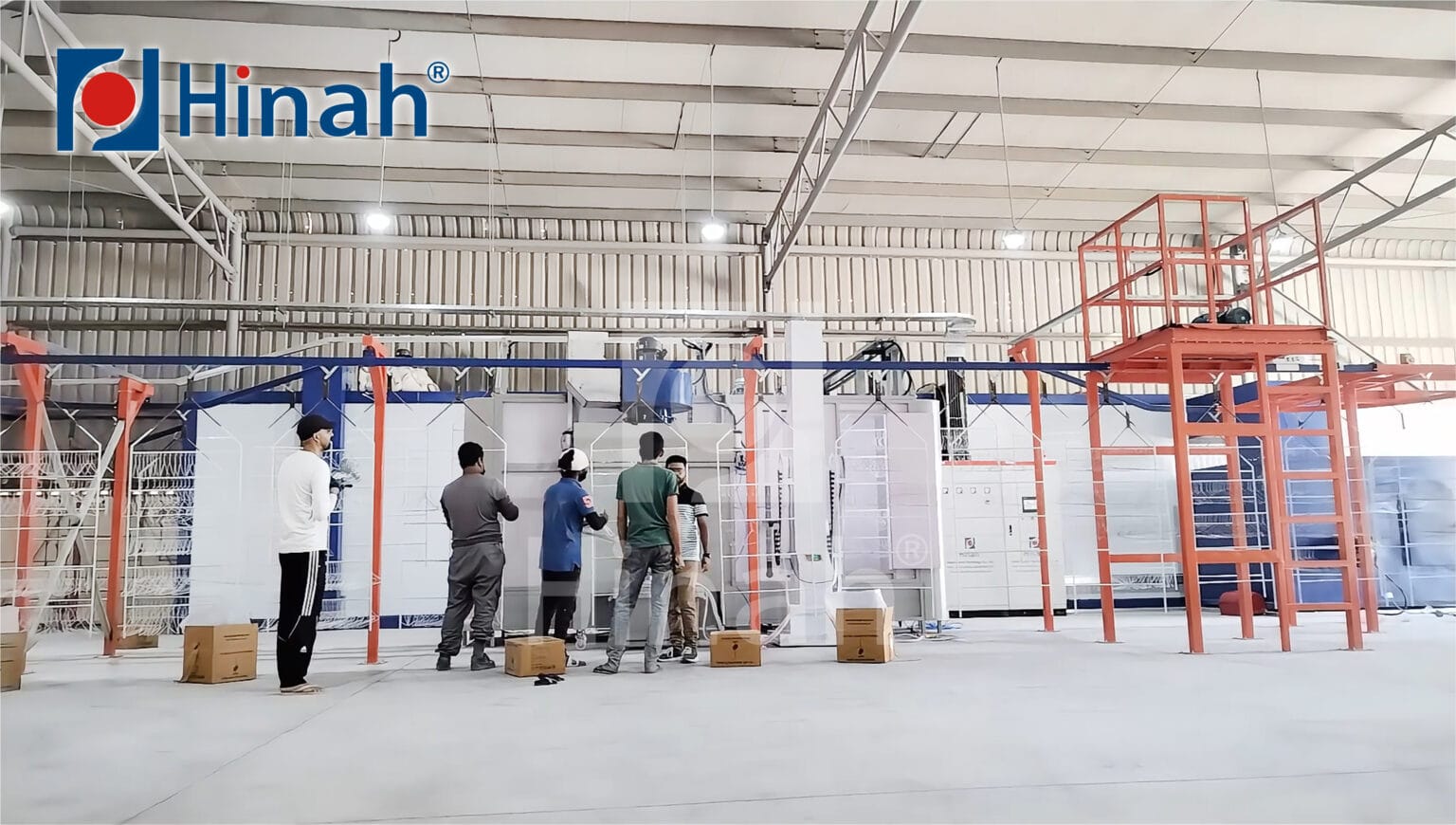
Precision and consistency: the advantages of automated powder coating
Automated powder coating technology can ensure the consistency and quality of the coating through advanced control systems and precision mechanical equipment. Compared with traditional manual spraying, the automated system can accurately control the angle, speed and amount of powder spraying, so that each product can be evenly coated with powder coating. This precise control not only improves the appearance quality of the product, but also ensures the uniform thickness of the coating, and enhances the durability and adhesion of the coating.
