As industries from automotive to aerospace seek faster, safer, and greener finishing solutions, the powder coating booth has evolved from a basic enclosure to a high-tech hub of efficiency. Early designs prioritized functionality over safety, often leading to wasted materials, slow throughput, and risks like dust explosions. Today’s advanced powder coating booths break this compromise, merging intelligent technologies to accelerate production while meeting stringent OSHA and environmental standards. This transformation isn’t just technical—it’s redefining how manufacturers balance speed, safety, and sustainability in an increasingly competitive landscape.
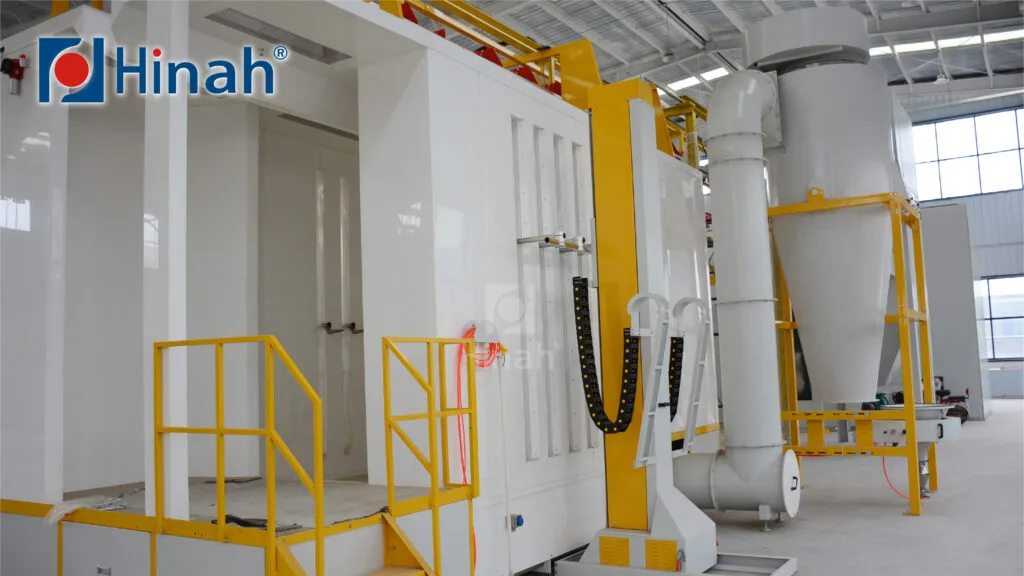
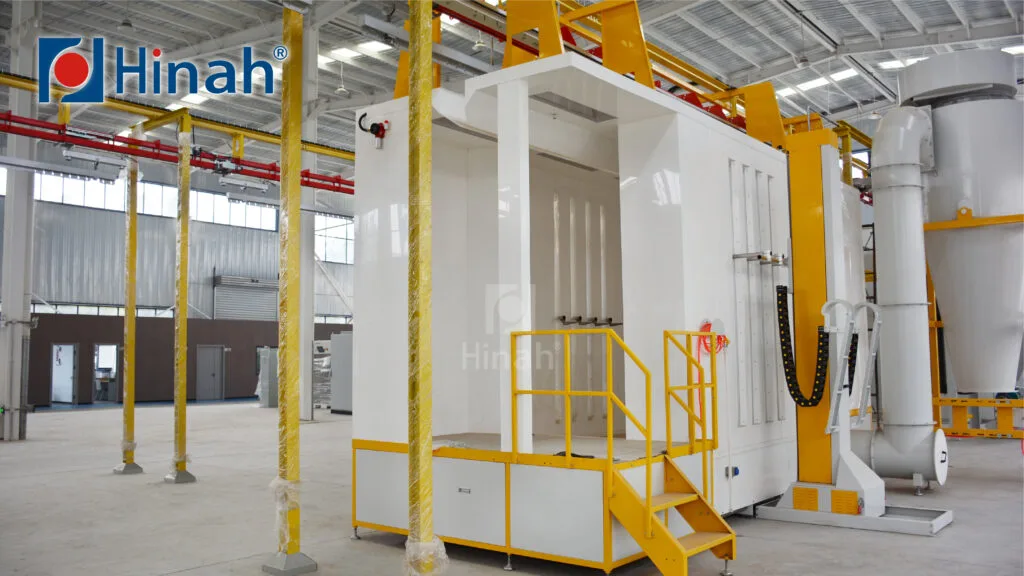
I. Why Speed & Safety Matter in Automatic Powder Coating Line
In the automatic powder coating line, speed and safety are two essential factors that directly impact production efficiency and quality. A well-optimized system ensures high throughput by reducing coating time while maintaining consistent application. Faster processing allows manufacturers to meet tight deadlines and lower operational costs, but excessive speed without precision can lead to uneven coatings and material waste. Therefore, advanced powder coating booths are designed to balance efficiency with accuracy, ensuring uniform coverage and minimizing rework.
