Powder coating line is the backbone of modern surface finishing, delivering durable, eco-friendly, and visually appealing results for everything from automotive parts to household appliances. While configurations may vary depending on production scale and automation levels, all powder coating lines rely on seven core components working in harmony. Below, we explore these essential elements and their roles in achieving a flawless finish.
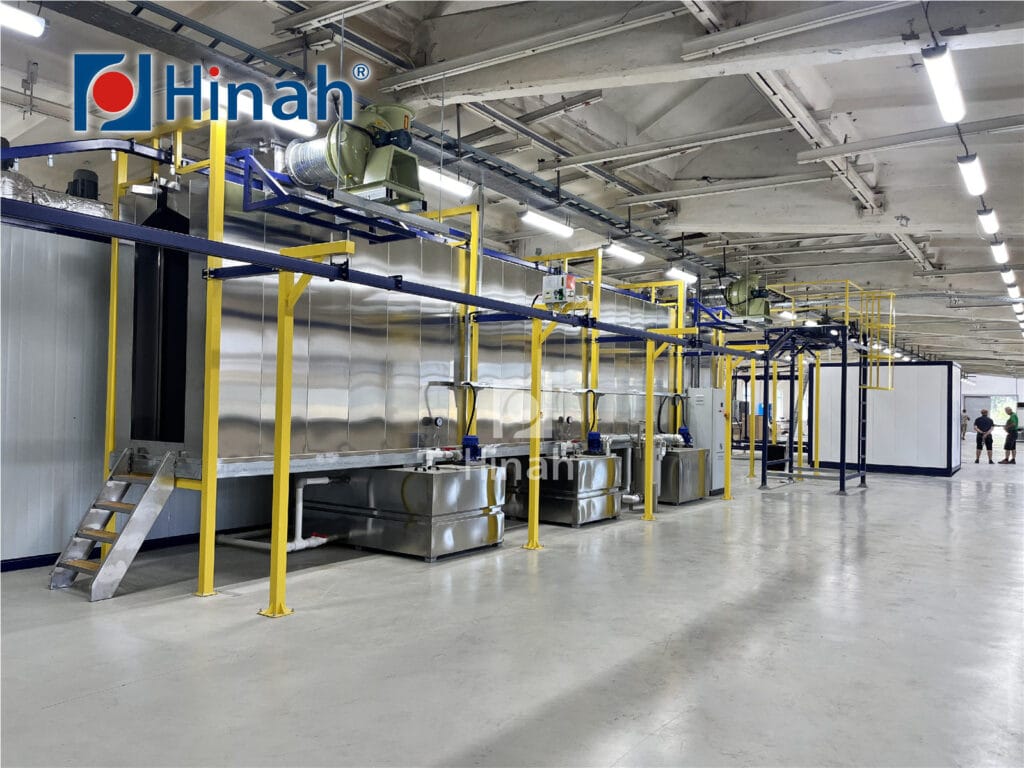
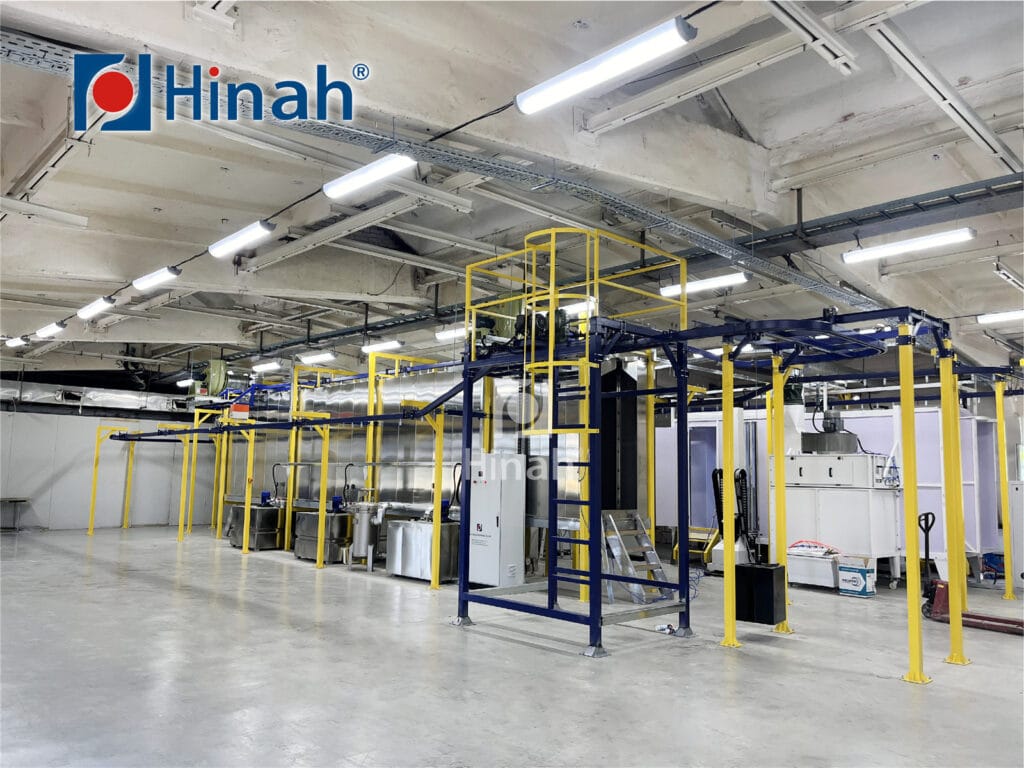
1. Pretreatment System: The Cornerstone of Quality
The pretreatment system is the unsung hero of any powder coating line. Its primary function is to prepare the substrate by removing