In addition, automated powder coating greatly reduces the occurrence of human errors. The traditional manual spraying process is easily affected by the experience and skills of the operator, resulting in uneven coating or omissions. The automated system ensures that each link is executed in accordance with the standard through preset programs and real-time monitoring, avoiding quality fluctuations caused by human factors. Automated coating not only improves the stability of production, but also improves the reliability in mass production, reduces rework and waste of resources, and helps companies gain an advantage in the competition.
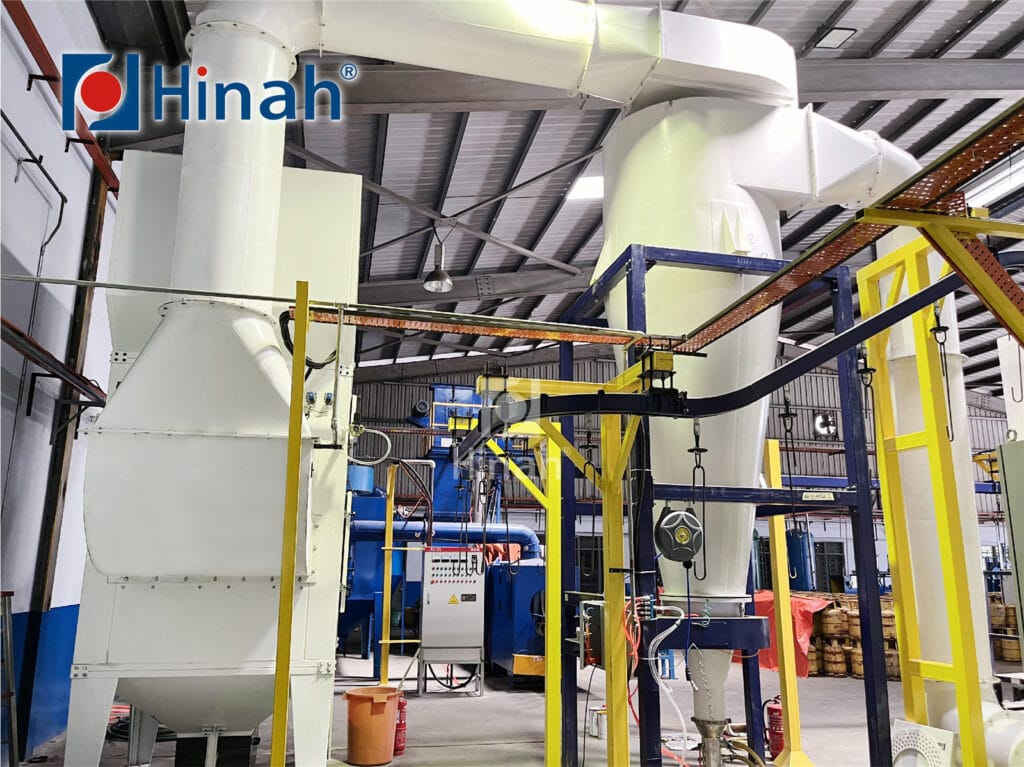
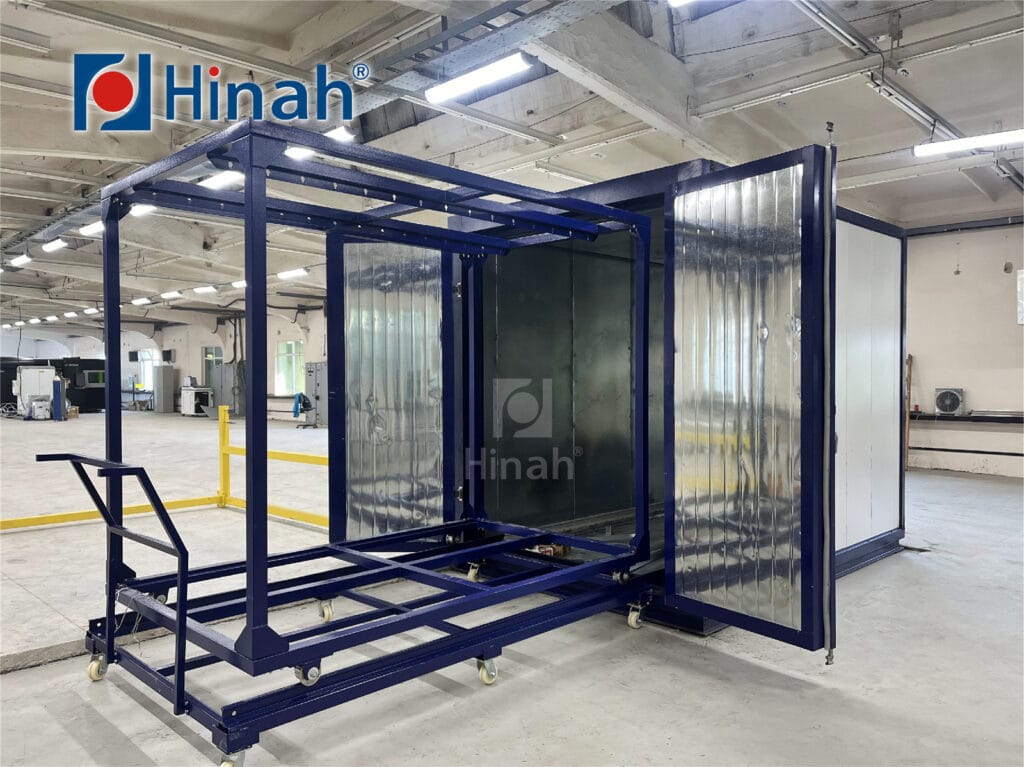
Environmental impact: The green revolution of automated powder coating