At the same time, workplace safety is crucial, as powder coating involves electrostatics, airborne particles, and high-temperature curing. A well-designed booth integrates features like proper ventilation, filtration, and fire prevention to protect workers and maintain compliance with safety regulations. Neglecting these measures can lead to equipment failures, health risks, and costly downtime. By prioritizing both speed and safety, manufacturers can maximize productivity while ensuring a reliable and secure working environment.
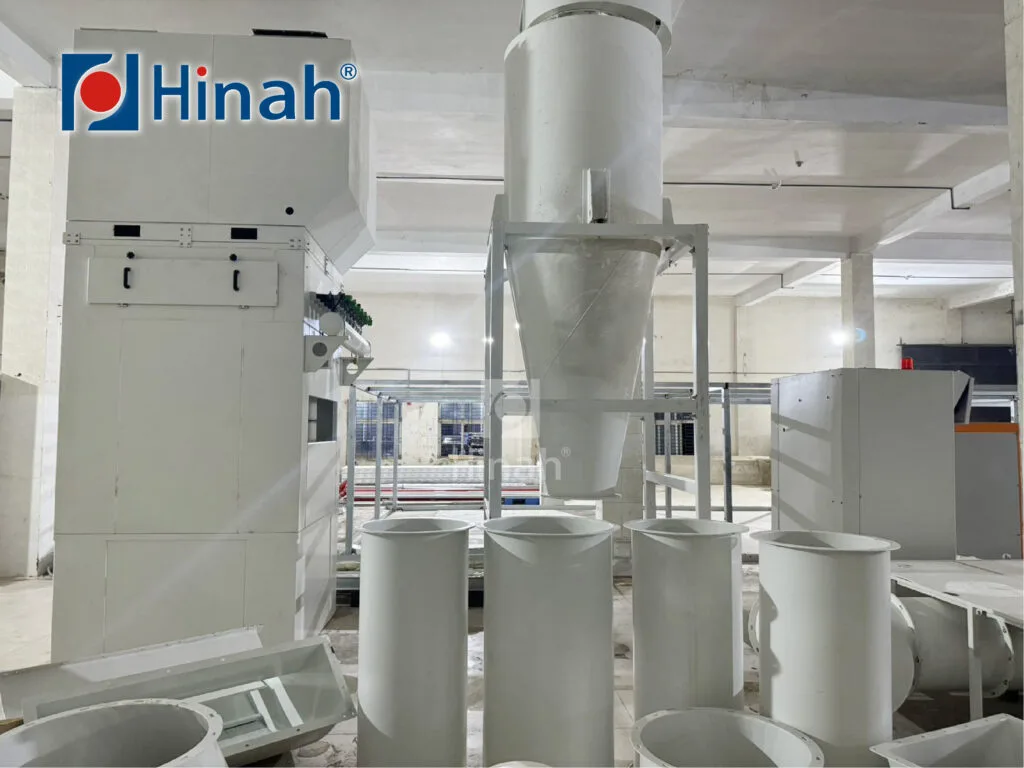
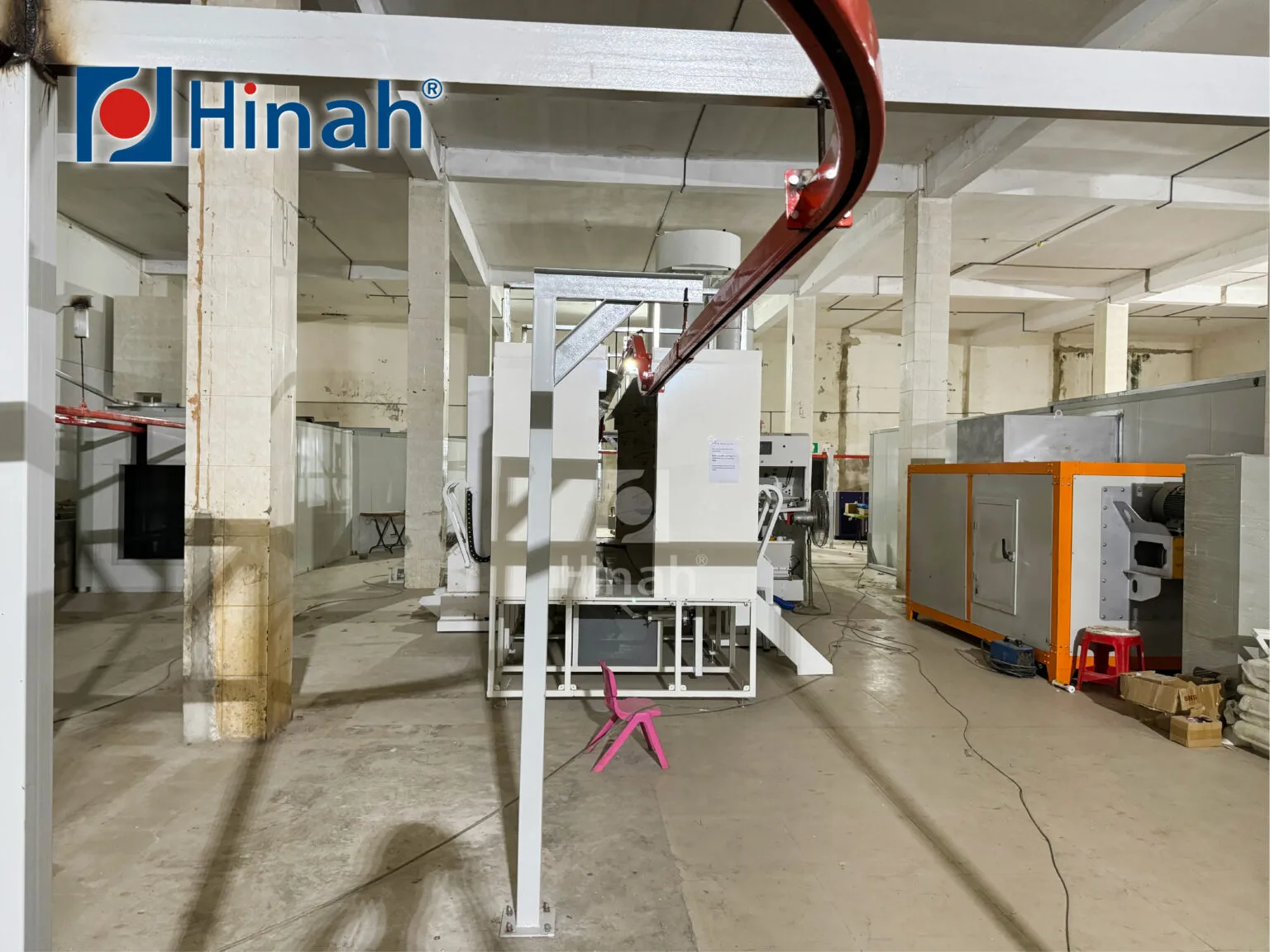
II. Key Features of Modern Powder Coating Booth
Streamlined Operation
Modern powder coating booth integrates automation to enhance efficiency and reduce manual intervention. The entire process—from workpiece cleaning and hanging to spraying—is seamlessly connected, ensuring smooth and efficient workflow. Adjustable rotating platforms at turns improve flexibility, allowing workpieces to move easily through the system. Additionally, continuous operation ensures that once one workpiece is coated, the next immediately enters the booth, minimizing idle time and maintaining a steady production pace.
High Spraying Efficiency
A well-designed powder coating booth optimizes batch processing with a spacious spray chamber that accommodates multiple workpieces simultaneously. This multi-piece coating capability significantly reduces individual coating time, increasing overall throughput. The efficient layout and automated controls ensure uniform powder distribution, reducing material waste and improving coating consistency across all products.
