Want to Discuss Your Upcoming Product Line?
Hinah coating will help you get things done.
Email us
Tel (Whatsapp/Wechat)
+86-186 3213 8668
Powder Coating Pretreatment System
Advanced technology, energy saving, high efficiency.
Pretreatment is a crucial step in the powder coating process, ensuring optimal adhesion and corrosion resistance of the coating to the substrate. Hinah offers top-of-the-line pretreatment equipment designed to meet the diverse needs of our customers. Our pretreatment solutions are available in two primary types: spray type and dip tank type.

Type1: Spray pretreatment
Advanced technology, energy saving, high efficiency.
- Spray pretreatment is a method of cleaning and treating the product surface by spraying cleaning agents and chemicals in the form of a spray through a spray nozzle.
- It usually uses a high-pressure water stream and the mechanical movement of the nozzle to achieve the spraying action.
Features
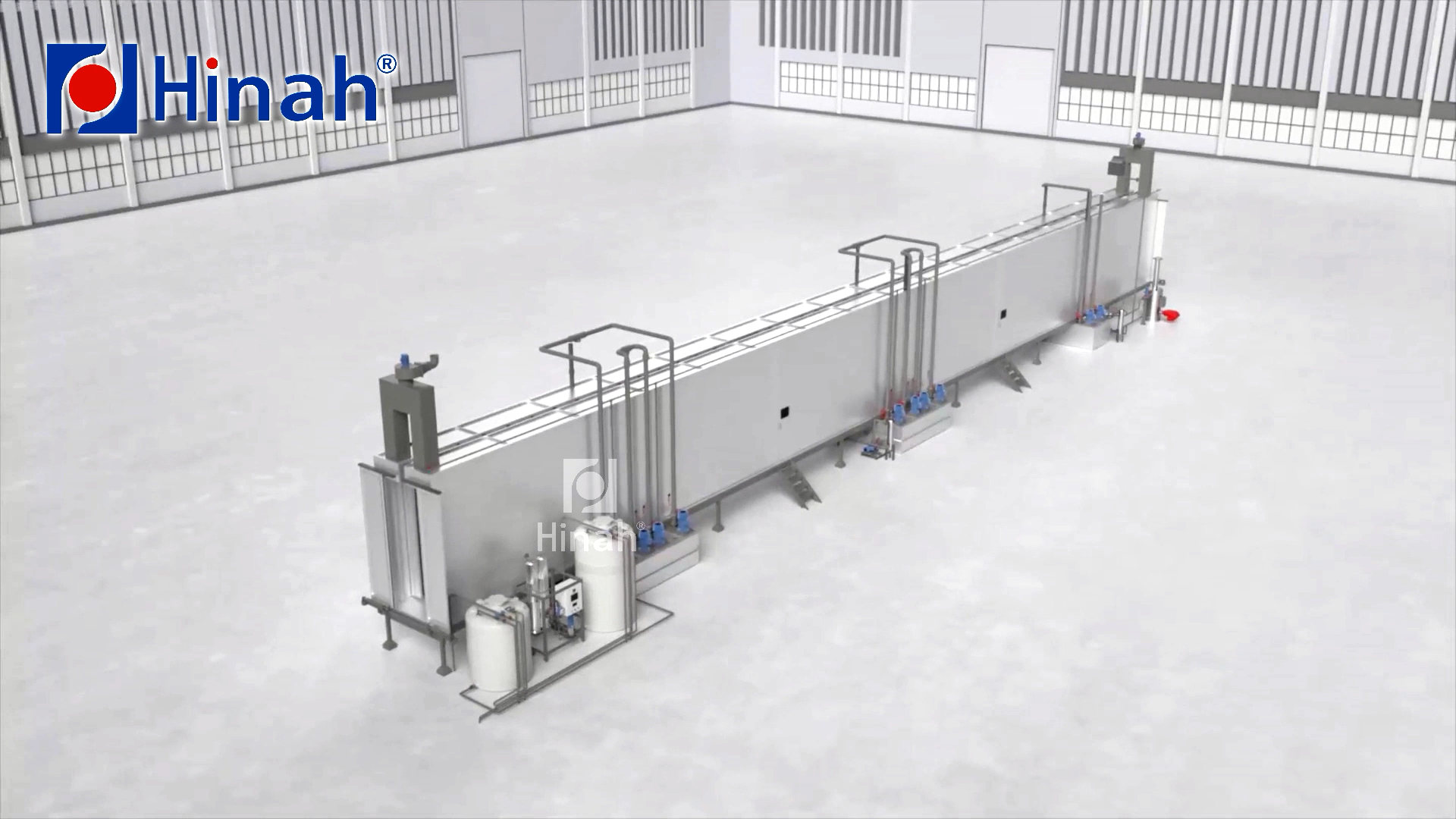
Spraying Pre-treatment
Spraying Pre-treatment before Powder Coating Line
- All Types Of Equipment For Powder Coating Lines
- Any Size According To Customer's Requirements
- Production Within 45-90 Days
- Delivery And Professional Installation
- 12 Months Warranty And Lifetime Service
Our spray-type pretreatment equipment is designed to apply pretreatment chemicals evenly and efficiently onto the surface of the workpiece. This equipment utilizes spray nozzles to disperse the pretreatment solution, covering the entire surface area with a fine mist. It offers flexibility in adjusting parameters such as spray pressure, flow rate, and chemical concentration to achieve optimal results for different substrates and coating requirements.