contaminants like oils, grease, rust, and dirt. Skipping or rushing this step risks coating failures such as peeling, blistering, or poor adhesion.
A comprehensive pretreatment process typically includes degreasing with alkaline or acidic solutions, thorough rinsing to eliminate chemical residues, and surface activation through phosphating or chromating. This final step creates a microscopically textured layer that improves powder bonding. Automated powder coating lines often use spray or immersion methods with precise temperature and chemical controls, while smaller operations may rely on manual pretreatment. Regardless of the approach, the goal remains the same: a clean, chemically prepared surface ready for coating.
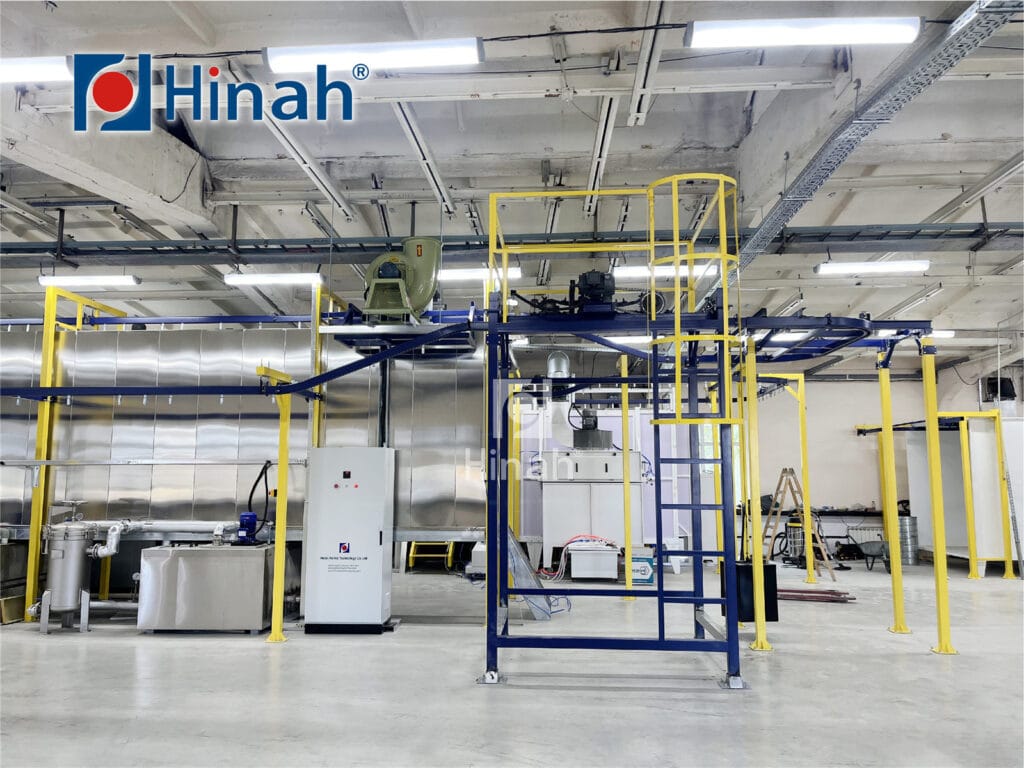
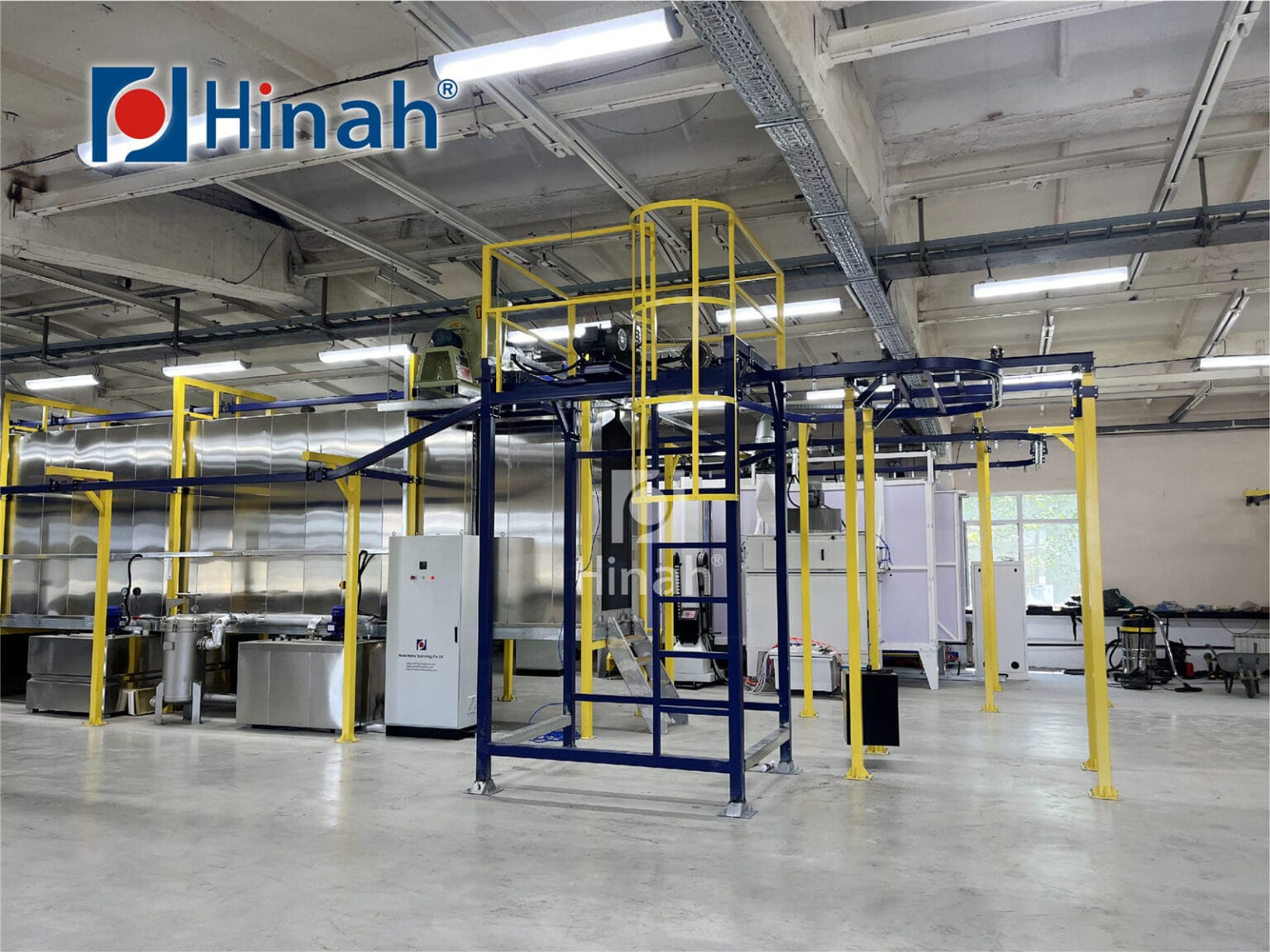
2. Dry-Off Oven: Eliminating Hidden Threats
After pretreatment, parts are often left with residual moisture. Even minimal water traces can disrupt powder adhesion, leading to clumping or uneven coverage. The dry-off oven addresses this by gently heating parts to temperatures between 150°F and 200°F, evaporating moisture without prematurely activating the powder. Modern ovens prioritize energy efficiency, using optimized airflow designs to ensure rapid, uniform drying. This step guarantees that parts enter the coating phase completely dry—a non-negotiable requirement for consistent results.