Automated powder coating technology effectively reduces the emission of volatile organic compounds (VOCs) by using powder coatings instead of traditional liquid coatings. VOCs are common harmful components in liquid coatings and have serious effects on air quality and human health. In contrast, powder coatings do not require solvents, so there is no VOC emission, which not only reduces environmental pollution but also avoids the generation of toxic gases. In addition, the precise control of automated powder coating minimizes the waste of powder coatings, improves material utilization, and reduces the generation of waste.
Powder coatings themselves also have environmental advantages. It is not only non-toxic and harmless, but also has zero solvent emissions during use, avoiding the pollution of harmful chemicals commonly found in traditional coatings. At the same time, powder coatings can be completely recycled and reused, which not only reduces the waste of raw materials, but also further reduces production costs. For the manufacturing industry, the use of automated powder coating technology can help enhance the green image of the enterprise, meet more stringent environmental regulations, and meet the needs of sustainable development.
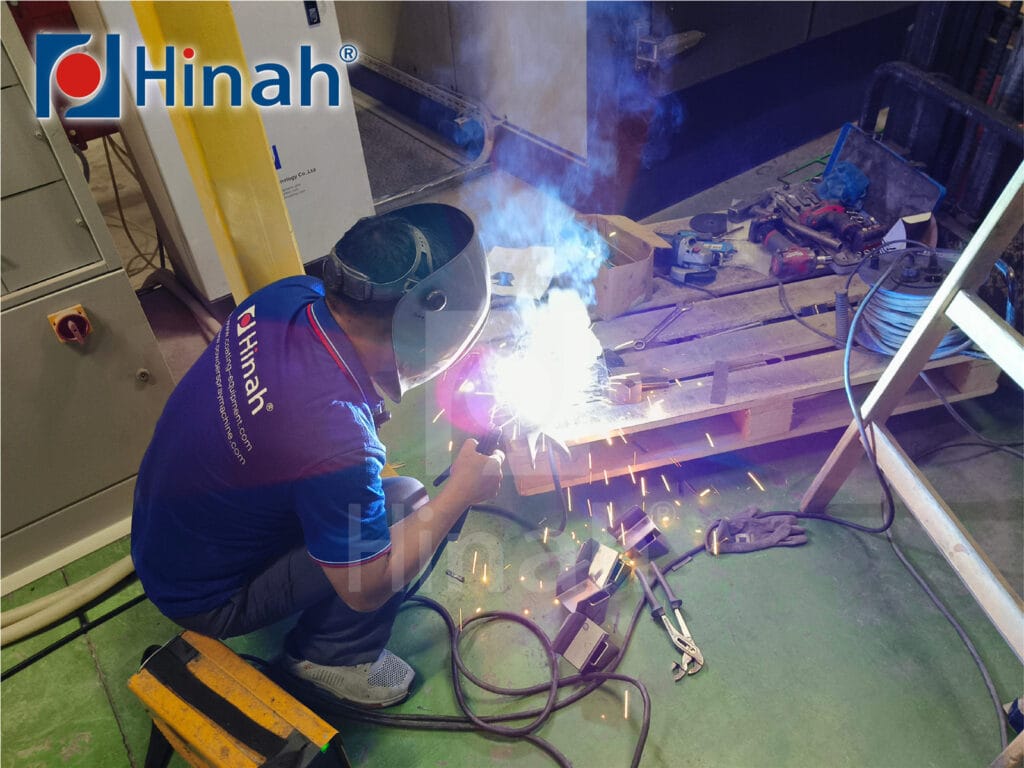
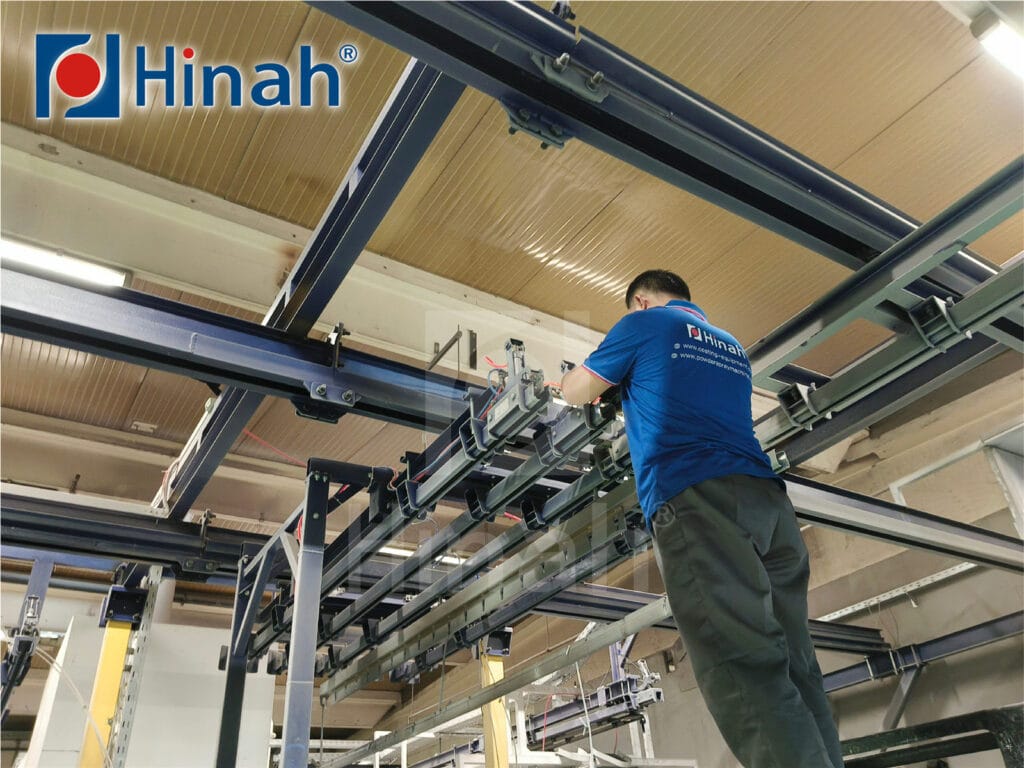
Conclusion
The application of automated powder coating technology in the manufacturing industry not only improves production efficiency, but also significantly improves coating quality and consistency. The introduction of this technology has changed the traditional manual spraying method, making the production process more precise and controllable, and greatly reducing manual errors and waste. For the manufacturing industry, automated powder coating is not only a tool to improve productivity, but also a catalyst to promote technological innovation and industry progress.