- Uniformity: Spray pre-treatment sprays the cleaning agent and treatment solution uniformly over the entire product surface, ensuring that every area is adequately cleaned and treated.
- Efficient: spray pre-treatment enables the cleaning and treatment process to be completed in a short time, making it suitable for high throughput production environments and increasing production efficiency.
- Flexibility: Spray pre-treatment can be adapted to different product shapes and sizes for a wide range of product types and sizes.
- Resource-saving: Compared to immersion tank pre-treatment, spray pre-treatment typically requires less cleaning agent and treatment fluid, thus reducing resource consumption.

Type2: Dip tank pre-treatment
Advanced technology, energy saving, high efficiency.
- Immersion tank pretreatment is a method of cleaning and treating products by complete or partial immersion in a pretreatment tank.
- Pretreatment tanks usually include alkaline cleaning tanks, pickling tanks phosphating tanks, etc. The product is left in the tank for a period to react and clean with the treatment solution.
Features
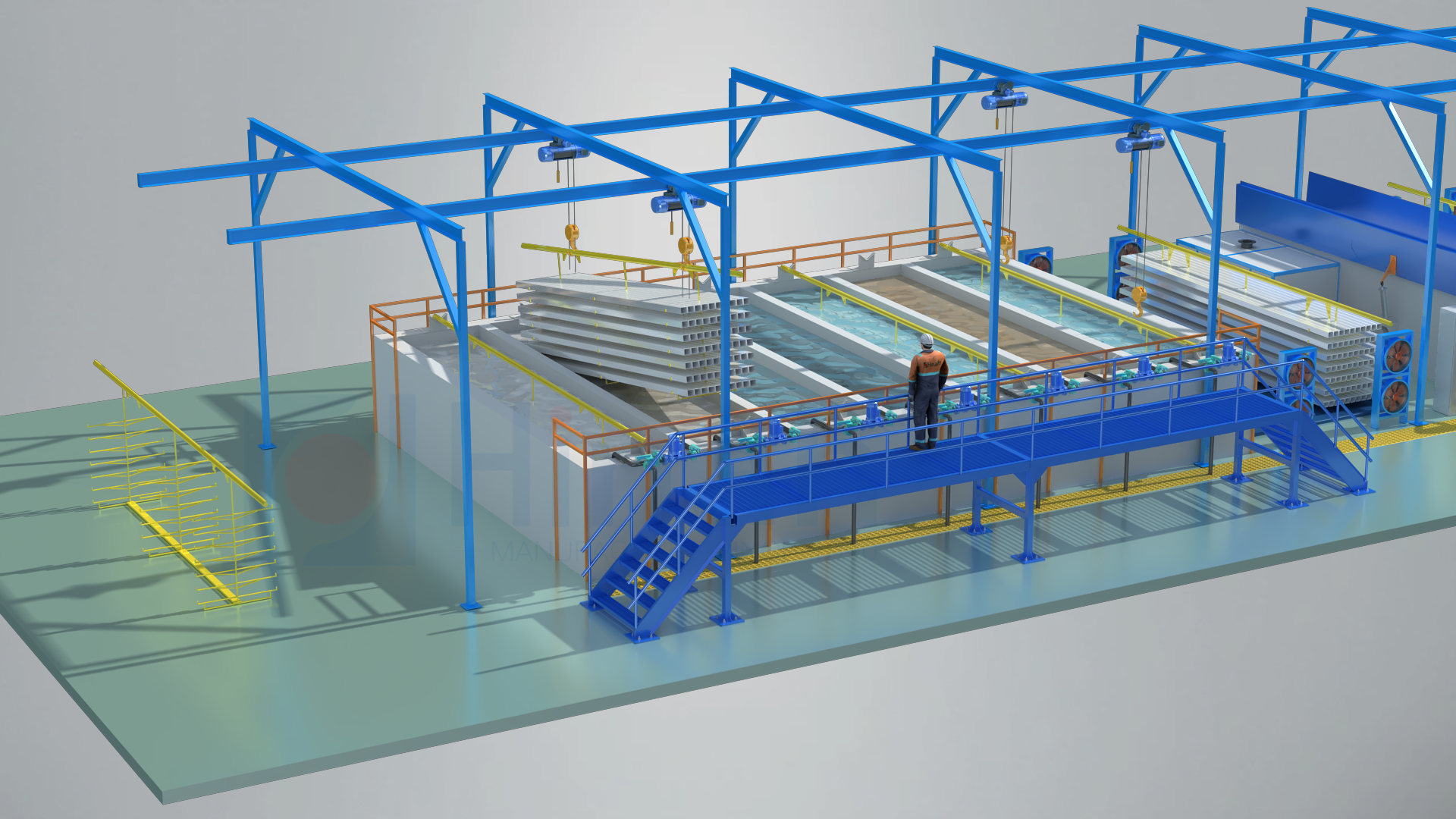
Dipping Pre-treatment
Dipping Pre-treatment before Powder Coating Line
- All Types Of Equipment For Powder Coating Lines
- Any Size According To Customer's Requirements
- Production Within 45-90 Days
- Delivery And Professional Installation
- 12 Months Warranty And Lifetime Service
- Thoroughness: The immersion tank-type pretreatment enables the product to be completely immersed in the treatment solution, ensuring that the treatment solution fully contacts every corner of the product surface and completely removes dirt and oxides.
- Stable treatment: Due to the long residence time of the product in the treatment solution, the immersion tank pretreatment allows for better control of the temperature, concentration, and reaction time of the treatment solution to achieve a stable treatment effect.
- Wide applicability: Immersion tank pretreatment is suitable for all types of products, especially for products with complex shapes and many holes, and can treat surface and internal dirt.
- Easy to operate: Immersion tank pre-treatment is relatively simple and easy to operate, simply place the product in the pre-treatment tank and wait for a certain amount of time to complete the treatment.