Enhanced Safety and Environmental Protection
Safety is a priority in modern powder coating booths. Advanced dust control systems prevent powder particles from escaping, reducing the risk of inhalation and ensuring compliance with workplace health standards. The enclosed design minimizes airborne contamination, creating a cleaner and safer work environment while also reducing the environmental impact of the coating process. These features help manufacturers meet both production and regulatory requirements efficiently.
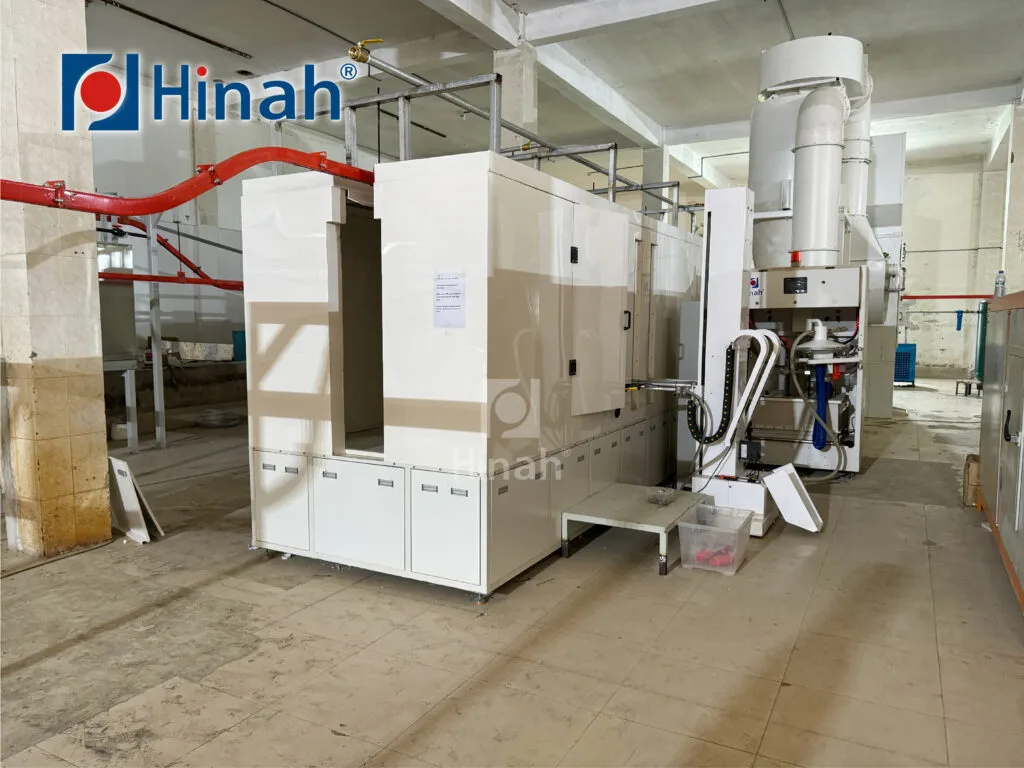
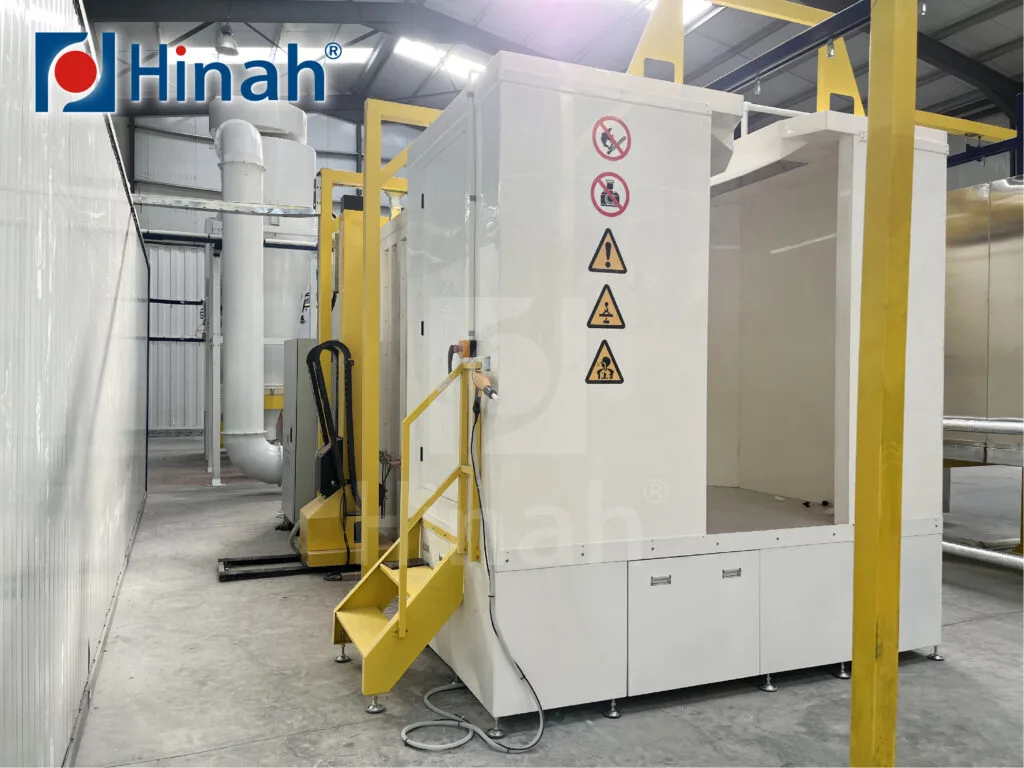
III. Maintenance Tips to Maximize Powder Coating Booth Performance
1. Regular Cleaning and Powder Recovery
Accumulated powder residue can affect spraying efficiency and booth airflow. Regularly clean booth walls, floors, and recovery systems to prevent powder buildup. Ensure that filters and cyclone separators function properly to maintain optimal powder recovery rates and reduce waste.
2. Inspect and Replace Filters