3. Powder Application Booth: Where Coating Meets Precision
The powder application booth is where the coating process truly begins. Electrostatic spray guns charge powder particles, which are then attracted to the grounded substrate, forming an even layer. In automated lines, robotic arms or reciprocators ensure consistent coverage, even on complex shapes. Manual systems, meanwhile, depend on skilled operators to achieve similar results.
Critical features of a powder booth include:
Electrostatic guns for optimal particle charging.
Airflow systems to capture overspray and maintain a clean environment.
Lighting and visibility for quality control during application.
Advanced booths may incorporate quick-color-change technology, reducing downtime when switching between powder types.
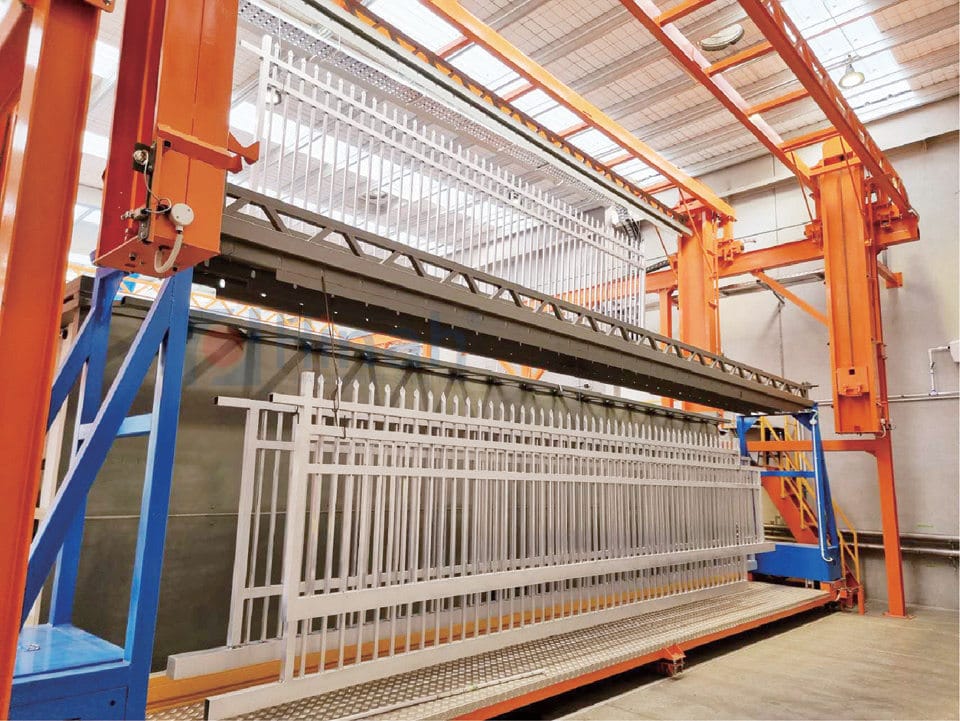
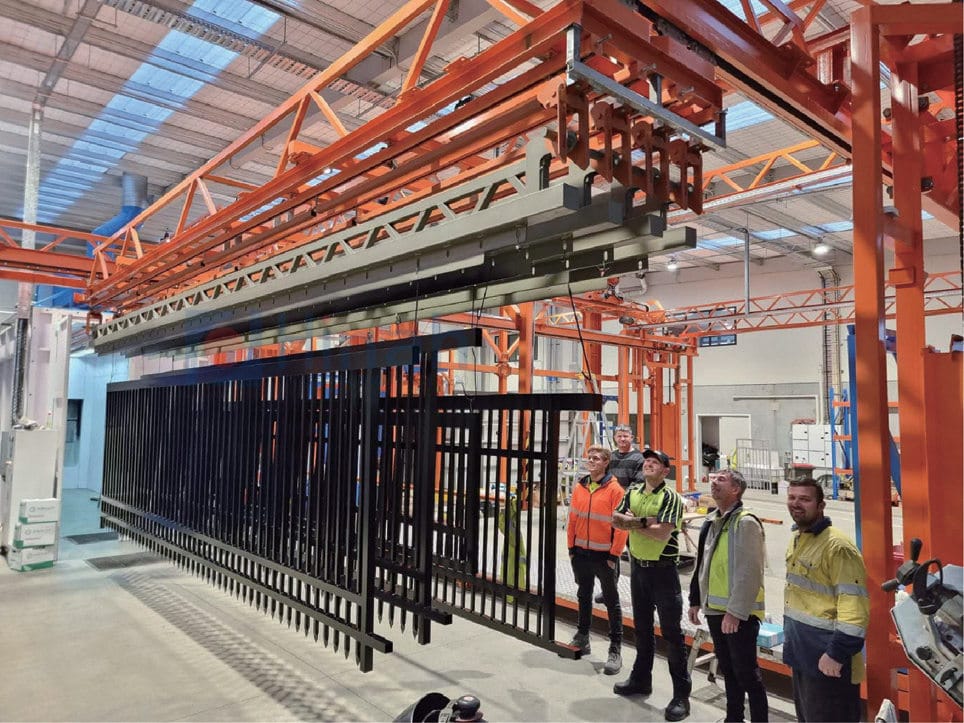
4. Curing Oven: The Final Transformation
The curing oven is where the powder coating achieves its signature durability and finish. Parts are heated to 300–450°F, causing the powder to melt, flow, and chemically bond into a smooth, resilient layer. Uniform heat distribution is critical; uneven temperatures can lead to incomplete curing, resulting in weak spots or poor adhesion.