- Flexibility: Immersion tank pre-treatment is suitable for products of different shapes, sizes, and materials, offering a high degree of adaptability and flexibility. The composition of the treatment solution and the treatment time can be adjusted according to the requirements and treatment objectives of the different products in order to obtain the best possible pre-treatment results.
- Suitable for high-volume production: Immersion tank pretreatment is often suitable for large-scale production environments, allowing large numbers of similar products to be treated and increasing production efficiency.
- Long soak time results: Due to the long time the product spends in the treatment tank, soak tank pretreatment provides a more thorough removal of dirt and oxides from the product surface, providing better coating adhesion and durability.
- Configuration of multiple treatment tanks: Immersion tank pretreatment systems can be configured with as many treatment tanks as required, such as alkaline wash tanks, pickling tanks, phosphating tanks, etc., to enable multiple treatment steps to be carried out in succession. This can further improve the treatment effect and coating quality.
- It should be noted that spray and immersion tank pre-treatment each have their own advantages and the choice should be based on a combination of factors such as product characteristics, production requirements, and budget. In some cases it is possible to use a combination of both methods, for example, a spray pre-treatment for initial cleaning followed by an immersion tank pre-treatment for a more in-depth treatment.
Proven
30 years of experience providing proven equipment
Lifetime Service
Maintenance is more important than repair
Maximum Efficiency
Production line capacity fully matches demand without wasting any resources
Contact Us -- Free Design & Order Equipment Calculation
Order Equipment Calculation
● Factory Dimensions (length, width, height)
● Work Piece Output (1 day = 8 hours, 1 month = 30 days)
● Material of the workpieces
● Dimensions of work piece
● Weight of the workpieces
● Color Change Demand (Frequency)
In Order To Provide You With The Best Solution, Please Tell Us The Information
We closely communicate with clients to understand their needs and provide tailored solutions. Once the solution fits their requirements, we customize the production of the powder coating line to help them adapt to their specific production environment and coating needs.