Filtration systems play a crucial role in maintaining air quality and preventing contamination. Check primary and secondary filters frequently, replacing clogged or damaged filters as needed. A well-maintained filtration system enhances worker safety and ensures consistent coating quality.
3. Check Conveyor and Ventilation Systems
The conveyor system should operate smoothly to avoid uneven coating due to inconsistent workpiece movement. Lubricate moving parts and inspect for wear. Additionally, ensure that ventilation systems function efficiently to control airflow, prevent overspray, and maintain a clean working environment.
4. Monitor Spray Guns and Nozzles
Powder coating guns and nozzles can become clogged or worn over time, affecting spray patterns and powder distribution. Regularly inspect and clean them to ensure precise application and minimize material waste. Replace damaged components promptly to maintain coating uniformity.
5. Calibrate Equipment for Optimal Performance
Periodic calibration of electrostatic settings, conveyor speed, and powder flow rates ensures that the booth operates at peak efficiency. Adjustments should be made based on workpiece size, coating thickness requirements, and environmental conditions to achieve the best results.
By implementing these maintenance practices, manufacturers can extend equipment lifespan, improve coating quality, and maintain a safe, efficient powder coating process.
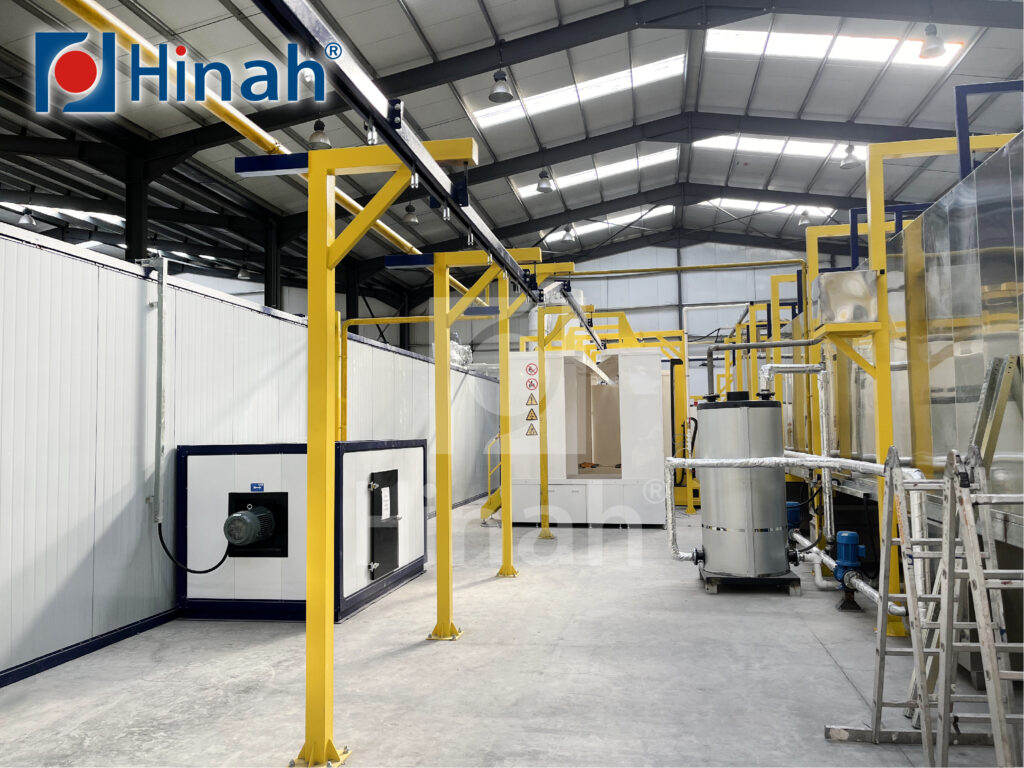
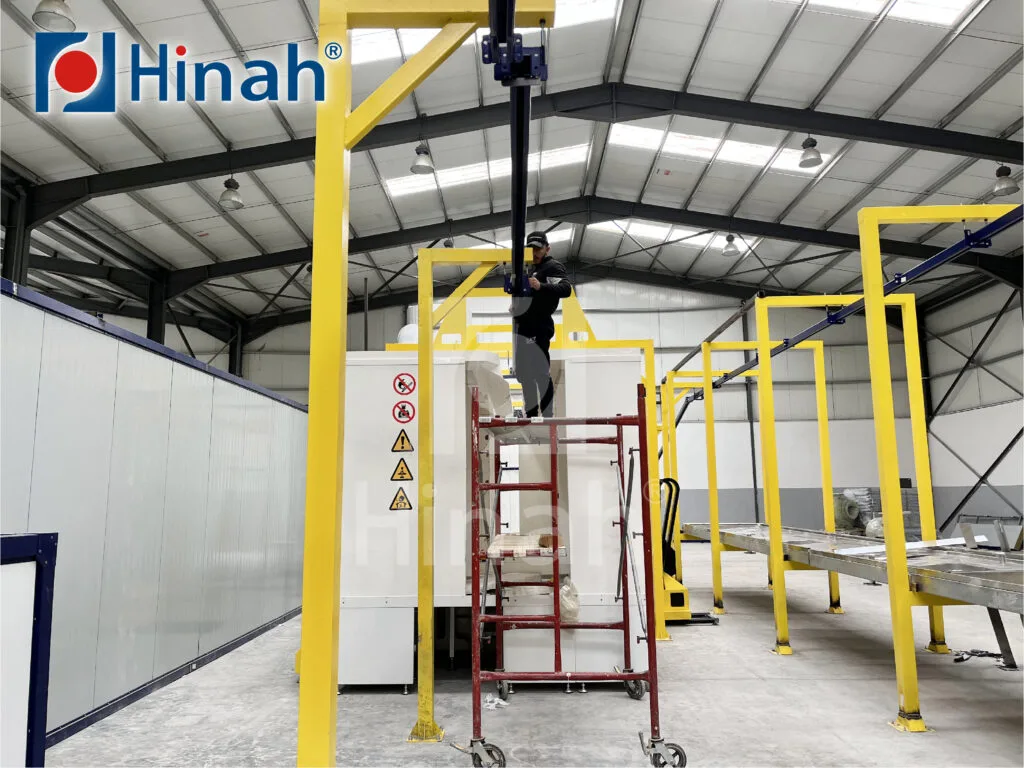
Conclusion
A modern powder coating booth is essential for achieving high-efficiency, high-quality, and safe coating operations. By optimizing speed and safety, integrating advanced features, and following proper maintenance practices, manufacturers can maximize productivity while ensuring consistent coating results. Regular upkeep, including cleaning, filter inspection, and equipment calibration, helps extend the booth’s lifespan and maintain peak performance. Investing in a well-designed and well-maintained powder coating system ultimately leads to cost savings, improved product quality, and a safer working environment.