Modern curing ovens use convection or infrared heating, often paired with energy recovery systems to reduce fuel consumption. Some designs include multiple temperature zones to accommodate varying part thicknesses or materials. The result is a finish that withstands corrosion, UV exposure, and mechanical stress.
5. Conveyor System: The Lifeline of Efficiency
The conveyor system ensures seamless movement of parts through every stage of the coating line. Overhead conveyors are ideal for heavy or large items, while belt or chain-on-edge systems suit smaller components. In automated setups, conveyor speed is synchronized with pretreatment, drying, and curing times to avoid bottlenecks.
Key innovations include collision-avoidance sensors, variable speed controls, and modular designs that adapt to different part sizes. For manual or semi-automated lines, simplicity and reliability are prioritized to maintain steady workflow.
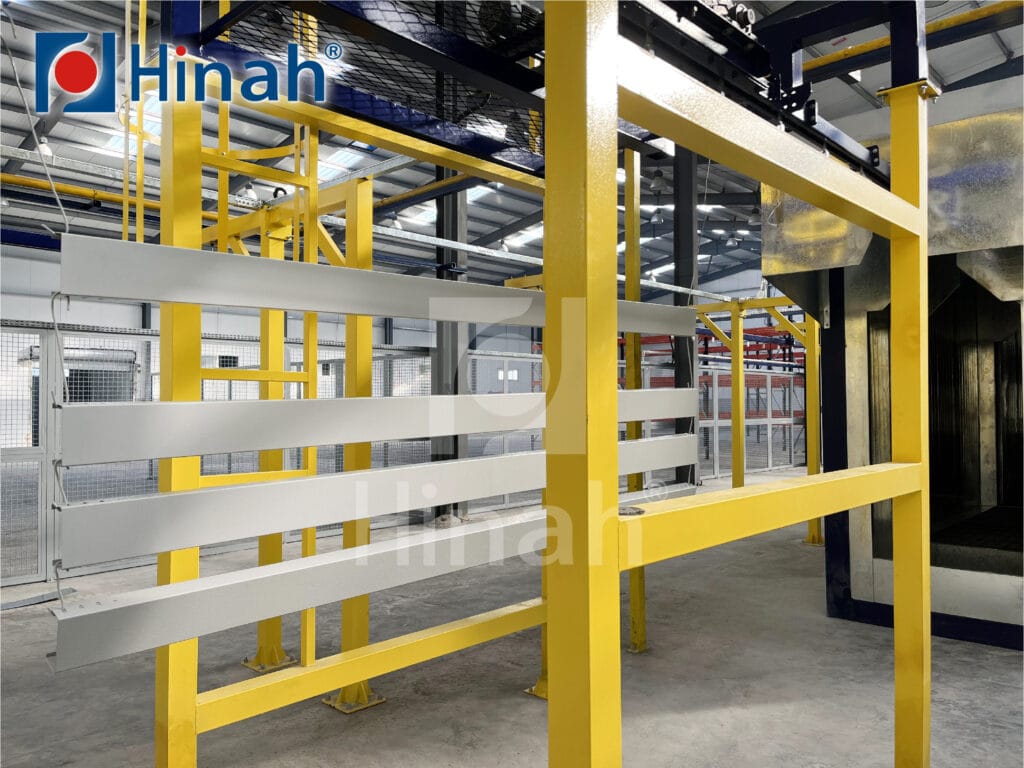
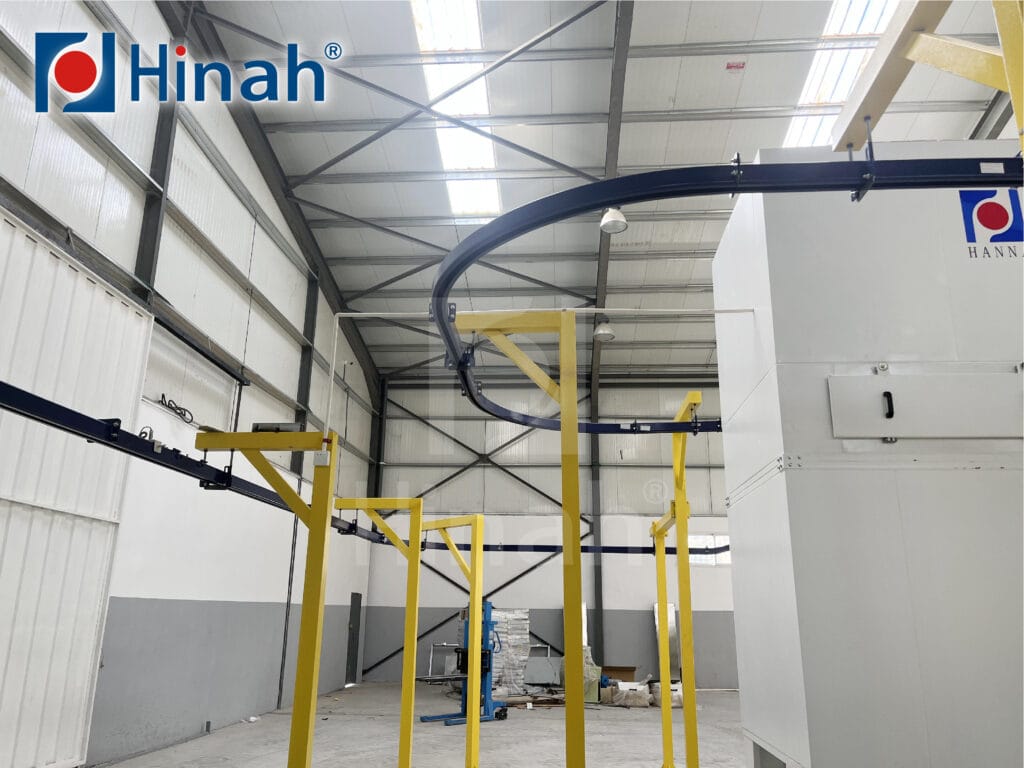
6. Powder Recovery System: Sustainability in Action
Powder coating’s eco-friendly reputation stems largely from its material efficiency. The powder recovery system captures up to 95% of overspray using cyclones, cartridge filters, or vibrating sieves. Reclaimed powder is filtered, blended with fresh material, and reused, drastically reducing waste and operational costs.
This system also minimizes environmental impact by limiting airborne particulates and landfill contributions. Advanced recovery units include real-time monitoring to track powder usage and optimize recycling rates.
7. Control System: The Brain Behind the Process
The control system acts as the nerve center of the powder coating line. In automated setups, Programmable Logic Controllers (PLCs) and Human-Machine Interfaces (HMIs) allow operators to adjust oven temperatures, conveyor speeds, and spray gun settings with precision. Sensors detect variables like part thickness or humidity, enabling real-time adjustments to maintain quality.
For smaller or manual lines, control systems may involve simpler interfaces or manual overrides. However, the principle remains consistent: centralized oversight ensures all components work cohesively. Emerging IoT-enabled systems take this further, offering predictive maintenance alerts and energy usage analytics.