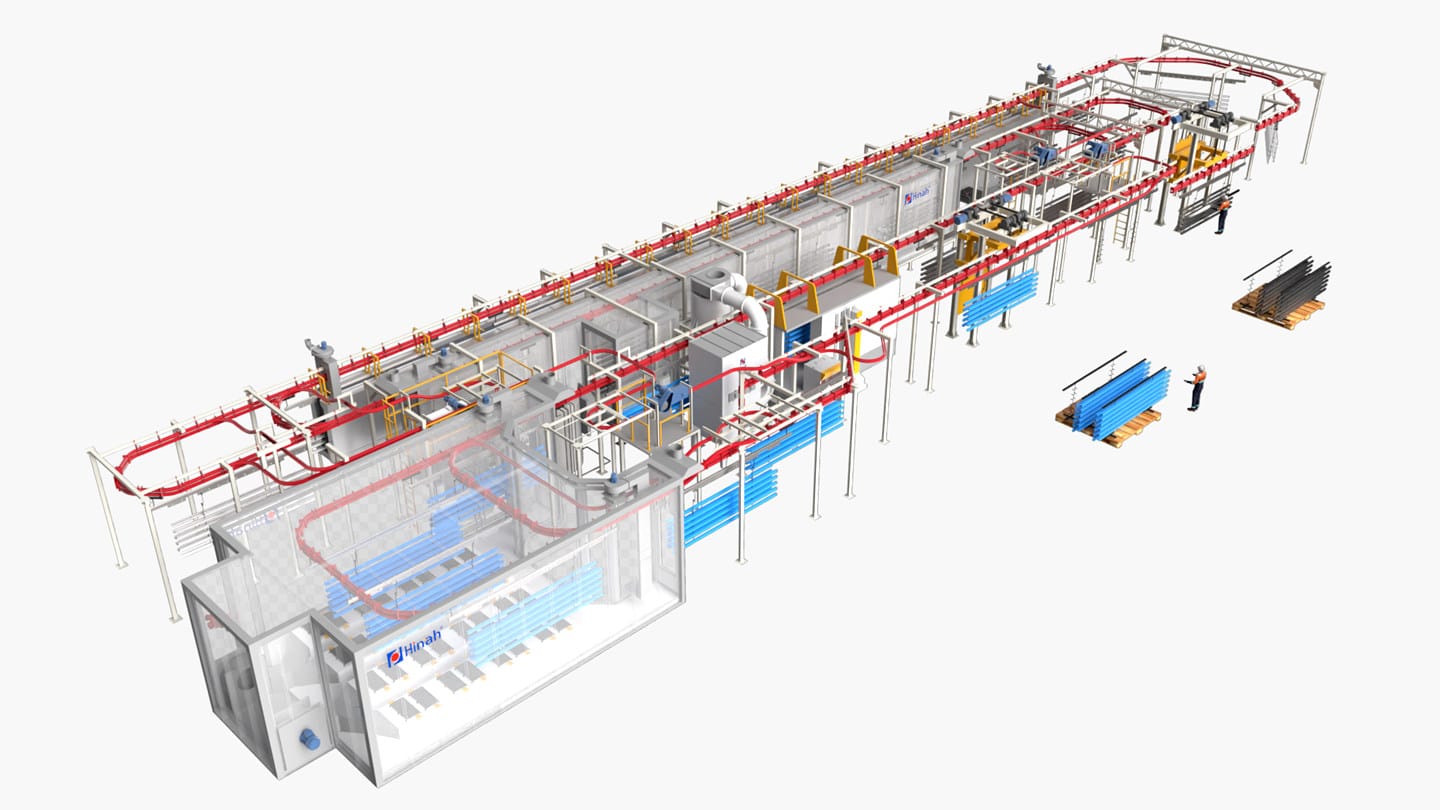
/CONTACT US
Want to Discuss Your Upcoming Product Line?
Hinah coating will help you get things done.
Email us
Tel (Whatsapp/Wechat)
+86-186 3213 8668
Learn How We Helped 1000+ Customers Gain Success.